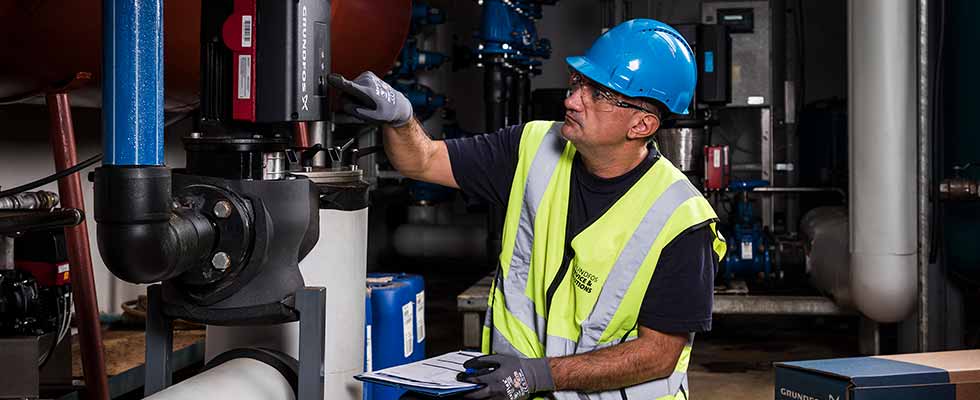
Every new pump system startup requires a balancing act between time, cost and accountability. Because pump systems are designed as “plug and pump” for easy installation, contractors and maintenance teams may assume that when the switch is turned on, the system will begin pumping perfectly. Many startups begin this way. However, regardless of whether the equipment is plug and go, pumps have undergone transport and are being introduced to a new system. Getting the best overall life cycle performance from the system takes minimal time and effort, including the right person at startup who best knows the product and how to make the minor adjustments needed to ensure that the equipment is operating optimally.
Even proven plug and pump systems experience common challenges that should be addressed at startup. Ensuring all the equipment is running optimally will deliver greater system efficiency and a longer life cycle, as well as reduce operating costs. If something is not configured precisely, continuing to run it can potentially worsen the problem over time and shorten the life span of the product or the system.
The person responsible for system installation may not be responsible for the long-term maintenance of the system. A factory-trained representative will know the best way to break in the product and system and bring it up to speed properly. This person understands how to measure vibration and perform alignment where needed, look for visible stress on the system, review sequencing and ensure elements are working together properly and efficiently.
One of the most common issues at a traditional pump and system startup is misalignment. There are many pump options today that may not require alignment due to their design. However, while traditional pumps may have been tested and adjusted during the manufacturing process for optimal operation, the physical challenges of transport from factory floor to installation site—the forklift mount, truck travel over long distances, and move to install site—often cause minor alignment issues. These are easily and quickly resolved when the right person who knows what to look for is on-site. It is best practice to ensure laser alignment is performed on long-coupled pumps to ensure optimal performance and full life span of these pumps.
Grouting the base of the pump or pumping system can be another common issue. Pumps and pumping systems are designed to move liquid, but the systems themselves should not move around. The main purpose of grouting a base is to reduce vibration and maintain structural integrity with the foundation. Grouting also helps shaft to shaft alignment, reducing the wear of moving parts of the pump and pump system. Some pumps and systems or newer versions take this into consideration within the design constraints and have eliminated the need for grouting. However, manufacturer’s recommendations should be strictly followed on this matter.
Startup puts stresses on a new pump and the overall system, so bringing the new system online at a reasonable speed and making adjustments as needed is the proper way to avoid damage at the onset. Some manufacturers offer recommended startup speeds, and industry norms recommend using soft start or initial ramp then slowly ramp up to operating speed using variable frequency drives (VFDs). Adding a new pump also has the potential to shock the system. The best practice is to close the discharge valve and perform a controlled ramp up of the pump to desired speed, then carefully open the discharge valve to gradually ease the system to desired operating condition. This is another example of how trained personnel can help smooth the startup process for pumps and systems.
Unnecessary strain to the system also may be caused during installation when something does not line up properly, and installers force pieces together. Operating the system this way, rather than making the proper adjustments during installation, can add unintended stress to the pump and system and result in costly repairs down the road. Trained personnel can point out these situations and help correct the issues in collaboration with the contractor.
It is best practice to take baseline vibration measurement at the time of startup to ensure it is within industry standard tolerances. Good measurements will indicate that equipment is operating in its “happy place” and no undue stresses on the overall system are observed.
Understandably, contractors for system installation and startup are constrained by a timeline and budget. Coordinating between multiple entities at the time of startup is a challenging task and can become a nightmare. However, contractors who include the right people during startup make the installation and startup process as efficient as it can be.
Contractors are highly skilled and knowledgeable about installation and other pieces of the systems. However, including a manufacturer’s startup representative equates to adding a specialist who will best understand how to properly initialize the pump and system.
Typically, manufacturers charge a fee to provide an on-site representative for startup and commissioning. However, factory-trained personnel know their products and how to look for the right things. In nearly every situation, something is found that requires an adjustment that will affect the long-term performance of the system.
Having an expert on-site allows contractors to complete the job more easily and quickly. The overall result for the facility engineer and maintenance team is efficiency, as well as a meaningful and cost-effective impact to the operation.
Plug and pump products are designed to provide easy and quick installation. They deliver time and cost savings to both the installer and end user. However, securing the greatest return on investment comes from including an expert in the process who understands long-term performance and system maintenance, ensuring the best results from the start.