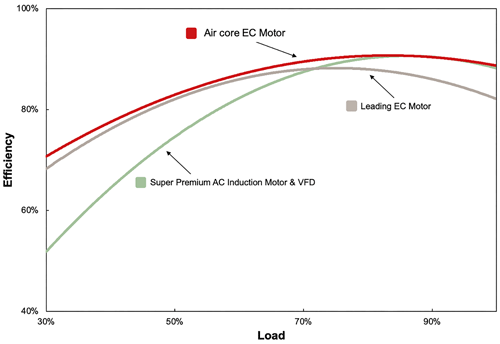
The United States Department of Energy (DOE) recently proposed new energy conservation standards for circulator pumps, prompting manufacturers to design them for increased efficiency.
Circulator pumps are ubiquitous, and the opportunity to reduce their energy consumption is enormous. An Electric Power Research Institute (EPRI) report estimated the energy savings potential for the approximately 30 million installations of circulator pumps is greater than 50%.
Circulator pumps are found in a variety of commercial building applications, such as air handling units (AHUs), cooling coil booster pumps, small radiant systems, ground source heat pumps and domestic hot water (DHW) recirculation loops. To date, circulator pumps have been overlooked for energy efficiency upgrades, in part due to the lengthy, capital-intensive design cycles inherent to pump design, but new technologies are making it worthwhile.
Currently, more than 90% of circulator pumps in the U.S. are constant volume pumps powered by standard induction motors, according to the U.S. General Services Administration. To achieve energy conservation goals, the DOE recommends using more advanced motor technologies.
The DOE’s analysis finds that electronically commutated (EC) motors are generally much more efficient than induction motors and can improve overall pump system efficiency. Most EC motors use a traditional iron-core stator with copper windings, but new air core motor topologies are using an innovative printed circuit board (PCB) stator, which has the benefit of eliminating core losses and increasing efficiency. As circulator pump manufacturers consider new EC motor technologies in their designs, there are several factors to consider for optimization.
Efficiency
EC motors are generally 30% more efficient than induction motors because their construction minimizes losses between the rotor and stator components. In EC motors, the lamination and copper heat loss is reduced by 50%, making it more efficient. EC motors that meet international efficiency (IE) 5 standards offer some of the highest efficiency levels possible, but it is important to note that EC motors can vary in efficiency over different speeds and loads. When choosing an EC motor, identify a motor that has a flat efficiency curve across a wide range of load conditions to optimize overall pump system efficiency and operations (Image 1). Doing this will ensure the pump system will benefit from optimum efficiency under a variety of operating conditions.
Advanced EC motors that use PCB stators can increase efficiency further and eliminate core losses. The copper
in PCB stators is etched directly into the PCB, increasing reliability and reducing the amount of copper material. Motors that feature a stator composed of a steel core with copper windings will experience eddy currents that result in motor losses. Replacing the core and copper windings with the PCB stator eliminates these losses, resulting in a higher efficiency motor at the rated power and speed, as well as across the entire operating range.
Controls
The DOE recommendation indicates that improvements to motor efficiency and demand-based variable speed controls can yield greater energy savings than those from improved hydraulic efficiency, saving upwards of 65% of energy use depending on the application. Pumps that vary speed can reduce their energy consumption by reducing pump speed to match load requirements. Integrated variable speed controls can also eliminate the need for throttling downstream valves to match demand, saving both energy and infrastructure wear and tear. In addition, this can be done without having to install, wire and commission a separate, conditioned air space for a conventional variable frequency drive (VFD), which can be cost prohibitive.
While all EC motors have some level of built in variable speed technology, it is important to be aware that their control capabilities range from basic speed control options to more sophisticated control features found in typical VFDs, such as MODBUS connectivity and capabilities to communicate motor performance and health data back to a controller or centralized control system. These advanced EC motors enable the remote monitoring of vibration, temperature, speed and efficiency, which feeds back to pump controllers and allows motors to adjust and protect themselves on demand.
Reliability
Compared to induction and other asynchronous motors, EC motors generate less heat, which avoids stress on components and results in longer service life. However, in all motors with copper-wound iron cores, the coefficients of thermal expansion of the iron, copper windings, insulation materials and varnish are all different, leading to expansion and contractions at various rates across the materials, which ultimately leads to the failure of the motor. The PCB stators in advanced axial flux EC motors only consist of two primary materials, the etched copper and the glass-epoxy laminate, both of which have the same coefficients of thermal expansion. This means thermal stresses are minimized and allow the copper to maintain its original form and protection within the PCB material. In a multiyear accelerated life test program where PCB stator coils were tested alongside conventional preformed copper coils under similar conditions to determine the robustness and reliability, results indicated that PCB stator life is at least 10 times longer and is 10 times more reliable than a form wound coil stator.
Design
The design of an EC motor is an important factor, as space is often at a premium. Most motor designs for pumps require infrastructure for foot mounts and allotted space around the pumps for servicing and the motor itself. EC motors that take advantage of more compact, axial-flux designs and thin PCB stators can result in 50% smaller and lighter form factors and reduce overall space required for a pump system (Image 2). These smaller, lighter EC motors can also simplify design processes for pump manufacturers and make installation easier.
Sustainability
Highly efficient EC motors can reduce energy use and operating costs over the lifetime of the motor and, in some cases, can pay for themselves within the first year of operation. In addition to reduced energy demand, sustainable design that minimizes the use of raw materials and incorporates end of life management can support initiatives to reduce waste. The majority of motors end up in landfills after 10 to 20 years, but advances in circular motor design are allowing for extended component life and reuse. Consider a motor that takes advantage of modular design to make the motor easy to maintain and allows components to be reused multiple times to serve future generations, keeping the motor in service and out of landfills.
As circulator pump manufacturers plan for the DOE’s new energy conservation standards and select EC motors for new equipment, efficiency, controls, reliability, design and sustainability should all be factored into decision making for optimal operations and lifetime. Selecting the right EC motor can help systems achieve the maximum energy efficiency and conservation of energy today, while contributing to a more sustainable future for the next generation.