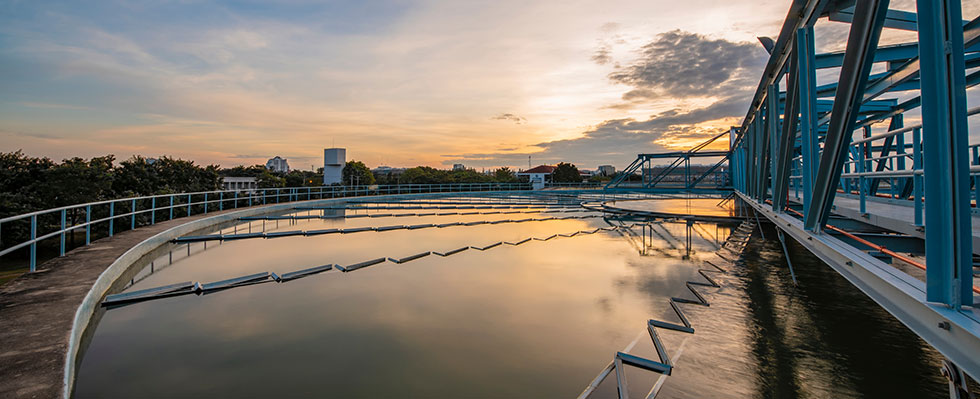
Industrial water and wastewater systems pump massive volumes of water throughout collection, distribution and treatment facilities to operate at maximum efficiency. As the amount of these processed fluids increases, so do the complexities of the system requirements.
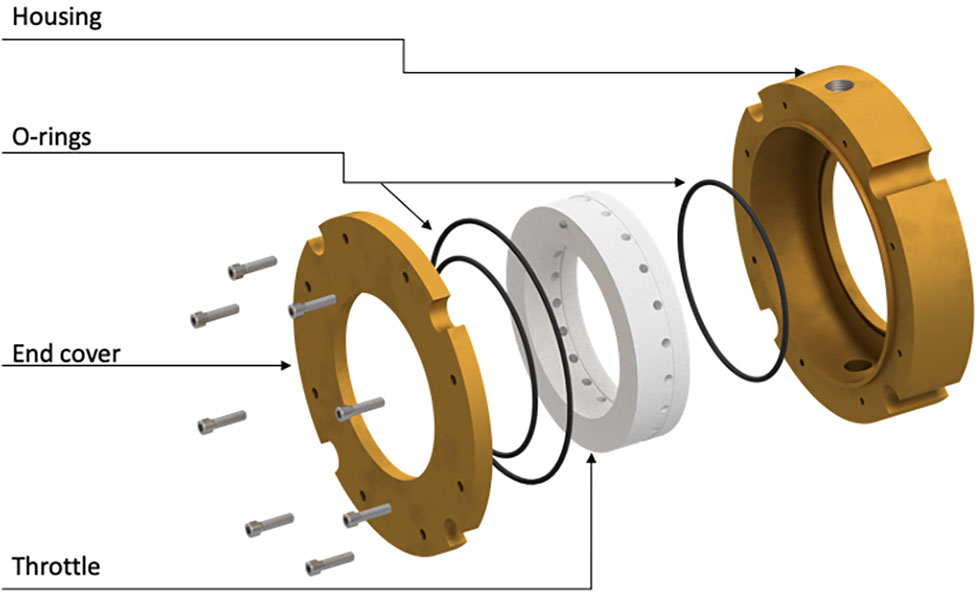
Additionally, municipalities and waste treatment plants often run rotating equipment, such as vertical turbine pumps, that can be challenging to seal.
It is paramount that pumping systems are designed to handle both the typical volume of processed water flow as well as the maximum runoff quantities that occur as a result of factors like excessive rain and improper sealing practices.
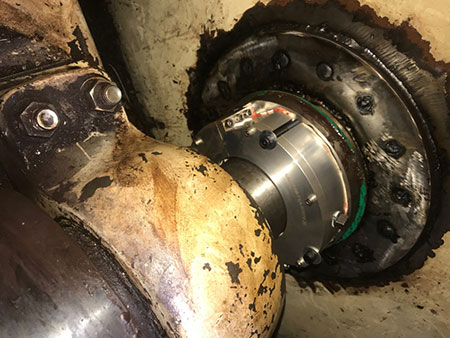
It is no secret that legacy main-shaft sealing devices designed 100-plus years ago remain the primary seal technology still used today. However, when end users are selecting the best sealing solution for their water and wastewater applications, they must grasp what advanced technologies are available that will best fit their facility’s specific needs.
