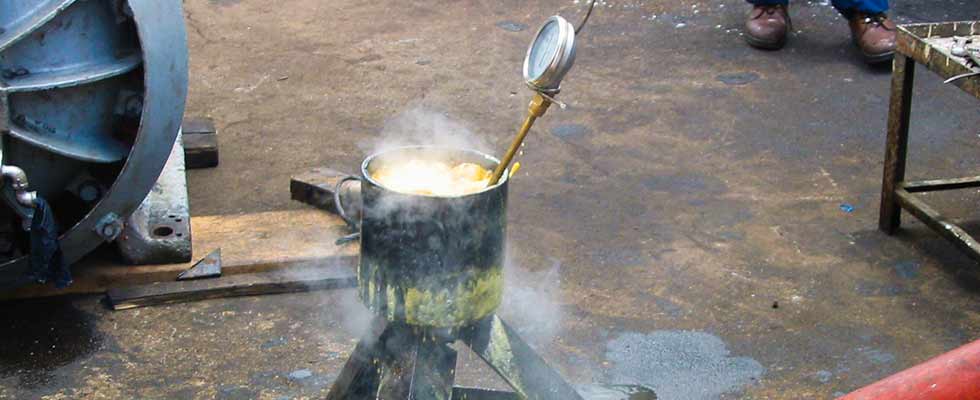
Improper bearing installation is a common cause of bearing failure. If a bearing is damaged during installation, no amount of lubrication or alignment will save that bearing. At best, it will only prolong its inevitable premature failure.
Poor bearing installation starts with poor bearing storage. It is important to ensure that bearings are kept in an area with constant temperature and humidity, making sure the oldest bearings are used first, keeping the bearings in their protective packaging, and laying them flat as opposed to hanging them. Make sure the environment is vibration-free and clean, in order to prevent particle ingress contamination. One big problem with poor bearing installation is the method that is used to install the bearings. This also holds true for gears, hubs, rings and any other workpiece that needs to be heated to be mounted on a shaft.
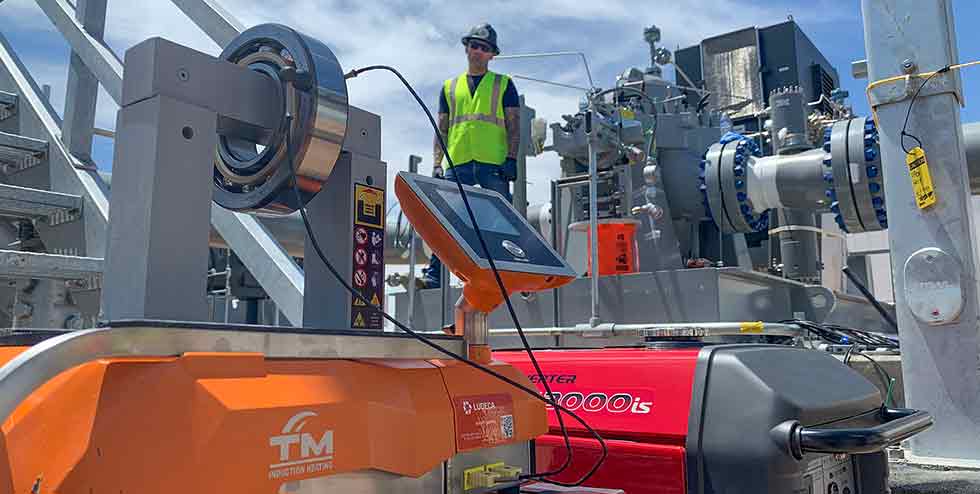
Other problems are selecting the correct bearing, measuring to confirm that the interference fit is correct, making sure to clean the shaft on which the bearing will be placed, and not contaminating the bearing during handling.
Another problem is overheating. It is imperative to maintain an even temperature throughout the bearing while installing it and make sure never to exceed 250 F (121 C.)
