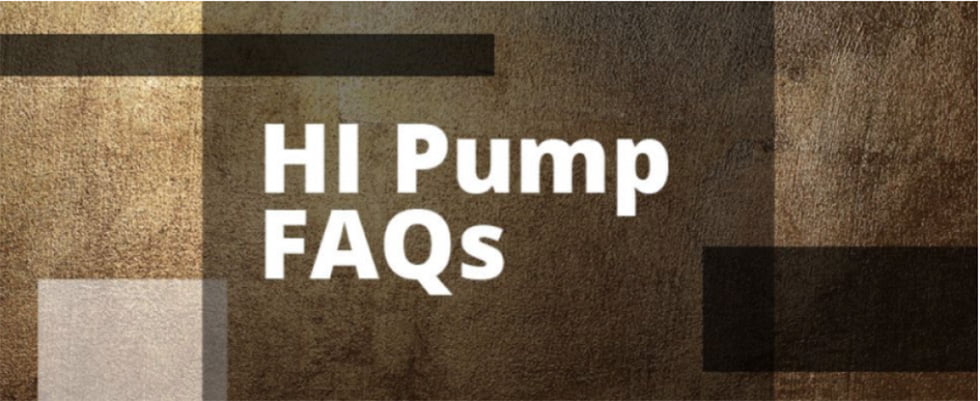
How is vibration due to structural resonance avoided in vertical pumps?
Vertically suspended pump types VS1, VS2, VS3, VS6 and VS7 are typically flexible structures above the mounting plate. Focusing on the above-base structure of a vertical pump and the frequency of the first bending mode, it may coincide with running speed(s) or other forced vibration frequencies. If the pump is operated in a resonant condition (running speed coincident with a structural natural frequency), then amplification of the forced vibration can occur resulting in unacceptable levels. If the pump has a variable speed drive (VSD), the probability of a forced vibration frequency coinciding with a structural natural frequency increases greatly. To prevent the structural natural frequencies of the upper pump structure from being resonant, manufacturers usually conduct a structural dynamic analysis, as described in ANSI/HI 9.6.8 “Rotodynamic Pumps: Guideline for Dynamics of Pumping Machinery.”
Because there are usually two windows in the discharge head/driver support, the lateral stiffness in one direction may be different than the lateral stiffness in the other direction. This difference results in structural natural frequencies for each mode in-line with the discharge pipe different than the structural natural frequencies for each mode perpendicular to the discharge pipe (Image 3). If we consider the forced vibration due to unbalance, a minimum frequency separation margin is desired between the first structural natural frequencies of the upper structure and the operating speed for a fixed motor speed unit, or the range of operating speeds for VSD units.
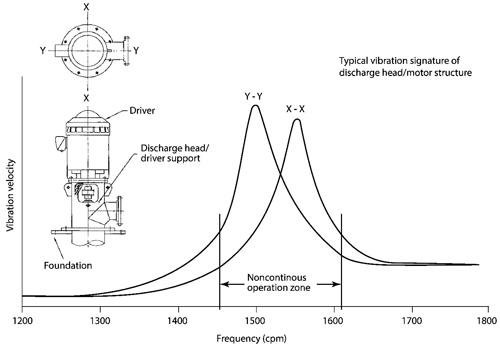
Within this example the operating speed would need to be below 1,450 cycles per minute (cpm) or above 1,610 cpm. If the pump needs to operate in the “noncontinuous operating zone” identified in Image 3, the designer would need to evaluate how to increase or decrease the natural frequencies in each direction.
Changing the pump structural natural frequencies may require one or more design modifications to the structural elements—including changing the window or shell geometry of the driver support or discharge head, adding ribs or gussets, changing the structural height, modifying the flexibility of the flanged joints, or selecting a driver with a different stiffness, weight or center of gravity location or mounting arrangement.
For more information, refer to ANSI/HI 9.6.8 “Rotodynamic Pumps: Guideline for Dynamics of Pumping Machinery.”