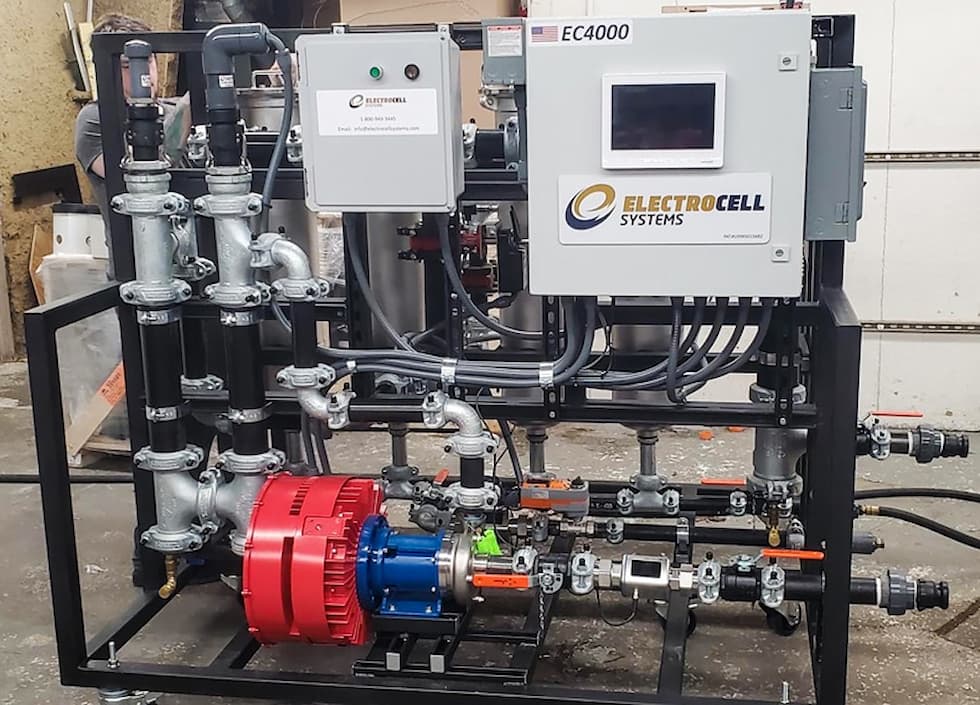
Rising urbanization, industrialization and industrial use are driving growth in the water pumps market. New developments in the industrial sector, particularly in power and energy, as well as agriculture, have significantly increased the demand for water pumps.
At the same time, emerging contaminants, Environmental Protection Agency (EPA) advisories and regulations are driving the need to produce cleaner, higher-quality water in more sustainable ways. The development of water recycling industries is also expected to generate substantial growth for participants in the water pump market in the coming years.
As growth in the pump market continues and more energy is required to power increasing numbers of water and wastewater systems, efficiency and reliability are becoming especially important criteria in pump operations. Through a combination of regulation and innovation, electric motors—which power pumps by transforming kinetic or rotational energy into hydrodynamic energy for fluid flow—are continuing to improve in efficiency and energy savings.
A new breed of smaller, lighter, quieter and efficient motors are being used in pumps for water/wastewater, as well as other agriculture, food and beverage and heating, ventilation and air conditioning (HVAC) applications. Benefits include reduced energy demand, less mechanical stress and fewer maintenance issues, among others. Below are five essentials to improve the efficiency and performance of motors for pump systems.
1. Variable Frequency Drives
A variable frequency drive (VFD) controls the speed of a motor by producing its own alternating current (AC), ultimately controlling the AC frequency supplied to the motor. VFDs also deliver energy savings. A recent study by the Cadeo Group verified the expected energy savings of variable speed systems and estimated energy savings to be between 19% and 55%, with variation due to workload.
When an AC motor is first energized to power a pump, it is susceptible to a large electrical current flow that exceeds the steady-state current value (i.e., in-rush current). Some motor designs address this issue with a soft starter, such as a reduced voltage soft starter (RVSS). Since a VFD can control the motor’s ramp-up time to full speed, it can also minimize in-rush currents without the risk of excessive motor slip and motor overheating, which are common concerns associated with soft starters.
2. Low Noise
Noise and other mechanical indicators can signal unusual conditions or system inefficiencies that require maintenance. Noise could be caused by any number of factors including abnormal load, incorrect mounting or brinelling.
Motors that incorporate printed circuit board (PCB) stators can eliminate two common issues in electric motors: acoustic noise and torque ripple. These motors offer low acoustic noise because of the absence of normal magnetic forces acting between the rotor and the stator. This results in an average of 3 decibels (dB) lower sound power noise across the entire frequency range.
Synchronous, axial flux, permanent magnet (PM) motors also remove core losses and eddy current loss in the rotor. The absence of magnetic forces between the rotor and the stator means no cogging torque, less vibration and therefore, lower noise (and fewer maintenance concerns).
3. Smaller Size & Footprint
Compact motors can pass on many benefits in pump operations. They often require less support structure, further reducing the cost of pump development and installation.
For small manufacturing or processing facilities, compact motor systems integrated with a pump can free up valuable facilities space by taking a typical packaged pump skid solution and reducing its footprint by 50%. A VFD mounted directly to a motor can also offer space savings and require less wiring compared to conventional motor plus VFD installations for pump systems. This can offer cost savings and pass a more manageable system over to integrators and pump OEMs that are looking for solutions for smaller facilities.
Many end users of fixed-speed pumps recognize the benefits of adding a VFD with variable speed capabilities to their pump systems. Variable speed pump systems allow users to control the speed of the pump instead of adjusting valves to match demand. This reduces the energy consumption and mechanical stress of the system. However, a common barrier for these operators is the costs associated with installing a traditional VFD. They report that the costs of running additional conduits and hiring certified engineers to install and commission the drive can outweigh the energy and mechanical benefits. Compact motor systems with integrated VFDs solve this problem by close-coupling the VFD to the motor/pump, which allows end users to reap the benefits without superfluous costs.
4. High Standards
Water and wastewater treatment facilities are critical infrastructure so failure is not an option.
Motors with PCB stator technology are reliable due to reduced torque ripple, vibration and fatigue. Using National Electrical Manufacturers Association (NEMA)-standard drive-end bearings and oversized bearings for the non-drive-end also offers added durability and reliability.
Motors that meet International Efficiency (IE)4 and IE5 standards offer some of the highest efficiency levels and can help pump OEMs achieve and maintain energy requirements while maximizing wire-to-water efficiency.
5. Controllability
Motor systems with embedded internet of things (IoT) technology can be programmed to provide valuable, real-time performance analytics that can improve your uptime and efficiency. For instance, in agriculture, farmers can efficiently control the pumps powering irrigation operations, intelligently distributing water throughout their farms, while reducing energy usage and combating rising operational costs.
MODBUS control capabilities can be used to relay information such as speed and power back to a system controller. This data can be used to determine a pump’s pressure and flow and allow the system to adjust performance as needed.
With this capability, mechanical features such as control valves, flow meters and pressure gauges can be eliminated from the system, saving installation costs and further improving operational efficiencies. VFDs can also transmit temperature and vibration readings, so facility managers and operators have more actionable insights for preventative maintenance.
Advanced motors are playing a larger role as pump OEMs strive for more sustainable operations. Five essentials, which include a VFD, small footprint, low noise, controllability and meeting the highest industry standards, can contribute to more efficient and higher performing pump operations.
Using motors that meet these criteria can result in reduced energy demand, less mechanical stress and fewer maintenance issues over the life of the pump system, which all add up to being better for pump operators and the planet.