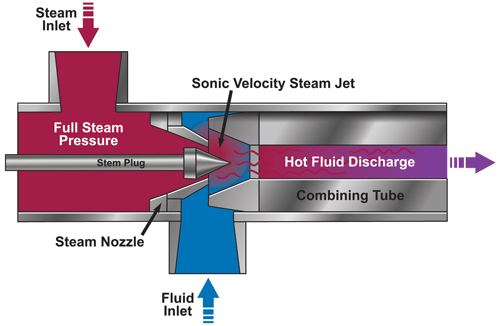
Achieving the perfect temperature every time is integral to chemical processing when using jacketed heating. These jackets are designed to control cooking temperature using a cooling or heating jacket around the vessel through which a cooling or heating fluid is circulated.
Two primary methods of heating a jacketed reactor are steam and hot water. Steam is often the first heating method for many in the industry because of its availability and ease of use, but more chemical engineers are beginning to see the advantages of hot water heating in jacketed reactors.
A water-heated jacket has a proven uniform heat exchange between the jacket and the vessel walls. This ensures uniform temperature control throughout the various stages, eliminating hot spots and burn-on and avoiding thermal shock for better quality control.
Steam in Jacketed Heating
Chemical processors have commonly leaned toward using steam as a heating source in jacketed reactor applications. First, the steam is directly injected into the jacket and heated to the desired chemical reaction temperature. Then, the vessel goes through a cool-down phase to bring the product back to safe handling temperatures (or its starting temperature) for the next step in the process.
This next phase begins by removing all the steam and condensate collected at the bottom of the jacket before introducing cooling water. If the cooling water is not added correctly to the jacket, the dramatic temperature change can cause thermal shock that can crack and damage glass-lined vessels or welds on steel tanks.
Steam heating is the least complicated heating technique, as the steam’s constant temperature is inexpensive and straightforward, but it is inefficient in some applications. Steam heating does not offer precise temperature control, due to the steam’s uneven distribution and the jacket’s higher temperatures. This causes hot spots to develop, compounding uneven product heating concerns. This increases the chance of product burn-on and reduces product quality.
Hot Water in Jacketed Heating
Using hot water to heat jacketed reactors solves many of the problems presented by using steam heat. The most important being that the temperature in the jacket can be controlled more precisely with hot water. Because hot water distributes heat more evenly, the ability to eliminate hot spots that can cause the product to burn is easier to do, improving product quality. Hot water can also be tempered to increase as the product temperature increases to eliminate large gradients that may occur when using steam in the jacket.
Some chemical reactions may go through a heating phase, a cooling phase and then back to heat several times. A hot water system can heat, hold and cool a process by introducing cooling or tempered water at a controlled rate. The water for the jacket can be gradually heated up or down to desired temperatures, eliminating the potential of thermal shock. This makes for a more streamlined process, as there is no need to stop production and wait like when using steam.
Indirect vs. Direct Steam Water Heaters
Heating water is the most common need in manufacturing today. Water needs to be heated (often to a precise temperature), whether the water is used for processing food, metals, pulp or paper or any other consumed commodity.
Chemical processors have several options when heating water—two of which are an indirect heating method (such as a heat exchanger) or a direct heating method.
Indirect heating methods heat water through a heat transfer barrier or wall, typically having a specific rate of heat conduction. Direct heating methods transfer heat directly into the water and provide instant heat transfer. Most chemical engineers are familiar with heat exchangers and use them for their processes, but many may not know much about direct contact steam injection heating.
Unlike indirect heating methods, direct steam injection (DSI) does not have a heat transfer barrier like a heat exchanger. While heat exchangers may be necessary for some applications, heat transfer barriers have a specific heat conduction rate that can lengthen the device’s response time to process changes.
On the other hand, DSI heaters do not have a barrier. They can respond instantly to a temperature controller, ensuring no lag time at startup as the fluid temperature will change immediately with the regulated steam flow changes. DSI heaters can be regulated as fast and precisely as the control loop can measure and respond to changes in temperature. This instant transfer of heat provides two main advantages: precise temperature control and energy efficiency.
More than 20% of the energy in steam can be presented as sensible heat. Because it is both the latent and sensible heat of the steam, a DSI heater requires less steam flow for a given process than indirect heating methods. In addition, condensate return is unnecessary for a DSI system because all the steam’s energy is transferred to the process. In essence, 100% of the condensate energy is recovered. Different DSI control valves use various physical principles for their operation. Each of these control schemes provides multiple levels of temperature control accuracy and other maintenance requirements.
DSI heating also offers other advantages that are not part of an indirect system. These savings can also lead to a more efficient overall plant layout, from reduced/eliminated maintenance needs to the compact size requiring less floor space. DSI technology also incorporates precise temperature control, which saves energy by heating fluids to exact temperatures while reducing setpoints and energy demand, resulting in improved product quality.
Instead of introducing only steam to the jacket, a DSI heating solution instantaneously heats water that then surrounds the jacketed vessel at a uniform temperature. DSI technology may ensure precise heating, eliminating hot spots and burn-on while allowing smooth transitions from heating to cooling with no thermal shock.