
When it comes to pumps, one incorrect judgment could lead to an even bigger mess to clean up. Instead of heading for a surefire disaster, ask: what needs to be pumped? When it comes to electric submersible pumps, this should always be the first question to explore. It seems like common sense, but too often it is left unanswered while the wrong pump is rented or purchased.
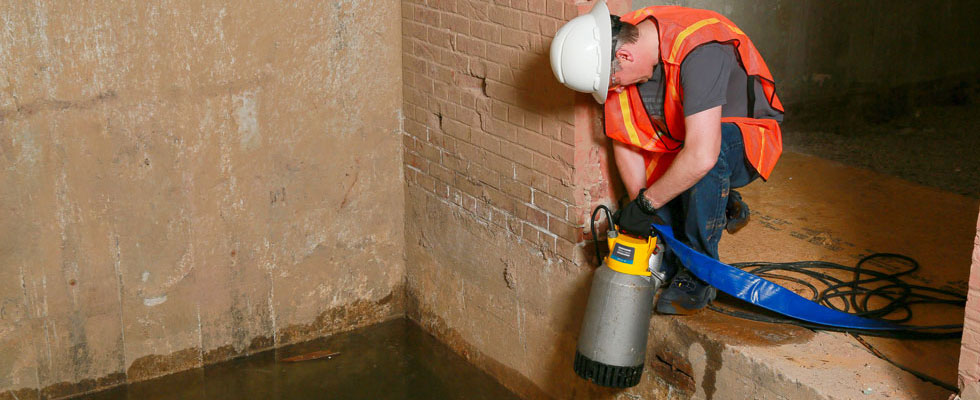
The type of application pump to be used on the job site is critical information. Just as important is taking the time to see what elevation, distance and flow are needed on the job. Without this knowledge, the likelihood of choosing the wrong unit to perform the work increases tremendously.
Taking the time to correctly answer these questions eliminates the biggest and most typical slip-ups during the pump selection process. To avoid costly mistakes, take a look at these recommendations for buying, maintaining and using submersible pumps.
Applications Matter
Electric submersible pumps are typically best used in deep groundwater. To provide the most impact on the job site, choosing the correct pump needs to be step one. There are three variations of these pumps:
- dewatering pumps: pump fresh water with minimal folic, such as sand
- slurry pumps: pump heavy mud
- sewer pumps: handle everything in a sewer
If the operator chooses the incorrect variation, the pump will promptly fail, leading to an expensive mistake. This is not ideal and can create many problems, including: clogging the pump, snapping the shaft, breaking the impeller and wearing the webbing down.
Once the user selects the correct pump style per the application, they should determine the amount of flow needed for the job, any elevation change and the desired distance for moving the water.
To combat gravity resistance, determining elevation change allows the user to know what pump strength is necessary to complete the task. It is important to know both the suction elevation from the water to the eye of the impeller, in addition to the discharge elevation from the eye of the impeller to the water’s destination. By adding these two numbers, the user will have the sum total elevation (gravity resistance).
The distance determines if the line size should be increased to reduce friction loss because of resistance. Friction occurs in all pipes and hoses when liquid travels through them. Velocity of the water traveling through the pipe or hose, as well as overall distance of the pipe or hose to the delivery point, both impact friction.
The flow requirement is determined by figuring out how far and the location where the water is moving.
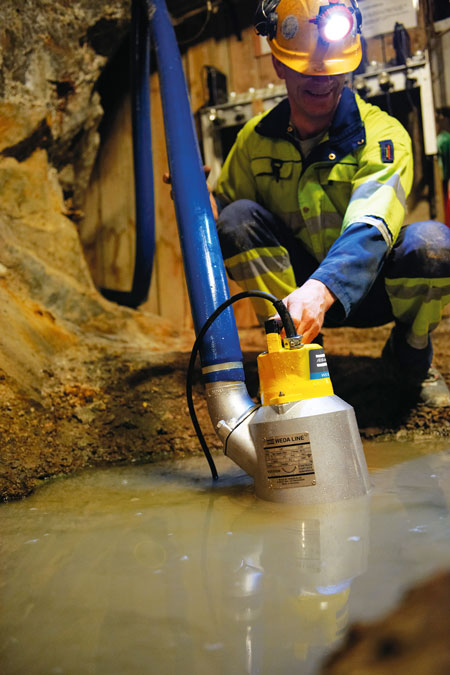
IMAGE 2: Operator performing maintenance on a dewatering pump
Variations of Features
Identifying these variables will impact the submersible pump’s features, such as horsepower (hp) and type of impeller.
