End users should consider factors such as initial cost, pump capabilities, performance, reliability and maintenance costs when making a purchasing decision.
IDEX Corporation
09/19/2016
.jpg)
Evaluating Applications
At the simpler end of the spectrum are applications for treating process water that will be reused for industrial purposes, such as boiler feeds, cooling water or water needed to dilute chemicals for other processes. For these activities, bleaching chemicals, cleaning agents and corrosion inhibitors are used to remove toxic elements. Few of these applications require high-pressure chemical injections, and most of the chemicals used are dispersed on a high-volume, continuous basis. For these reasons, fully functioning metering pumps may be considered extravagant, and lower-priced rotary gear pumps can do the job successfully. The highest end of the water treatment spectrum involves treating water for human consumption. Municipal water treatment plants deploy a combination of reciprocating and rotary pumps to accomplish the multitude of stages that are required to make drinking water safe for human consumption. They use metering pumps and rotary gear pumps to administer a wide variety of chemicals:- Disinfectants, such as chlorine or sodium hypochlorite, are used to improve odor and kill unwanted microorganisms.
- Coagulants are used to collide millions (or billions) of miniscule particles that are too small to be filtered (finer than 1 micrometer). These particles remain in motion because of negative electrostatic charges that cause them to repel one another. Positively charged flocculants, such as polymers, are injected in order to bring tiny colloidal particles together to form flocs, or larger and heavier aggregates, that become easier to filter.
- Chemicals such as sodium hydroxide and calcium carbonate control alkalinity. Diluted sulfuric or hydrochloric acids are used to neutralize other acids and correct pH levels. In some cases, a uniform and high-volume flow of these neutralizing agents is required. In other cases, the required amounts of chemicals to be dosed can vary depending on the pH of the untreated water.
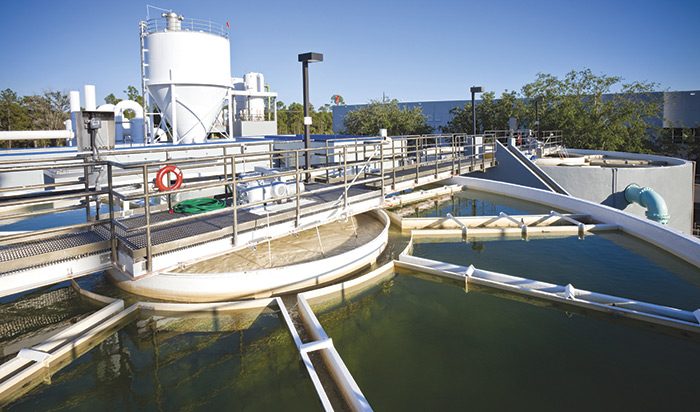
Pumps for Metering Use
Reciprocating pumps work by using a piston or a diaphragm to push the fluid out. The reciprocating action alters the volume of the pumping chamber, which changes the pressure exerted on the fluid being pumped. A pair of unidirectional check valves controls the pumping action, and the plunger cross-sectional area, stroke length and cycle rate determine displacement. Reciprocating pumps can deliver precise volumes for applications where high pressure is required. Sometimes, these pumps can be expensive because they require a complex drive for varying stroke. Reciprocating pumps may not be ideal for applications requiring excessively high volume flows, and they can be sensitive to changes in liquid viscosity, which can be an issue in dynamic processes where the viscosity changes with temperature variations. Reciprocating pumps can require complementary parts, such as a pulsation dampener to smoothen the pulsed flow of injected chemicals, an elevated reservoir, or a pressurized supply tank for liquids with low vapor pressures that do not flow freely. Despite these issues, reciprocating pumps are perceived to be higher-end products than rotary pumps. Their costs and capabilities may render them overbuilt for certain applications. Rotary pumps can overcome many of the challenges posed by reciprocating metering pumps, and they are usually less expensive. The cost factor is even more significant when pumped liquids require corrosion-resistant materials. Rotary (gear) pumps move fluid in a circular fashion between gears. The rotary gear pump operates by picking up fluid at the suction port in the cavities formed between the gear teeth and housing and by carrying the fluid around the outer diameter of the gears to the discharge port. By design, rotary pumps displace a relatively consistent volume per revolution, and they deliver essentially pulse-free linear flow. The flow rate delivered to the process can be varied in multiple ways, each with different degrees of control sophistication:- Bypass metering. This reduces flow to the levels required by the process and diverts excess flow back to the supply tank. Backpressure valves maintain constant pressure in the discharge line, while relief valves protect the components from excess pressure.
- Variable speed metering. This method can change feed rates by using a mechanical or hydraulic variable speed drive (VSD) equipped with a pneumatic or electrical operator, or a silicon-controlled rectifier (SCR) drive with a remote-control station.
- Ratio metering. This provides a combination of variable speed and bypass metering that can be used to merge two or more liquid streams at a constant ratio using an SCR package with speed control.
Selecting the Right Gear Pump
Companies choosing to implement gear pumps for their water treatment applications should consider the following criteria when selecting a rotary pump.- Design. Companies should consider pumps that feature a front pullout design, which facilitates easier access and makes it faster to maintain pumps. Design features should also include simplicity, with minimal parts.
- Performance. Today’s rotary pumps can deliver flow rates in excess of 10,000 gallons per hour, with multiple alternatives for turning down flow rates to meet process requirements.
- Safety. When choosing a rotary pump, sealless pumps offer fewer potential points of failure, which minimizes maintenance and ensures a higher level of safety for plant employees. Exposure to the chemicals used to treat wastewater can cause respiratory issues, and users should ensure that leaks do not occur when dosing hazardous chemicals like sulfuric or hydrochloric acid.
- Cost and value. Price matters on multiple levels, both in the initial cost of each pump and in the total cost of ownership. Users should evaluate total maintenance costs, parts inventory and time to delivery.