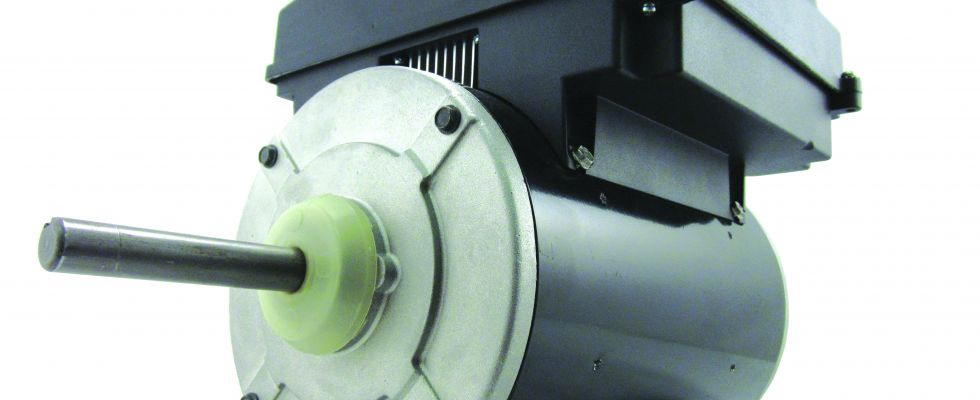
At a time when reducing energy usage is a priority for end users and government agencies, synchronous motors are gaining a foothold in the pumping marketplace due to their efficiency. Despite many benefits, not every synchronous motor technology is the right choice for every pumping application. This article reviews and compares various types of synchronous and induction motors and outlines the factors to consider when selecting a motor.
Synchronous motors are seeing worldwide growth. Analysts expect to see this category grow from 4% to more than 8% of all pumping motors in the next five years. That number may seem small, but it is only the beginning of a growing trend.
The popularity of this motor is related to the technological revolution over the last 10 years that has brought down the price of processor chips, and in turn, the cost of the motor/drive system. Thirty years ago, when synchronous motors were introduced in the pumping industry, processors to control the drive were costly and did not have many features. Now, the processors are a smaller part of the system and more powerful.
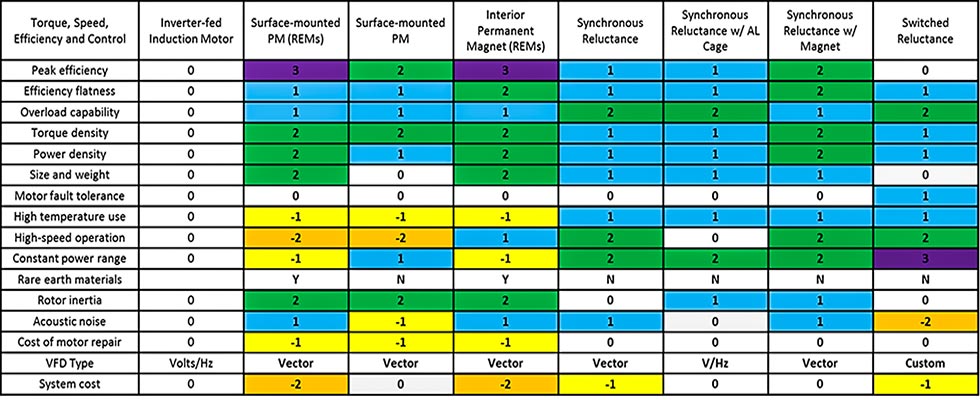
The use of rare earth magnets also adds to the cost, and magnet prices have swung wildly depending on the supply available (most are sourced from China). Fortunately, many manufacturers are now offering synchronous motors without magnets or with magnets not sourced from rare earth elements, making the motors more readily available.
What Is a Synchronous Motor?
In a synchronous motor, the rotor turns at the same speed (in sync) with the stator rotating magnetic field. Unlike an induction motor that relies on rotor slip to induce current into the rotor to generate torque, in synchronous motors there is no induced current and subsequent rotor losses. Reduced losses mean higher efficiency machines. Benefits include:
- high efficiency
- no rotor losses
- lower bearing temperature
- less frequent bearing maintenance
- variable frequency drive (VFD) performance (especially at lower speeds)
It is understood that there are energy consumption advantages by operating on a variable speed drive and adjusting operating speed to meet the application’s demands.
Synchronous-based designs experience their largest efficiency benefit when operating with a VFD. In an induction motor with a VFD, rotor losses account for a higher proportion of the total losses when operated at low load, as compared to operating at full load and speed. As the load is decreased, users see a comparatively better performance from synchronous motors as a result of eliminating these losses (Image 2).