Choosing the right size pump and power needed for completing the job is crucial. Wrongly sizing the pump for the application is frequently one of the biggest mistakes on the job site. This includes having too much hp and not enough flow. Selecting the incorrect size can lead to seal, impeller and shaft failures.
When it comes to impellers, the user should take some time to understand the impeller’s metallurgical makeup. Whether it is stainless steel, hard chrome or cast iron, the impeller type can make or break how the pump handles the application. For instance, if the operator is pumping something with solids in it, they would want a solid-handling impeller style and a submersible that can pass the solid. One additional item that can be beneficial in the metallurgic makeup depending on the material being pumped is the outer material of the pump casing. Choices include aluminum or stainless steel.
The pump casing can help with pH levels, or the measure of acidity or alkalinity of water-soluble substances. The scale is based from one to 10.
The casing and metallurgical makeup are important for chemical compatibility. If the water has a low pH, which can be acidic and corrosive, the operator will want a metallurgical material based on what is being pumped.
In this case, stainless steel is a good choice for lower pH levels. Additionally, aluminum handles a pH level between five to seven, but pumping low pH will likely chew up the casing to its death.
Over the Long Haul
Whether the operator just purchased or rented, or needs a refresher, it is always wise to refer to the OEM’s guidelines. This will help the operator create a proactive schedule of daily tasks and specific-hour intervals. For daily checks, the most important thing is to ensure the submersible pump is unclogged. When doing so, check to see if there is anything against the screen and clean as needed. Additionally, inspect the cable cord for cuts.
A benefit to submersibles is they are not equipped for engine oil, which reduces maintenance on this style of pump compared to most other pumps. However, it is recommended to periodically check if the seal has an appropriate amount of oil.
Lastly, by simply running the submersible, an operator can observe the unit and make note of leaks, abnormal sounds or smells.
Danger Ahead
Danger never ceases around electricity. So, when sticking an electrical submersible in the water, it is imperative to provide safety for the pump and the people around it. This should take top priority for the operator.
The first safety precaution to take is always properly shutting down the pump before performing any maintenance and system checks. Another safety measure includes confirming the pump does not rotate in the wrong direction.
One of the biggest dangers operators face with electrical pumps is an exposed cable. When a stray current in a motor uses a bearing as its path to ground, the resulting damage is known as electric arcing. This develops if there is a difference in potential between the shaft and the bearing housing.
For instance, if an operator runs a three-phase submersible pump, they would have an L1, L2, L3 and ground. An arc could occur anywhere between L1 and L3, creating an electrical surge or a fry situation toward the electrical motor.
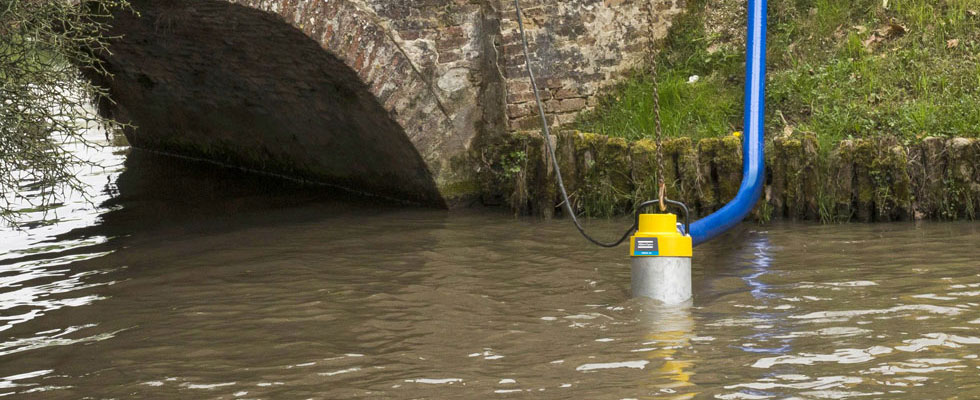
Conclusion
Success starts with some upfront work to successfully match the pump to the job. An understanding of this information will ensure the highest production from start to finish. When it comes to submersible pumps, taking a shortcut will only lead to an undesirable situation.
Finding answers to the application, elevation change and distance will make everything flow smoothly without setbacks and better safety.