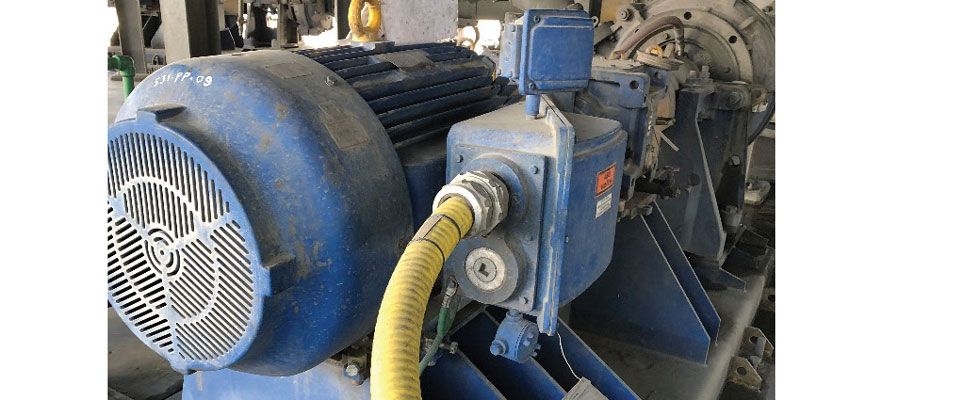
In many pumping applications today, there are multiple pumps involved in maintaining a single process value like pressure or flow. The benefits of using multiple pumps instead of one large pump are the size, cost, procurement lead time, system efficiency and inherent system redundancy. Multiple motors mean more controlling devices, including programmable controllers, offsetting some of the cost savings. The embedded application controls in variable frequency drives (VFDs) eliminate the need for a programmable controller, saving additional engineering hours and commissioning costs.
Here are answers to common questions that users may have on how VFD controls help with smart staging/destaging of multiple pumps to control process variables like pressure or flow.
1. What is meant by staging and destaging the multiple pumps in a pumping system/network?
In a pumping application, there could be multiple pumps in the same pumping network that are called to run based on the changes in the process. The VFD controls the motor of the first pump, varying the motor speed to control the pump’s output.
When the process demand exceeds the limit as gauged by the VFD proportional-integral-derivative (PID) controller, the drive controls automatically start the auxiliary pumps. These pumps are either using another VFD or the motors are started across the line. When they are started, they run at full speed to make up for the increased demand. Therefore, the speed of the VFD pump might decrease automatically, depending on the VFD’s PID controller. The auxiliary motors are stopped if the process demand falls below a certain level. The addition or removal of these auxiliary pumps by the master VFD in the pumping network is based on the VFD PID control algorithm, which is called smart staging and destaging of the VFDs in the pumping network.
2. Why would a pumping system need to use the staging and destaging control philosophy using a single VFD?
When the process demand increases either due to a change in the PID feedback or the setpoint, the PID output changes, which causes the VFD algorithm to stage or destage pumps in the pumping network. For example, the pressure in the pump line drops when many houses in the neighborhood start using water in the morning hours. At that time, the VFD PID tries to maintain line pressure by adding/starting more pumps in the system. When people in the neighborhood are done with morning chores, the demand decreases and the line pressure starts to increase beyond the setpoint for the line. At that time, the PID algorithm of the VFD destages/stops the previously added/started pumps. That is why a single VFD needs to stage/destage the pumps in the pumping network.
3. How is staging and destaging of the multiple pumps using a single VFD different than multiple pumps with multiple VFDs?
In the single VFD staging/destaging control scheme, the pumps that are not on the VFD output run at a fixed speed as they are started across the line and turned on and off using the relay output from the VFD. The only pump that varies the speed is the one that is connected to the output of the VFD. That is, the VFD PID controller controls the speed of the single pump and every other pump in the single VFD pump system runs at full speed.
Whereas, in the multiple-pump staging and destaging configuration, all the pumps can run at a variable speed using the PID controller of the VFD. There is a master VFD with the PID controller and all the other VFDs follow the output of the master VFD PID.
4. What is the difference between staging and destaging with a VFD versus a programmable logic controller (PLC)?
Automatic adding or shutting down pumps based on the PID output to meet the process demand provides a degree of automation to pumping systems with multiple pumps. The VFD controls sense the interlocks and gauge the available pumps in the pumping network for operation. The VFD application level controls shut down the pumps based on the reduced process demand or alternate the pumps for running configuration based on the accumulated runtime.
The same level of automation can be achieved by using across-the-line starters and controlling the process and the pump alternation using a PLC. Achieving this degree of control and automation by just using the VFD cuts down the installation and commissioning time for the pumping system and improves the overall return on investment (ROI).
If the process has multiple pumps in the pump network, the system is going to need a way to automatically start and stop the pumps in the network. There are technical and commercial benefits in implementing the staging/destaging of the pumps at the level of the VFD controls. Since there are multiple devices, the annual maintenance contracts with PLCs would cost more compared to only the VFDs. Embedded controls in VFDs offer ease of engineering using a single platform and faster troubleshooting.
5. With the drives now enabled with the Internet of Things (IoT), how would that help enhance the user experience?
IoT and digitalization of the industrial control devices are offering another level of customer experience for those that do not want to have local human-machine-interface (HMI) servers and control stations. IoT-enabled products are an option for users that are looking to control and monitor their operation from anywhere in the world. VFDs with a built-in gateway for internet connection reduce the need for additional hardware to connect the devices. Therefore, in a multiple-pump system that is configured for a staging and destaging application, IoT-enabled VFDs will help users monitor the system’s health, change the setpoint as required, or even change the schedule for starting and stopping the system. It can even help users know when the drive becomes available after a technician is done servicing the pump(s).