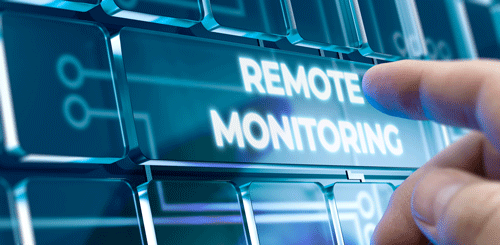
Water transfer companies that support fracking operations know keeping water flowing consistently and at the right pressure is key to serving their users and protecting their respective reputations. Remote pump monitoring, enabled by telematics, is a technological advancement that makes the job easier and more efficient.
Some pumps come with telematics technology installed. For pumps that do not, a remote monitoring system can be added in the form of a small box that contains a global positioning system (GPS) receiver, computer control board and satellite antenna.
Pumps telematics provide real-time data that allows companies to remotely track and analyze pump performance, adjust pumps and receive alerts when issues arise. The result is less downtime, less waste and increased efficiency.
Here is a deeper look at the benefits of remote monitoring for the upstream oil and gas industry.
Reduced Labor Requirements
Moving water through hoses across 20 or 30 miles of remote terrain presents a variety of challenges. Chief among them is the labor required to monitor every pump and hose, usually around the clock, to ensure the fracking operator has sufficient flow and pressure available to the frac site at all times.
In today’s tight job market, it is nearly impossible to hire enough people to cover every pump site, especially overnight. As a result, a company may not know until employees arrive in the morning that a split hose or pump issue has resulted in costly hours of water loss. With remote monitoring, third-party water transporters can monitor all their pumps from any location and set alerts that inform them when there is a problem.
Companies that have embraced remote monitoring report employees appreciate the technology. They are able to spend more time at home with their families instead of sitting in a truck in the middle of the night. Remote monitoring also frees up workers to take on other mission-critical tasks.
Faster Response to Emerging Issues
The telematics device collects data, stores it and sends it to an app or cloud-based fleet management solution that can be accessed on a user’s preferred device, typically a mobile phone. From any location, a pump user can check metrics such as suction pressure, discharge pressure, flow rate, engine speed, fuel level, oil pressure and oil and coolant temperature.
Users can set up alerts to be notified if a sudden drop in pressure or other irregularity occurs so there is no delay in addressing the issue. Pump telemetry even allows users to shut off pumps and remotely turn them back on. If a pump transducer is installed, the pump, as well as other pumps in the series, can be set to automatically shut off in predetermined situations. Automatic pump shut-off in the event of a pressure drop could save precious barrels of clean water if the drop is due to a hose leak. Once the pumps stop running, the company can send personnel to the first pump that shut off to identify the problem, fix it and get the water flowing again.
Even the most diligent employee on manual pump monitoring duty cannot notice a problem faster than telematics can, and any delay in shutting down a pump wastes water and drives up costs. Once the worker notices a problem, the time it takes to relay the information to a manager and alert other employees to shut off pumps down the line results in additional water loss.
Faster Response to Changing Needs
Remote monitoring is a valuable tool in nonemergency situations as well, allowing companies to respond more quickly to their users’ changing needs.
With pump telematics, if a fracking operator determines it requires more fluid pressure in a particular situation, a single worker sitting in a remote location can quickly increase the speed of every pump in the series so there is increased pressure almost immediately.
Optimized Pump Maintenance
Water transfer companies that leverage telematics can establish a reputation for efficiency and reliability, thanks in part to more efficient maintenance. Detailed diagnostic and analytics data lets users track the performance of various components of the pumping system. Companies can designate maintenance personnel to receive maintenance-specific alerts in response to diagnostic trouble codes, low fuel levels, engine hours and other data. With rental pumps, these alerts can also be sent to the pump vendor.
Prompt maintenance often keeps minor issues from becoming major ones. For example, a remote monitoring system may detect when a seal is no longer doing its job. Practicing preventive and predictive maintenance reduces downtime and helps companies avoid the need to explain service interruptions.
Increased Sustainability
Remote monitoring plays an important role in increasing the sustainability of oilfield operations. Long-term droughts
in Texas and other areas have made water conservation vital. Remote monitoring of water transfer systems helps
reduce water waste. If a leak occurs, the system can be shut down immediately.
Keeping produced water out of the groundwater is even more critical. Conscious of the need to conserve water, fracking companies have found ways to reuse produced water in their operations. The downside is this water is laden with fracking chemicals and poses a serious problem if it leaks onto the ground and into the groundwater. As with clean water transport systems, remote monitoring of hoses and pumps used to transport produced water enables companies to minimize spills and quickly identify and address their causes.
Questions to Ask Your Vendor
Companies interested in adopting remote pump monitoring should ask potential vendors about the capabilities of their system. For example:
- What data does the system provide?
- Is the data secured, and if so, how?
- What types of alerts can be set?
- What actions can the user take to control the pump remotely?
- How user-friendly is the interface?
- Do you offer 24/7 technical support?
The ability to customize based on the data needed for each site and user is crucial, as is ease of use and convenience. Is it simple to find and review pump data, check multiple pump sites and control pumps remotely? Is the app part of a larger fleet management platform that can be used to manage additional equipment?
With remote monitoring, third-party oil and gas service companies can track and analyze pump performance from anywhere in the world, quickly identify irregularities and make adjustments remotely. By reducing the need for on-site personnel, remote monitoring also increases safety. It is a cost-effective technology and is one more and more companies are embracing.