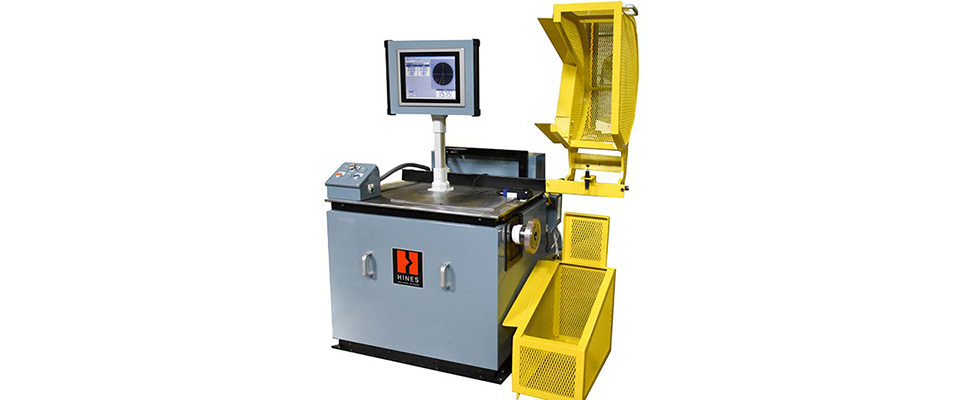
The top reasons for balancing a pump impeller are to make it run smoothly, quietly and longer. Unbalance causes vibration and heat buildup that will eventually result in bearing failure. Other dangers for unbalanced pumps include shaft deflection, excessive vibration, mechanical seal failures and seizing. The goal of balancing is to control the vibration to an acceptable limit when the pump assembly is operating.
Unbalance is the numerical amount and angle representation when the mass center axis of a part is different from its axis of rotation. The mass amount is multiplied by the distance from center to give the numerical value. Balancing is the act of redistributing the mass of a part so that the mass is evenly distributed around its axis of rotation.
Pumps commonly have two types of unbalance: single-plane and two-plane. Single-plane unbalance is when unbalance is measured on a single plane perpendicular to the axis of rotation. Two-plane is the unbalance as measured on two or more separate planes. Both planes will be perpendicular to the axis of rotationand, thus, parallel to each other.
Part dimensions will determine whether to balance in single- or two-plane. Generally, a 4 to 1 ratio of the diameter versus width of the correction planes determines how the part should be balanced. Narrow and flat parts are often single-plane balanced, whereas wider and longer parts are balanced in two-plane. Once the unbalance of the part has been determined, it can be corrected. Pump impellers are commonly balanced by removing material through grinding, drilling or milling—if the shape of the impeller permits.
The specifications for how well a pump should be balanced is known as the balance tolerance. Balance tolerance depends on part weight, speed of rotation and application. The force created by unbalance increases exponentially with speed. Unbalance tolerances are determined with operational speed in mind. International Organization for Standardization (ISO) provides guidelines for various “grades” in ISO document 1940-1. ISO 1940-1 was developed by a consortium of equipment manufacturers and operating companies aimed at optimizing economics and balance quality requirements. In this standard, the balance quality grade differs based on application of the part. The two key assumptions in this standard are:
- The permissible residual unbalance for geometrically similar workpieces varies inversely with the workpiece speed.
- Workpiece and bearing stresses will be the same for geometrically similar workpieces running at the same speed and same residual unbalance.
Therefore, the product of acceptable residual unbalance multiplied by the workpiece speed varies depending on the workpiece type.
One of the largest problem areas in balancing is the determination of adequate balance tolerance for parts. If the tolerances are too large, the final product will have too much vibration. If the tolerances are too small, a great deal of effort and money will be wasted trying to achieve it.
This can be frustrating to an operator of a balancing machine who may be unable to reach the specified levels using the balancer with which they have to use. Too much emphasis is often placed on using a “tight” unbalance tolerance and ignoring other design considerations.
ISO has issued guidelines regarding many devices. A pump impeller has a recommended “balance grade” of G-6.3. The ISO standards contain detailed methods of calculating different single-plane and two-plane unbalance tolerances.
How well parts can be balanced depends on several limiting factors. It is not cost-effective to balance a pump impeller to an extremely fine tolerance and then add components to an assembly that were not balanced to a similar degree of accuracy. Also, mounting pump assembly components without selecting appropriate fits and clearances will result in the components not being held concentric with the pump impeller. This creates unbalance in the system.
It is important to realize that balancing the pump impeller is only one step to achieving a balanced assembly. It is equally important to consider the balance of every rotating component, and also to consider how each of them is attached. A perfectly balanced component that is mounted off-center will create unbalance.
Another limiting factor during the balance process is limitations imposed by tooling. In an ideal world, all tooling
would be properly balanced, concentric and fit the part perfectly. However, no tooling is perfect.
Tooling can introduce several sources of error into the balancing machine’s measurement. The first source of tooling error is unbalance in the tooling. Any unbalance in the tooling and spindle will affect the measurement. To counteract this problem, tooling can be balanced by making corrections to the tooling itself.
A second source of error comes from tooling eccentricity or runout. Slight eccentricity can affect the balance by a large amount. Any eccentricity in the tooling and spindle will manifest as unbalance in the measurement. The unbalance caused by eccentricity can be calculated by the weight of the part multiplied by the distance off-center.
Here is an example of a tooling error that results in unbalance:
- There is a 10-pound part with 5 pounds of tooling
- The tooling is off-center by 0.003 inches (the width of a human hair)
- This will cause an unbalance of: (10 lb. +5 lb.) *16 oz./lb. * 0.003 in. = 0.72 oz./in.
Some balancing machine manufacturers offer tooling compensation that electronically accounts for and corrects both eccentricity and unbalance in the tooling. However, the third source of tooling error cannot be compensated for. Tooling must be accurate enough to hold the workpiece in precisely the same manner as the workpiece will be held in its final application and hold it consistently. If the tooling cannot accomplish this, it will contribute an inconsistent amount of unbalance, which will lead to parts having unbalance still present.
Potential causes of reduced tooling capability include debris on tooling or workpiece, repositioning of collet, wear of collet, oil buildup and poorly manufactured tooling.
Overall, in order to achieve balance tolerances, one must:
- understand balancing theory
- select the correct ISO grade for the application (G-6.3 for pump impellers)
- have and maintain high-quality balanced tooling
- minimize clearance between bore and shaft
- balance all rotating pump components
There are many obstacles to overcome when trying to meet an acceptable balance tolerance. By addressing the obstacles above, a pump user should have a final balanced pump assembly.