It is important to partner with fluid sealing experts to establish a baseline and better understand how much water is being used at your facility. From there, teams can tackle larger problems that are affecting the pump system’s overall shaft sealing and reliability, including shaft size, sediment content in the processed water, leakage rates, startup conditions, water pressure, pump speed, vibration and cavitation. These affect the long-term success of both the sealing technology and the pump.
This article will discuss the importance of conducting water use studies in water and wastewater treatment to better understand how much water is being lost at a plant and how teams can partner together to create custom-engineered solutions like mechanical seals that eliminate leakage and increase overall system reliability.
How Well Do You Know Your Plant’s Water?
All industrial plants use water in some way to operate efficiently. Industrial water treatment systems vary, depending on each facility’s needs, so how can manufacturers, maintenance technicians and plant teams know exactly how much water their plant consumes? This is vital, as understanding industrial water treatment systems and water use can help any plant conserve water and save money.
Water Treatment Systems
Industrial water treatment systems can be straightforward and compact. They may also be complex, multi-unit processes. These systems are used to treat water for many different plant applications. They make water more appropriate for consumption, manufacturing or even disposal. The technologies selected—as well as the order in which they appear in each system—depend on which contaminants are being removed.
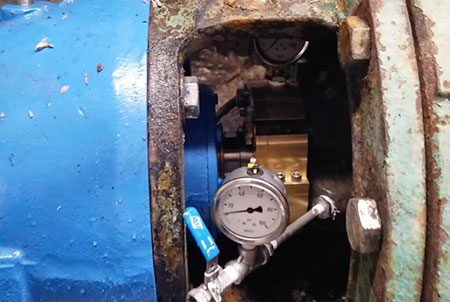
Some of the most in-demand industrial water treatment systems include:
Raw water treatment systems:
Used for the pretreatment and optimization of source water. This is naturally occurring water in the environment. The system improves production efficiency and process performance for specific applications.
Boiler feed water treatment systems: Treat water to protect boiler unit components and piping. They remove contaminants present in the boiler and/or makeup feedwater. These contaminants cause scale buildup as well as other problems that may be detrimental to equipment.
Cooling tower water treatment systems:
Used to protect cooling tower components from damage. This damage may be caused by contaminants in feedwater, circulation water and blowdown water.
Wastewater treatment systems:
Convert used streams into an effluent that can be reused or safely released to the environment or a municipal treatment facility.
Plants must decide whether an industrial water treatment system is needed. They must also determine which one to select. Consulting qualified water treatment specialists can help the team with these decisions. They can also help plants determine their goals and budgets.
Why Conduct a Water Use Study?
Treatment of water is costly and energy intensive. If the plant is not efficiently and effectively using this water, users may be sending money down the drain.
One area in which a plant may inadvertently waste water is in mechanical seal and/or packing flushing. To ensure that water use is as efficient as possible, users need to understand their plant’s current water use. A water usage study can save millions of gallons per year and help plants:
- decrease water use
- prolong equipment life
- eliminate process dilution
- reduce evaporation costs
- eliminate process costs
- reduce leakage to atmosphere
- reduce corrosion on equipment
- reduce housekeeping issues
What Does the Process Entail?
A fluid sealing expert uses ultrasonic testing to audit a plant’s media, flush water and leak rate. This audit helps determine an optimal flush water strategy.
For example, many plants maintain high flush water flow rates. However, they do not maintain flush pressure at 15 to 20 pounds per square inch (psi) above the stuffing box pressure. Plants should focus on maintained pressures—not flow rates—to maximize seal and packing performance.
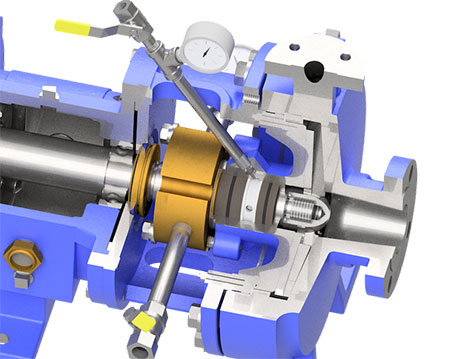
During the water usage study, the experts provide a summary of the facility’s current water consumption. At the same time, they develop a water reduction strategy for every stuffing box in the plant. The completion of water use studies typically takes between one and two weeks.
For example, a typical paper mill or chemical plant uses an average of 2 to 3 million gallons of water per year per stuffing box. Multiply that amount by every rotating piece of equipment, and you will find that big opportunities to reduce overall water consumption exist.
