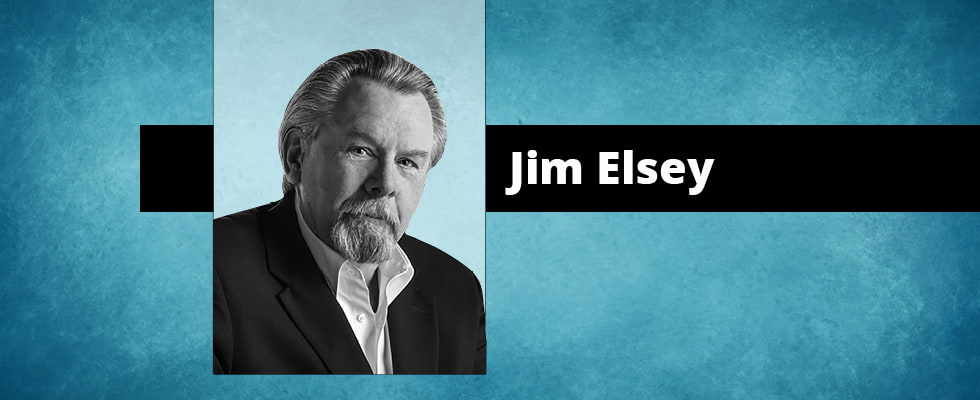
In last month’s column (June 2019), I shared my concept of what constituted a “pump twilight zone,” and I offered five mystery examples.
The preliminary reader reaction was good, so this month I am adding four more examples.
1. The case of the hidden factor
Problem
At a large paper mill in the Midwest, they use 8-inch self-primer trash pumps throughout the facility to transfer waste sump influent. Each sump has two installed pumps, one for main duty and the other is a backup spare. On a particularly troublesome sump, one of the pumps was having difficulty keeping up with the flow rate and was consequently replaced with a new pump from a different manufacturer. The new pump performed slightly better than the previous one, but not as well as the other pumps in the plant. It also could not keep up with the required flow rate.
The plant personnel contacted the manufacturer to have a representative visit the site for troubleshooting assistance. The manufacturer’s technician checked the pump’s mechanical settings and conducted all the normal performance tests, including a check for vacuum on the suction side with the suction isolation valve closed. All checkpoints on the pump were satisfactory and yet it would not perform properly in service.
The technician called his “pump-phone-a-friend” (aka, the old curmudgeon pump engineer for the manufacturer) and explained the situation. The suction lift was an easy 16 feet, the fluid is ambient temperature water and the submergence was more than adequate. The sump design is of adequate size and presented a laminar flow profile with little to no air entrainment at the pump suction. The engineer told the technician to look for an air leak in the suction line, but none were found. Some people suggested a new pump from a different manufacturer.
Solution The technician knew air leaks (ingress) in self-priming pump suction lines can be difficult to find because ambient air is leaking in—where most people are incorrectly looking for the fluid to be leaking out. He tried several methods involving leak detection equipment and the old and simple (but tried and true) method of duct tape and plastic wrap, all to no avail. The customer made a decision to live with the issue, add a temporary backup system and a plan to replace the “bad actor” pump during the next major outage. Months later, during the outage to replace the pump, they decided at the last minute to also replace the suction pipe. It was only then they found the hidden air leak in the suction pipe. It was in a transition piece that passed through the concrete floor above the sump, where it was inaccessible.
2. The magical exploding pump
Problem
At a surface mine near the previously mentioned paper mill, a rubber-lined slurry pump exploded during normal operation. When the pump exploded, the casing shrapnel damaged peripheral equipment, electrical enclosures and support structures. The good news was that no personnel were injured. The manufacturer was called and the engineer flew to the site to investigate. The customer insisted the issue was simply a bad casing (poor casting quality), and it was a straightforward warranty issue to replace the pump. The engineer did not believe in magic and went looking for the cause.
Solution
The engineer knew that pumps do not explode for supernatural reasons. He determined the forces required could only originate from a change of phase in the pumped fluid; that is, the liquid had changed to steam inside the pump. The volumetric expansion from water to steam is highly exponential and sudden, like an explosion. The suction and discharge valves for the pump remained open during the incident, so trapped fluid in the operating casing did not seem to be the cause.
