The concept of moving water from point A to point B has existed for thousands of years. It was not until after 1851 that engines began powering pumps, a hydraulic phenomenon known as suction lift in a "self-priming" pump. Ideas began to emerge about using water as power for other industries and as a tool to control the growing population's sanitation and food supply. The design of these pumps improved with time, and a large split volute, an open vane impeller, a check valve assembly and a strong drive assembly became requirements for the success of the self-priming pump revolution. New technology has inspired improvement to this simple mechanical concept—including submersible pumps with electric motors, vacuum-assisted centrifugal pumps and venturi systems with compressed air. The energy used by the pump to create a vacuum (up to 28 feet) restricts the self-priming pump's ability to create high discharge pressure, but the volumes can be as high as piping allows. Many companies have designed different versions of the self-priming pump, but in 1933, one manufacturer developed a pump with features that many users still rely on today. The combination of low maintenance, above-ground access, solids-handling capabilities, the ability to pull a suction lift up to 28 feet, and the large volute that, if full of water, allows the pump to prime and re-prime with use made this technology an ideal choice for wastewater facilities worldwide.
System Design
Selecting a pump for a particular application can be difficult. The selection strategy will depend on the application and the cost of the proposed solution: the cost of pump, motor and starter (if required), simplicity of the piping design and associated cost of maintaining the system. Once a facility determines the selection strategy, the next step is to improve reliability of the pump application by focusing on the piping design and basic implementation of instrumentation. This concept is illustrated by a facility that uses self-primed centrifugal pumps for cooling water circulation. The water source is an open pit near the pumps, and the sump is about 5 feet below the suction center line of the pump. A foot valve was installed at the bottom of the suction sump pipe. The pump manufacturer specifies the pump's net positive suction head required (NPSHR) given on the performance pump curve. The suction head should be taken into account in order to provide ample suction and prevent suction cavitation. In the case of pumping water, viscosity factor does not present a problem, and the temperature does not have significant variations that could affect the application case study. When designing the piping system, end users must follow the basic rule of keeping suction velocity below 15 feet per second by properly sizing the pipe, having an adequate water supply, and minimizing turbulence and water resistance caused by valves, foot valves and/or pipe fittings such as elbows. Calculating the suction friction loss is a more comprehensive method and leaves a smaller margin of error. With the addition of a basic instrumentation apparatus, the pump system will provide important process information that can lead to increased life and reduced downtime. During the startup of the pump system, check the piping and instrumentation drawing and compare with the field layout. Basic guidelines can help users visualize possible problems. Checkpoints that may help during a problematic startup are listed below.- The distance between the pump and the fluid source should be as close as possible.
- An adequate water supply must be evaluated prior to implementation.
- The pipe elbow should not be too close to the pump suction.
- If a filter or strainer is part of the piping, make sure it is not clogged.
- When a foot valve is used, make sure it is not stuck, and check for leaks. A suction pressure gauge can be used. Make sure the foot valve is functioning properly by closing the discharge valve, and then fill and charge the suction pipe.
- If an eccentric reducer has been installed, check for proper installation.
- Ensure the proper orientation of the check valve.
- Verify the suction lift is not too high.
- If not enough NPSH is available for the pumped fluid, consider a jockey pump or an inducer to increase the suction pressure.
- Check for possible air entering the system through valves above the water line or gaskets in the suction piping.
- If the fluid is vortexing at the pump inlet, low level at the sump may be the cause.
- If two pumps are connected in series, make sure that both pumps have enough capacity.
- Check that the vapor pressure of the fluid is not too close to the atmospheric pressure, especially when it rains. This condition may cause a drop in atmospheric pressure and can cause the inlet fluid to vaporize.
- Never throttle the flow of the pump at the suction of the process fluid.
Instrumentation Recommendations
In fluid dynamics, once the piping size and suction and discharge friction loss calculations have been taken into account and all the above check points have been analyzed, the next objective is overall information processing. In the case of pumping water for cooling processes, the basic instrumentation recommendations are listed below.- Low water level switch. In an open water reservoir, a low-level switch will provide information when the water level has reached a low indication, and corrective maintenance will eliminate pump cavitation.
- Flow monitor. A paddle type of flow switch can provide basic indication of either flow or no flow in the process. A flow meter will provide accurate water flow and a more accurate process condition. Several types of meters are available, including a magnetic flow meter, a vortex flow meter, an ultrasound and a paddle flow meter.
- Pressure monitor. A pressure gauge is the simplest way to check for proper inlet and outlet pressure. Pressure transmitters can provide instant information at remote locations.
- Inlet and outlet water temperature gauges or temperature transmitters. These can also be used to indicate important system conditions.
- Pump and motor indicators. Low-cost current meters can remotely send the signal to the control room to visualize current conditions. The current can be converted into motor horsepower that can indirectly be converted into a rough flow indication based on the pump performance curve.
Conclusion
A properly selected and engineered pump system can provide longer pump life, reduce downtime, offer indications of pump conditions and help users to plan upcoming maintenance. Basic fluid dynamics technology and instrumentation can significantly impact savings and reliability in pump applications.Other Self-Priming Pump Applications
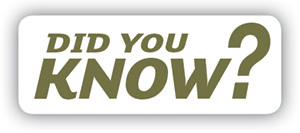
While self-priming trash pumps are widely used within wastewater systems worldwide, they are also becoming popular in portable rental units usually powered by diesel engines. A high demand for portable self-contained pumps has exploded during the past 15 to 18 years as general rental companies add pumps to their fleets. Coastal cities keep portable pumps on standby during hurricane/storm season to avoid flooding, as they do with backup generators for electricity.