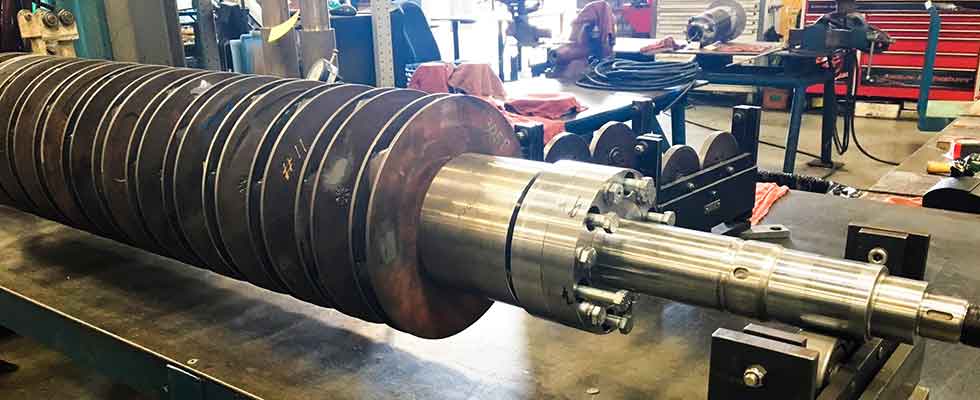
A major power plant in the United States experienced high vibration and recirculation issues with several ring section (BB4) boiler feed pumps, resulting in multiple catastrophic failures and unplanned outages. This case study details one of the pumps that was shipped to an aftermarket pump service center for a full analysis, troubleshooting, repair plan, rebuild and performance testing.
Combined-cycle power plants are the “new kids on the block” of the power generation industry. Designed to combine both gas and steam turbines, combined-cycle power plants can produce up to 50 percent more electricity with the same fuel usage as simple-cycle power plants. Modern combined-cycle plants can also react quickly to power grid demands with the ability to begin producing energy in less than 10 minutes and run at full capacity in less than 60 minutes. This provides an efficient complement to intermittent renewable technology.
As electricity demand has changed and combined-cycle plants have begun replacing conventional fossil and thermal power plants, the type of pumps used has also changed. Fossil power plants often use robust, long-lasting barrel pumps. These pumps operate for long, uninterrupted periods, and plants are generally fitted with two 100-percent or three 50-percent installed pumps per unit.
In combined-cycle plants, the demand for robust, yet expensive, barrel pumps diminished as the industry moved toward less expensive segmental rings pumps. Due to the recent shifts in the power industry, operators often face a shorter mean time between repair (MTBR), internal wear and high vibration issues on newly installed units.
Background
After experiencing numerous boiler feed pump performance and reliability issues at their power plant, the plant owner opted to pursue a comprehensive root cause analysis and repair plan with an aftermarket pump service center in Los Angeles, California. The investigation ultimately revealed a series of underlying issues linked to the performance problems and unexpected pump failures.
Findings, Engineered Solutions & Recommendations
During the first unit’s initial inspection and analysis, it was noted that the balance sleeve had a tapered fit in relation to the shaft. This type of design is uncommon because it requires high pressure and a special tool to install or remove the balance sleeve from the shaft. This is also a major safety concern.
Additionally, a tapered fit balance sleeve was installed near the yield point onto the shaft. The high pressure and tapered fit resulted in an undesired fit onto the shaft, producing high-stress concentration areas. The outside diameter did not run true to the shaft, which resulted in unequal peripheral pressure or force around the balance sleeve. In return, it created a scenario in which the shaft could bend. The reverse force, or bending moment, accrues 3,550 times per minute, causing significant bending moments at the root of the balance sleeve, eventually fatiguing the pump shaft.
A proposal was made to redesign the balance sleeve by making it a straight fit and making it longer to reduce the axial gap between the last stage impeller and the balance sleeve (Image 1). This prevents “disengagement” of the wear ring, which results in the destabilization of the rotor.

The phenomenon where the impellers hop forward and then return to their original position still exists, but due to the reduced gap, the impeller cannot restrict flow to the balance device.
The service center found that the pump’s original design required assembly by face-to-face configuration using anti-rotation pins. Because the last stage diffuser in the pump did not have a pin in the original design, the cover needed to “squeeze” the diffuser to prevent rotation. The gap produced by this design resulted in premature O-ring failure and also limited the pressure-carrying capacity. To improve both the pump reliability and the pressure-carrying capacity of the last stage joint, the diffuser’s faces were precision ground. By tightening the stack-up tolerances, the pressure-carrying capacity of the last stage joint is also improved.
Another major finding was that the slide fit impellers held each other on the shaft at the proper place with the help of the hub faces. However, the faces were not perpendicular, which forced the rotor to bend, causing high vibration problems.
When the rotor was placed on rollers to check runout, the TIR (total indicator runout) appeared to be within tolerance. However, the shaft would bend due to the faces not being precisely perpendicular to the bore once the pump was running and hydraulic forces were applied to the impellers. The issue was challenging to detect without imitating hydraulic force.
The service center designed and developed a special tensioning tool to verify the perpendicularity and parallelism of all impellers. Using this tool prevented the rotor from bending under dynamic conditions (Image 2).

The service center recalculated and machined the cover faces to produce an artificial cover sag that perfectly followed the natural rotor sag.
The recalculated offsets for the covers allowed the use of tighter clearances between the balance sleeve and balance bushing, therefore reducing the flow through the balance line. The balance line pressure on average was reduced by about 30 pounds per square inch gauge (psig), which also extended the MTBR.
Challenges
Initially, the power plant was hesitant to modify the pump’s original design and execute an engineered upgrade, which created a challenge for the service center to fully resolve the issue and potential shaft breakage. During the upgrade negotiations, another one of the plant’s boiler feed units failed unexpectedly with a broken shaft. As the service center anticipated, this additional failure served to confirm the issue at hand and emphasized the urgent need for a design modification.
Due to the urgency of the situation and the data provided, the power plant opted to send the additional pump for further analysis and proceeded with the proposed design upgrades.
Performance Testing for Validation
Power plants use balance line pressure as a main reference point in establishing a baseline for a BB4 pump’s overall health. The balance line pressure will increase along with greater internal clearances of critical fits, tolerances and other mitigating factors that can easily be missed during assembly. Therefore, performance testing that closely duplicates the actual conditions of a pump in service is a critical step in the repair process.
After repair, the pump was sent to a Hydraulic Institute-certified pump test lab in Chicago. Here, the pumps underwent standard testing protocols to measure vibration, pressure and flow. For reliability, the most important data point collected is the balance line pressure, a unique feature in testing segmental ring pumps. With the test lab’s engineering support, the service center was able to design and set up a testing procedure that closely mimicked the installed pump’s field conditions.

Back in Service
Once the repair and testing were completed and the pumps were installed, the service center received a number of identical segmental ring section pumps from multiple power plants exhibiting the same issues. Using the knowledge from the previous rebuilds, the service center was able to execute a series of similar repairs for these additional boiler feed pumps in an expedited time frame.
Today, all of the segmental ring section pumps have been placed back into service and are performing correctly without reliability issues.
The service center used a thorough inspection process, extensive process control procedures and stringent acceptance criteria to accomplish these repairs.