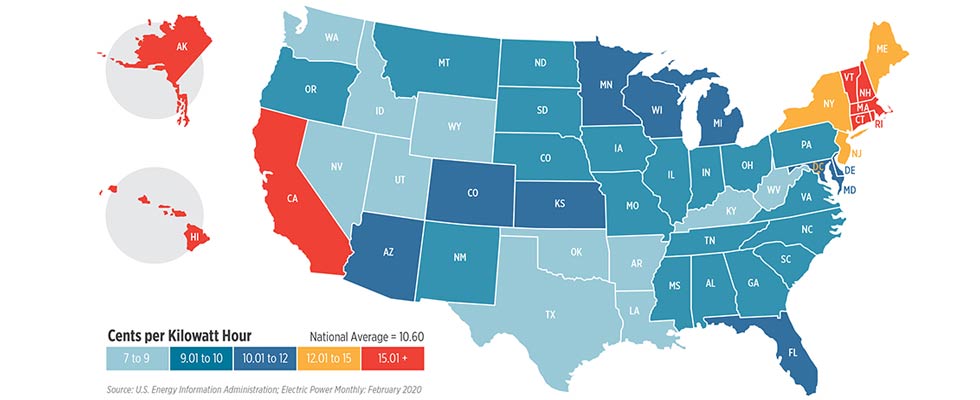
As more industries look for pumping solutions that operate with greater efficiency and conserve energy, municipal water systems are faced with their own set of challenges. While efficient solutions deliver positive financial benefits, system reliability is even more crucial. Steady operation, consistent performance and quality water delivery are all must-haves. There is no room for compromise when delivering water for entire communities.
Each component in a pumping system can factor into efficient operation. That is why, when considering a high-efficiency system, it is important to look at the total package: i.e., is the motor sized correctly for the pumping needs, and is the drive sized to handle everything? A variable frequency drive (VFD) that is sized for the pump and motor assembly and engineered to optimize its operation to specific minimum and maximum pumping demands—even the worst-case-scenario pumping demands municipalities can face—is an important consideration.
This is what high-efficiency pumping systems equipped with permanent magnet technology promise. They deliver reliability, performance, quality and efficiency. The key to getting the most out of these systems—and benefiting from all they have to offer—is understanding the impact of sizing and selecting the right high-efficiency pumping system for the application.
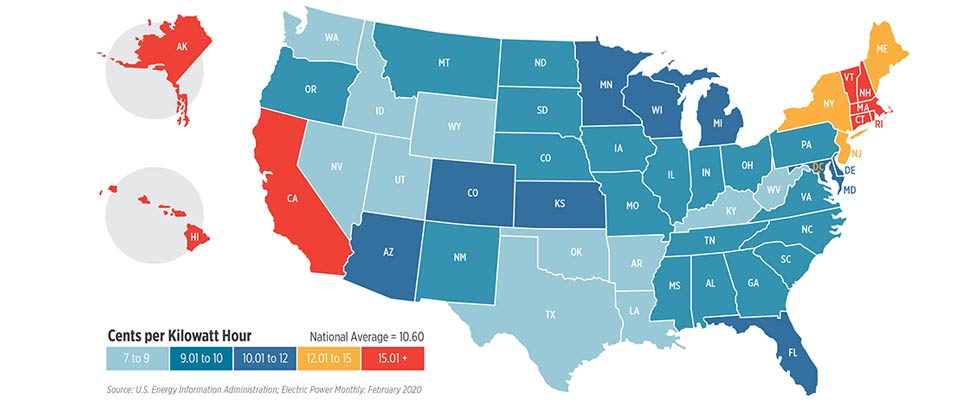
How This Technology Works
A growing solution for delivering higher efficiency is a complete system that features pump and drive components built around a permanent magnet motor. These motors feature rare earth magnets that operate with no-slip and run more efficiently. This translates into lower input power for the same output power that saves on operational costs every time the motor runs. Because they are engineered around a pump and drive package, efficiency is maximized.
A total system can offer a 90% or higher motor efficiency rating, which is up to 12% higher than a synchronous motor of similar ratings. In a municipal setting that runs constantly, these savings can add up and will multiply over the years. In fact, given the 24/7 operation that happens with municipal systems, this groundbreaking efficiency can pay for itself in one to two years,1 while the system’s life cycle continues to serve the community for more than a decade when operating at regular conditions.