Further investigation revealed the customer had added a variable speed drive to the pump to ostensibly control a sump level farther down the process line. The designer for the revised system did not factor the critical carrying velocity of the slurry into the calculations. A brief explanation is that solids will drop out of suspension if the velocity in the pipe drops below a certain level.
As the sump approached a full level, the newly added controls told the pump to slow down. It slowed down several times and so sufficiently that the solids in the slurry dropped out of suspension and formed a block on both the suction and discharge sides of the pump as if the suction and discharge valves were closed. Yet the pump was still running (but now with a blocked suction and discharge). The motor horsepower was simply being converted to heat in the liquid captured in the pump casing. We do not know exactly how long it took, but the liquid transformed to steam and the pump exploded; not as if by magic, but from the simple laws of physics in a PVT for liquids relationship (where PVT = pressure/volume/temperature). To understand and calculate liquid temperature rise in a pump casing, see my two articles on this subject in the November 2015 and January 2018 issues.
3. Electric bill increases 50 percent in three months
Problem
A petrochemical process facility in the upper mid-South uses more than 120 pumps in the plant. The pumps are all ANSI (B73.1) design compliant, and the population is evenly divided by two major manufacturers, but with two different types of impeller design. At the start of the new fiscal year, the facility switched sources for its replacement pumps and parts to a new supplier. Within three months, the plant manager noted that not only had the plant’s electric bill increased significantly, but the facility production output had also dropped markedly. The manager called the new supplier to complain and advise he was switching back to the previous source. The manufacturer’s engineer reluctantly agreed there was apparently a problem of some sort, but respectfully requested if he could ask a few questions.
Solution The pump engineer asked, “What has changed at the plant other than the pump supplier?” The plant manager then turned the conversation over to the new plant maintenance supervisor. After some conversation, it was determined that the new maintenance supervisor had been improperly instructed on how to set the impeller clearances. For one type of pump, the impeller setting clearance is to the casing and on another type, it is to the stuffing box (mechanical seal chamber). However, the new supervisor was setting all of the pumps in the middle of their total travel, which is 100 percent incorrect. As a result, all of the pumps in the plant were now operating at a low efficiency due to the enormous clearances. After some convincing and retraining, all of the pumps were restored to their correct running clearances. Now everyone is happy except the salespeople at the power company.
4. This pump is hot and haunted
Problem
A Pacific Northwest facility purchased an ANSI pump for a new system at their plant. The customer had dozens of ANSI pumps in service, but this was a first purchase from this supplier. After a few minutes of operation, the customer noted that the pump bearings were running hot and quickly rising in temperature. They shut down to investigate and called the new supplier. The local representative went to the site. The oil type, viscosity and level were checked as satisfactory. Pump end play and alignment were checked to be in an acceptable range. The pump’s hydraulic condition point for head and flow was measured to be near the best efficiency point. The results of a simple field test for excessive pipe strain were determined to be within acceptable limits. These checks were taking too much time and money, and the plant staff was getting understandably anxious and cranky. The representative called the pump factory for help. The factory engineer reviewed the data and asked for a picture of the pump installation.
Solution
When the engineer saw the picture of the pump installation, he immediately saw the reason for the overheated bearings.
The pump was installed with the right side (starboard) up against a wall that precluded personnel access. Since the oil level view port was on that obstructed side, the end user made the decision (with good intentions) to switch the view port to the left (port) side of the pump.
The mistake was the wrong penetration was used to install the view port. They used a same-sized 1-inch threaded penetration that was for the optional oil cooler (if required for high-temperature applications). By using the incorrect port, the oil level, when properly adjusted to be in the middle of the view port, was now approximately 1 inch below where it was supposed to be. Consequently, the bearings were starving for oil and this was why the pump operated hot.
The pump was removed from service, the oil level view port was positioned at the correct elevation and the overheated bearings and oil were replaced. The exorcism worked and the haunted pump is now running cool, sans ghosts.
Conclusion
Any time changes or additions are made to a pump and/or the system, we frequently enter a twilight zone of issues that initially appear as unexplained phenomena. Whether you are the end user, the supplier or an invested third party, always ask why the pump is being replaced and/or what has changed. If you find yourself frequently walking the path through the twilight zone late at night, ask yourself why. And then maybe ask the question a few more times.