One water study was conducted at a food processing plant. Its sewer bill was nearly $1 million per month because of the high solids content. The decision was made to add closed-loop systems on many assets, and this managed to eliminate water use on those pumps and valves.
The information gleaned from a water use study can help with a crucial next-step decision: which sealing technology is best for this specific application?
Compression Packing for Industrial Applications
First designed at the turn of the 20th century, legacy sealing (compression packing) is the oldest and most common type of sealing device used to prevent product leakage and extend the life of pumps, valves and other rotating equipment. For decades, most packing was just lubricated vegetable fiber inserted in the stuffing box between the body of a pump or valve and its rotating member.
Now, exotic fiber materials such as polytetrafluoroethylene (PTFE) yarns, graphite yarns and carbon yarns are used to create packing that not only complies with more stringent water usage standards but can also withstand higher temperatures, faster shaft speeds and wider pH ranges. History has shown that achieving an average packing life of three years or more is possible in certain applications.
Compression packing is often the sealing solution that OEMs select to seal their equipment because it is a versatile, cost-effective option that does not require any dismantling of pumps or equipment to be installed. This is important for larger pumps that require special handling equipment to lift and move and are too vital to plant operations to allot for downtime. In critical applications, such as influent or effluent pumping where larger pumps are used to move wastewater streams, downtime can be detrimental, especially in the face of uncertain weather conditions and additional flows into the treatment plant when time is not an afforded luxury.
Clean, environmentally safe fluids can often be sealed with braided compression packing; however, while compression packing is a flexible and proven sealing device, it requires maintenance for break-in periods. Packing wears at the dynamic sealing area where it seals against the shaft or sleeve of the pump and, improperly applied, can affect the run life of the pump and lead to costly downtime for bearing, sleeve and component replacement.
Most importantly, a stuffing box with compression packing installed must usually leak a minimum amount, often making it not entirely suitable for environmentally hazardous fluids like wastewater.
Even in applications where the fluid is environmentally safe, this leakage may not be allowed in the plant due to housekeeping issues, safety concerns and costly product.
Because compression packing must usually leak, and single seals allow vapor to escape, hazardous or corrosive fluids like wastewater must be sealed with a double seal configuration and be lubricated with an exterior barrier fluid like water, synthetic lubricant or glycol.
More Robust Sealing Solutions Are Required
A mechanical seal is a device used to seal fluids on a rotating shaft. Unlike compression packing, in which dynamic sealing occurs radially between the packing and the pump shaft or sleeve, mechanical seals consist of two flat faces—one rotating and one that is stationary and mounted perpendicular to the shaft, eliminating much of the shaft wear caused by packing. Rotation of the rotary seal ring against the stationary seat ring causes a rapid pressure drop across the primary seal interface caused by friction on the liquid molecules between the seal faces. Liquid molecules also act as small ball bearings to lubricate and reduce friction, reducing heat and wear.
Mechanical seals are designed to be leak-free, which enhances overall sealing reliability and minimizes pump damage and safety concerns caused by leaks. Eliminating this leakage in a setting like a wastewater treatment facility or water processing plant will reduce the chances of bearing contamination and premature equipment failure, which will inevitably eliminate collateral damage and reduce overall operation costs.
When handling process fluids with heavy solids content like municipal wastewater, robust seals are required, and seal technology that eliminates or reduces shaft wear is critical. In these processes, compression packing may not be the first choice, as particulates may embed in the packing and be difficult to flush away. This will cause excess wear and friction, making packing less than ideal for slurry applications. One seal for this type of industry application is a single mechanical seal with an external flush system. The next solution is a double-arrangement mechanical seal. Another option is an air seal system where the system is made up of a noncontact tandem seal that uses air to seal and water to clean and cool the stuffing box—minimizing or eliminating particulate damage to the seal components. The system includes:
- two shaft-supporting bushings that minimize shaft deflection
- an air seal
- a lantern ring for flush water
Because the air seal is noncontact and floats above the shaft, the system uses little energy. It is also resistant to system conditions that damage or destroy traditional seals and pumps, including pipe strain, misalignment, off-best-efficiency-point (BEP) operation and cavitation.
It is crucial for pump system operators and facilities in industries like wastewater treatment to partner with sealing experts to identify which issues should be addressed. Through water use studies and equipment examinations, these experts can offer custom-engineered sealing solutions catered to a plant’s needs and training to setup teams for future success.
Not only will this reduce leakage of hazardous waste, improve safety conditions on-site and reduce downtime, but it can save a plant millions of gallons of water per year.