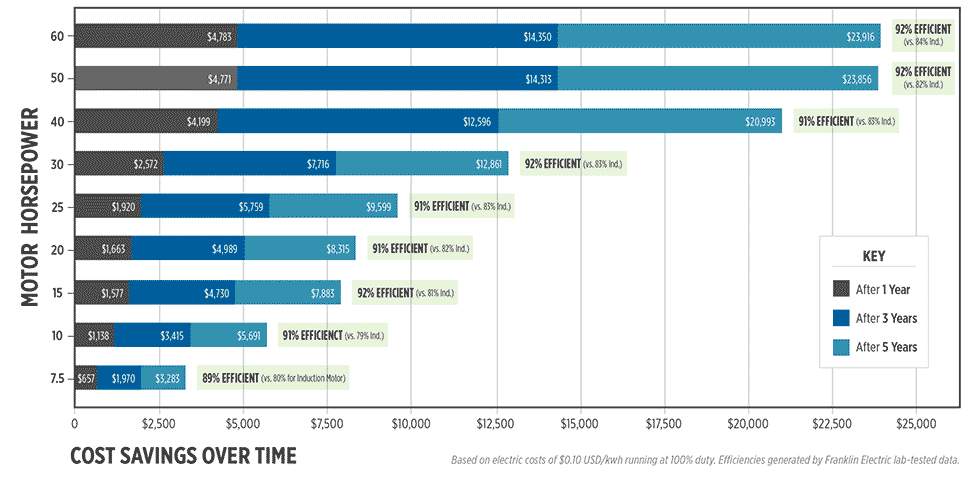
Balancing Operational Savings With Reliability
For many municipalities, permanent magnet motors may seem like a new concept, but they have proven their value for years in specialized applications from machine tools to, most recently, air conditioners, fans and pumping systems. Thanks to the evolution and the high relevance of this technology, permanent magnet motors can now be found in even more pumping applications and a variety of conditions, including municipal settings. As of 2021, more full-service manufacturers offer solutions suited for small ranges using 4-inch motors and reliable systems that cover up to 300 horsepower (hp). As technology progresses, manufacturers have also come a long way in providing cost-effective solutions that are built around drives engineered to operate with both induction and permanent magnet technology rather than custom ones. This also allows users to easily upgrade existing installations by switching out the motor only for streamlined retrofit applications.
This larger hp still delivers all the benefits of permanent magnet motor operation, like lower energy consumption and reliable operation. The lower consumption then has a ripple effect within a community: by consuming lower kilowatts than standard induction systems, there is less stress on a community’s electrical grid. Users can also operate them at a slower speed for general use, but if users need more flow or pressure, a properly sized system can accommodate it. For example, for pumps that do not load to the permanent motor’s service factor amps (SFA) rating, the permanent magnet motor can spin faster than an induction motor to increase the performance of a lower-performing pump.
Of course, when supplying water to homeowners and businesses, quality is critical. High-efficiency pumping systems that are National Sanitation Foundation/American National Standards Institute (NSF/ANSI) 61 certified and safe for drinking water systems provide this peace of mind.
When looking for greater long-term savings and a lower total cost of ownership (TCO) over conventional systems, there are several factors to consider in addition to daily operating costs. With permanent magnet technology, field trial data indicates an investment payback of fewer than two years in most long- or continuous-run applications. Many factors can improve this return-on-investment (ROI) time, including energy consumption costs in the region. In fact, data from the Global Energy Institute indicates stark differences from state to state in terms of energy costs, with nearly half of the country paying at or higher than the average cost of 10.60 cents per kilowatt hour.2 California, Vermont, New Hampshire, Massachusetts, Rhode Island, Alaska, Hawaii and Connecticut have the highest rates at 15.01 cents or higher.
Although less notorious, energy used by induction motors to produce work can reach up to 97% of its lifetime cost, while purchase price represents as low as 2%.3 Preliminary data also indicates a longer run life. In addition, permanent magnet motors feature a lighter and more compact size than standard induction systems, offering ease of installation while reducing freight and setup costs. This is especially important when it comes to emergency replacement situations, where a more compact unit can be delivered to the jobsite quicker and more cost effective.
What about other costs associated with startup, installation and operation? While annual energy costs are easily calculated using motor efficiency, ease of initial startup and overall operation can also deliver cost savings over time. Select manufacturers have engineered their packages so that drives can easily be paired with a variety of motors in minutes—eliminating time wasted on programming.
In terms of operation, specific high-efficiency systems have been designed with built-in compatibility with smart technology. These systems can be paired with accessories and protocols that unleash remote operation. This allows users to monitor systems and record data remotely, saving on time, labor and transportation costs.
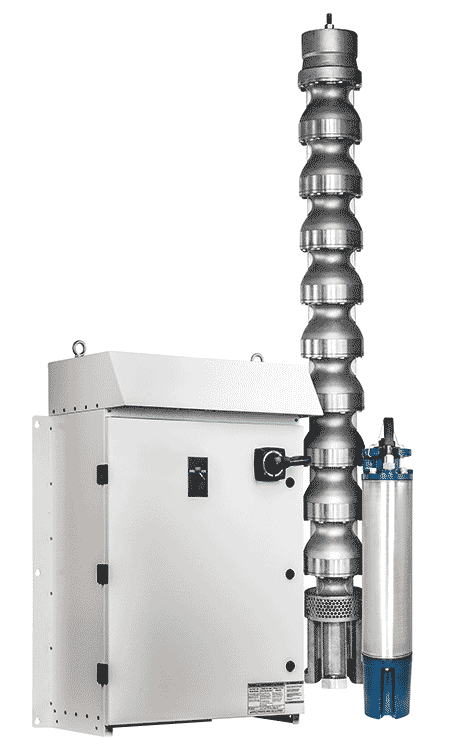
Built to Work Together: Compatibility & Scalability
High-efficiency pumping systems with permanent magnet motors are offered in a variety of sizes and can easily grow with a municipality. Getting the system from one manufacturer can help with this compatibility and scalability. A single system manufactured with these components and shipped from a single source will allow for simple startup, compatibility with a variety of application types, optimized performance and extended system life. Some offer service options to ensure users are backed up for sizing and selection as well as setup.
In terms of scalability, users do not have to compromise efficiency when the system needs to grow. In fact, the larger the system, the more users can continue to save, thanks to increased operational efficiency. In fact, after the initial payback period, users are actually making money compared to a conventional system while also satisfying customers’ needs—including growth in the community.
References
1. Franklin Electric Field Data
2. Global Energy Institute U.S. Chamber of Commerce
3. Hydraulic Institute