Once the correct bearing has been selected, it has been measured to confirm the selection, and the shaft is free of contaminants and burrs, now comes the selection of the method used to mount the bearing. The selection can either give the bearing a long, healthy life or condemn it to death before it rotates even once.
There are several methods that can be used to heat a bearing for installation: blow torch, brute force (sledge hammer), oil bath, hot plate, cone heater, and oven or induction heater. Here is a review of each method, along with pros and cons.
Blow Torch
Using a blow torch is fast, but remember that the temperature of the flame is between 2,000 F and 2,250 F depending on the type of torch. The bearing can heat up quickly, but there is no way of checking the temperature of the bearing and even a steady hand will get the bearing well beyond the maximum allowable temperature of 250 F that bearing manufacturers recommend before damage occurs. So, a blow torch is not a good option. Sealed and prelubricated bearings should never be heated using this method.
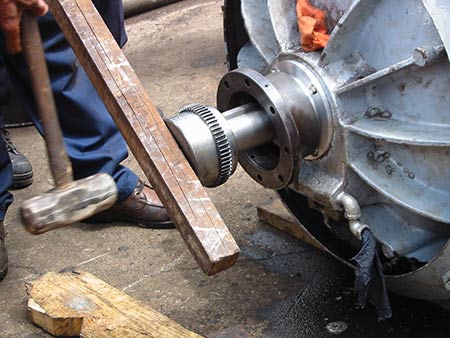
Brute Force
Using brute force usually means using a hammer (often a sledge hammer), preferably with a piece of wood to cushion the blow. No temperature issue here, but the bearing balls can be damaged with the impact of the hammer directly to the outside diameter (OD) if the bearing is not handled carefully.
If the piece of wood is not placed evenly across the bearing, the impact will transfer energy directly to the cage or balls, and can cause pitting on the surface of the OD and inside diameter (ID). It also may warp the ball bearings, damaging the bearing immediately. If users are not careful, sometimes the shaft itself can be impacted. This method is probably not conducive to a healthy bearing.
Oil Bath
Using an oil bath, the new bearing is submerged in hot oil. The temperature of the oil can be checked quickly, but the first problem is the contamination of the bearing if the oil is not clean.
Secondly, not knowing the exact temperature of the bearing itself, there is the risk of injury due to the hot oil and the possibility of a flash fire. Extreme care should be taken when removing the bearing from the hot oil and installing it. Prelubricated bearings and sealed bearings should not be heated using an oil bath.
Hot Plates & Cone-Type Heaters
These methods involve heat transfer. The bearing is placed on a heated plate, where the temperature has been preselected, but the majority of hot plates do not have a way to measure the temperature of the bearing. Secondly, the bearing is only being heated on one side, which means the bearing must be flipped to heat both sides evenly.
Oven
Users can set the temperature of the oven, but cannot verify the temperature of the bearing; an external probe may be required. Also, an oven can take some time to preheat.
Induction Heaters
This method is a clean and quick method in which the temperature is measured with a temperature probe. The desired temperature is selected to the specific degree, ensuring that a user will not overheat a bearing.
Most induction heaters also have an automatic demagnetizing cycle at the end of the heating cycle. The weight of the bearing is what will determine the size of the induction heater that will be needed. There is no one-size-fits-all solution, even though technically one could use the largest induction heater on the market and heat anything, but that would be overkill.
The ideal induction heater will use two temperature probes to monitor the temperature of both the ID and OD of the bearing. This is especially important for precision bearings. By monitoring the temperature between both the OD and ID, users can prevent the bearings from being heated too fast, and thereby compressed between the OD and ID, deforming the bearing balls and pitting the inner and outer races.
A high-quality induction heater with digital display and a graphing and export capability allows users to both see the progress during the heating cycle and export the results to be printed. A safety feature, which is a delayed start, allows an individual to step away from the unit before the heating cycle starts. This may be important for users with heart pacemakers or defibrillators installed.
The most important factor with all of these heating methods is to be able to precisely monitor the temperature of the bearing.