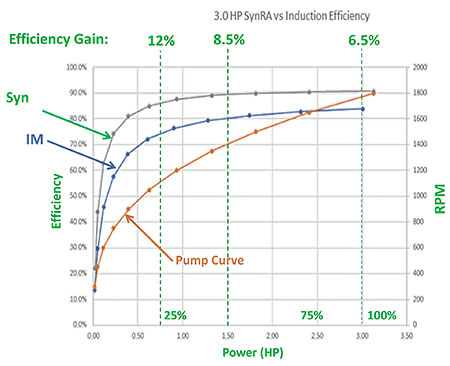
The flatter efficiency curve means the realized benefits will exceed the IE4 or IE5 peak efficiency improvement differential. Considering it is common to spend as much as 75% of the operating time below 90% of full speed, the impact is significant. As an example, in heating, ventilation, and air conditioning (HVAC), at full load, a synchronous motor integrated with a VFD will achieve a 3% to 6% increase in efficiency versus an induction motor at full speed with a VFD. However, at 25% power, users are still achieving 44% of the pump flow but at 8% to 12% higher efficiency. Thus, at part load operation, synchronous motors offer more efficiency improvements.
Synchronous Motor Varieties
Several types of synchronous motors are now available, and all seem to come with their own acronym. Here are the most common terms to know.
Electronically commutated motor (ECM)
When discussing pumping applications, ECM refers to a motor with integrated drives and controls. ECMs are commonly used in HVAC systems.
Brushless with permanent magnets (BPM)
These can be referred to as permanent magnet alternating current (PMAC) or brushless direct current (BLDC). Permanent magnets are surface mounted or interior mounted. The latter uses only rare earth metals, whereas the former could use ferrite-based or rare earth magnets. Lower mechanical strength and limited speed capability are downsides of a surface-mounted PM. An advantage is its ability to vary speed easily.
Hybrid synchronous reluctance motor (HSM) with PM assist
HSMs use lower-strength magnets that saturate the rotor and improve the power factor. The share of reluctance torque is significant compared to PMAC.
Synchronous reluctance motor (SynRM)
SynRM works on the concept of “magnetic reluctance” but does not require magnets to induce a magnetic field. The rotor consists of steel laminations cut to act as magnetic poles. The rugged design generally demands more current to the VFD and has a lower power factor compared to PM designs.
Synchronous reluctance motor with aluminum cage (SynRA)
SynRA offers the incremental advantage of running on a standard volts/hertz (Hz) VFD and can be a drop-in replacement to a current induction motor application.
Switched reluctance motor (SRM)
SRM predates both DC and AC induction motors. Control issues make it unsuitable for many applications. It has a simple design but a complicated electrical setup. Dedicated position sensors and timing mechanisms are required to control most applications.
Choosing a synchronous motor also means choosing a VFD, and different synchronous technologies have VFD choice implications. So, it is important to understand from the manufacturer the different expected outcomes.
When determining whether to go with induction or synchronous technology, take a top-level view. This “system-conscious” decision requires looking overall at the goals of the system. If the motor speed must run at 100% consistently, an induction motor is a good choice.
A potential drawback to synchronous motors as compared to induction motors is that in applications with unstable pumping loads, shuddering can occur, eventually causing the motor to trip. To prevent this issue, the synchronous motor and drive system should be designed to include a resistor to the VFD.
When it comes to thermal performance, the synchronous machine will have a comparatively far cooler rotor than an induction. This is due to improved power density and the ability to build a given rating in a smaller package, with less active electrical material, while also delivering higher efficiency performance.
The reduced rotor temperature also has a maintenance and reliability benefit. Since less heat is transferred to the bearings, and a temperature decrease of only 50 F (10 C) will double the grease life, users can expect the synchronous machine to be more reliable than an induction.
DOE Standards
The U.S. Department of Energy (DOE) is interested in synchronous motor technology and looking at setting test standards for them. The current pump energy index (PEI) shows no difference in efficiency for synchronous versus induction motors, but DOE, with input from the Hydraulic Institute (HI), has proposed to create coefficients to demonstrate the difference between synchronous and induction machines. This will allow end users to easily compare what pump suppliers are saying about their motor and drive efficiency.
With standard induction motors, it can be difficult and cost-prohibitive to exceed IE3 (NEMA premium) to reach the desirable IE4 or IE5 efficiency levels, particularly for smaller power ratings less than 75 kilowatts (kW). Synchronous motors, on the other hand, bring energy efficiency improvements to the industry, and the latest and most high-efficiency motors and variable speed drives are readily available in the marketplace.
Pumping Applications
Today, synchronous technology is making a splash in pool pumps, taking a significant share of the industry. Legislation is driving manufacturers to become more comprehensive in their energy-efficient offerings. In particular, meeting the California efficiency levels now requires the use of synchronous technology in pool and spa pumps, causing manufacturers to standardize synchronous technology across the board.
For circulator pumps (used in residential and commercial HVAC systems), synchronous motors are prevalent. The DOE is working on a ruling now that could require the use of synchronous motors to meet the required levels of efficiency and take advantage of the lower partial load losses.
Variable speed induction motors are common in commercial pumping applications, but the next evolution for increases in efficiency could be synchronous motor-driven systems.
Synchronous motors are growing in use in the pump industry, a trend that could accelerate as energy savings and a regulatory push puts pressure on end users. Multiple technologies of synchronous motors are available, each with advantages and disadvantages. It is critical to fully evaluate the various offerings and choose the technology that best fits the application.