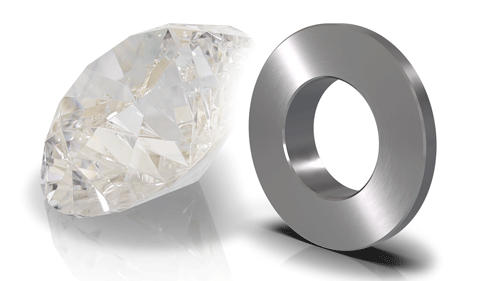
Proper mechanical seal face selection is essential for eliminating leaks in pumps and other rotating equipment. The benefits of choosing the right face go well beyond improving mean time between failure (MTBF) rates.
Mechanical seal faces come in a variety of composition materials and designs. The face material must stand up to abrasion and wear. The most-used, hard-faced material is silicon carbide, followed by tungsten carbide and aluminum oxide, to name a few. Additionally, the face design should complement the type of seal for the application, including conventional, pusher, non-pusher, unbalanced, balanced or cartridge configurations.
However, there are two time-tested seal face material and design technologies that can take the guesswork out of the selection process. These options extend seal MTBF from weeks to oftentimes years, and reduce water, energy and capital
costs while helping companies lower their carbon footprints.
Diamond Face Treatment
Among the most advanced and durable face materials is ultrananocrystalline diamond (UNCD), or diamond seal face technology. This face treatment—a thin film of diamond—is grown from diamond film via chemical vapor deposition on the sealing face. The most widely used substrate for a diamond face treatment is sintered silicon carbide. With recent developments, diamond film is also being used on tungsten carbide substrates.
Today, more than 60,000 components using diamond face treatments have been deployed worldwide in various challenging applications, including abrasive slurries, chemically reactive media, poor lubricating environments, intermittent dry-running applications and temperature-sensitive media.
Not to be confused with microcrystalline face treatments that can only be used with another diamond mating surface, UNCD face treatments can also be run against silicon carbide or tungsten carbide counter faces and reduce costs associated with auxiliary equipment.
UNCD has a number of properties that make it a beneficial sealing material for many applications. The low coefficient of friction allows the seal face to survive low lubricity and intermittent dry-running conditions, also reducing heat generation and energy consumption. As an exceptionally hard material, its abrasion resistance makes it ideal for abrasive particulate and slurry applications. The chemical resistance of UNCD protects the seal faces and allows them to perform even in strong alkalis and acids.
They also reduce the application’s carbon footprint by minimizing water waste and reducing energy loss. Depending on conditions, the reduction in the motor’s power consumption alone can result in a payback period of less than 12 months.
A recent example highlighting the benefits of a diamond face treatment took place at a United States plywood manufacturing facility. The hot water temperature (315 F to 325 F), coupled with the seal faces’ heat generation, caused the mechanical seal’s O-rings to fail in just weeks.
The plant wanted to increase seal reliability while keeping its Plan 11 seal flush plan. Within weeks of adding diamond-treated faces on the universal cartridge seals, the facility achieved a return on investment for the seal upgrade. Retaining the existing flush Plan 11 saved the plant nearly $6,000 in equipment, material and installation costs. By eliminating the need for a coolant, the plant also avoided an increase of more than $3,000 and up to 2.1 million gallons in annual water usage, not to mention improving MTBF to 14 months.
Upstream Pumping Design
Used for decades around the world in many industries, upstream pumping (USP) seal face technology lowers the amount of water used to cool and clean a seal. Compared to more traditional solutions, this can reduce water usage from 2 to 3 gallons per minute to 3 to 5 gallons per day. USP combines the benefits of dual-pressurized and unpressurized seals, providing the environmental protection of a double-seal arrangement with the inherent safety of a tandem-seal arrangement. Active lift pushes the low-pressure buffer fluid into the higher-pressure process fluid, taking advantage of pressurized and unpressurized sealing concepts.
It replaces conventional seals with a low-volume, high-pressure pump. The pump propels a minute quantity of buffer liquid along the path normally sealed by the mechanical seal faces and into the product side. Because the product side is at
a higher pressure than the buffer liquid, this seal is said to
pump upstream.
The spiral groove pattern of the USP face is a pressure-generating system and acts like an impeller. It directs barrier fluid toward the outside diameter, meeting the resistance of the sealing dam and increasing pressure. This causes the flexibly mounted face to actively lift, setting the sealing gap. In this noncontacting mode, liquid is pumped from a low-pressure region to a high-pressure region.
USP technology eliminates complex and expensive support systems, saving money and reducing water waste. For example, a leading oil and gas company wanted to reduce operation costs. The company looked closely at one of its onshore oil field operations, discovering high water and power consumption rates.
The oil field employed water injections to boost oil recovery from existing reservoirs, employing an extraction process that utilized clusters of water injectors to extract oil from reservoirs. The oil field focused on 10 water injection pumps operating with traditional, mechanical double seals.
A cost analysis showed the oil field operator could save close to $2 million in six years by replacing the pumps’ conventional seals with USP face technology. Further, return on investment would be achievable after the first two years, and the pumps would run with 90% less pressure (8 bar), a safety enhancement over the 120 bar pressure with the double seals.
Face composition material and design are critical to the performance of the mechanical seal. Mechanical seals incorporating UNCD treatments are providing cost-saving benefits to many applications, ranging from poor lubricating conditions found in hot water to strong chemical and abrasive applications found in mineral processing and mining.
A USP seal face design reduces seal leakage to the atmosphere when compared to a pressurized dual seal. It delivers a simple support system, ensuring face lubrication without the cost of a pressurized barrier system. It also eliminates seal face flush to dissipate seal heat, reduces water usage, addresses low water supply pressure challenges, and lowers power consumption and heat generation.