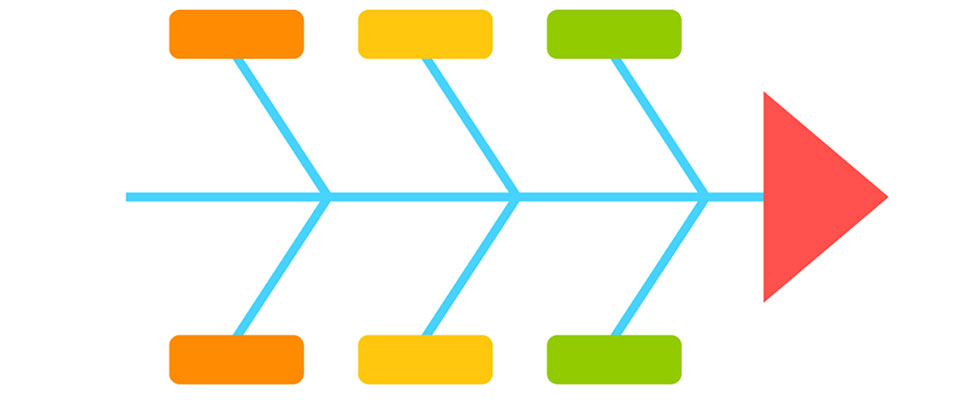
All too often, pumps fail. The same pumping system is attended to time and time again, and the maintenance costs mount up. This is a sure sign that the root cause has not been addressed. Instead, the symptoms are overcome, and the operation is set going again—until the next time.
Performing an analysis of the root cause of the failure will pay dividends. Once the root cause is found, long-term solutions can be planned, documented and implemented.
But which root cause analysis tools or methods should be used? A little knowledge goes a long way.
Operational Data
In root cause failure analysis (RCFA), experience has cultivated a preference to start with operational data. In many circumstances there is not much data, and what does exist may be unreliable. Where available, it is best to use data from systems such as telemetry systems, supervisory control and data acquisition (SCADA) and programmable logic control (PLC) data. Where this is unavailable, there are methods by which data can be derived or deduced.
For example, in the absence of a flow meter, forward flow can be derived from the pump running time and the volume of liquid passed forward. This can be compared to the pump curve, which can reveal if the pump is suitable for the application. Paired pumps, such as in an alternating duty/standby arrangement or identical but differently located pumps completing comparable operations, can be compared by calculating the ratio of pump flow rates. If both pumps are running efficiently, the ratio will be between 0.9 and 1.1.
Outside of this ratio and one pump—in the same setup—is running inefficiently relative to the other. In addition, investigate the relative frequency of starts for each pump. If one is starting more frequently, this can indicate a problem downstream of the pump such as an inoperative nonreturn valve (NRV). Far too often, a pump will be reset and the NRV is ignored, but having investigated the root cause, the NRV can be maintained, repaired or replaced.
Work Order Data
Another set of data that is informative if it is available is work order data. This may take the form of a count of the number of jobs raised to an asset, the type of job raised per asset, the amount of time required to repair the asset, or the reason the job was raised.
This is likely to be the impact of the service failure such as a leak or a loss of pressure, mean time between failures and spares required. Combining operational and work order data provides powerful data-driven and statistical root cause indicators. Consider, for example, using Pareto analysis.
Both data methods are assisted by accurate data recording which, in turn, requires a cultural understanding for the usefulness of recording accurate data as well as a comprehensive asset list.
The 5 Whys
Keep it simple. There are statistical methods for RCFA. However, an analysis method that is an everyday tool able to be used by everyone in maintenance is at its most useful and effective. A tool that is used is always more useful than a tool that is rare and can only be used by an expert. The five whys involves asking a series of questions to drill down to the root cause.
A user might stop at one why such as, “Why has the pump stopped?” They get symptomatic relief and repeat breakdowns—which is an expensive way to operate pumping systems. The first answer might be, “the pump was blocked” and ceasing the maintenance activity once the blockage has been cleared is a sure route to a return visit. So, it is necessary to ask further, “Why is the pump blocked?”
It could be that a macerator is broken, or it may be that inappropriate material is entering the system further upstream. Ask the third why, “Why is the macerator broken?” and so on until a root cause is arrived at and then address that. Always take a step back to consider what has happened and consider FRETT—force, reactive environment, time and temperature. Typically, this method requires asking why five times, hence the name of the method.
Fishbone Diagrams
This may require a meeting between managers or can be conducted by an individual, but it is more strategic than the five whys. It can even be used to provide the five why questions to be asked by a technician responsible for interventions. The bones of the fish may begin with generic areas of investigation such as:
faults in the design—pump selection, impeller selection, pumps used at an inefficient point of the pump curve
- material defects
- machining errors
- assembly or installation defects
- operational conditions outside of the design intention
- maintenance or lubrication deficiencies
- improper operation
Systematic examination and elimination of each hones in on where the root cause exists. RCFA does not have to be glamorous. Take a step back and consider what has happened, look into why it happened and drill down to the root cause—what system failed, which component failed, what combination led to a service failure from a component or a multicause effect.
Then, solve the root cause, document and implement a solution for today, and build in planned prevention for tomorrow.