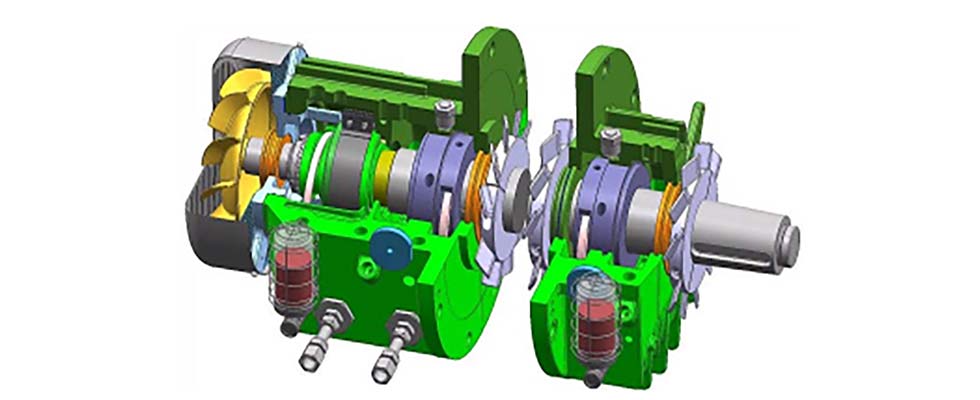
Reliability is a fundamental requirement for between-bearing, high-energy pumps that operate in oil and gas applications. To optimize pumping systems, design improvements and material upgrades can be implemented during planned maintenance intervals, extending meantime between failures (MTBF) with minimal effort. In older pumps, the bearing assembly is key to modernize the pump to current American Petroleum Institute (API) standards and reduce operating cost.
Pump failures and the resulting unplanned downtime can lead to elevated maintenance costs and lost revenue from reduced production. In many cases, the root cause of this issue is hiding in the design of the bearing housing. To resolve this, bearing assembly retrofits have become increasingly common in the hydrocarbon processing industry. These retrofits remove known failure modes of outdated designs and can meet current API standards to drastically improve MTBF.
API 610 11th Edition Retrofit
The first thing that comes to mind with bearing assembly retrofits are overhung pumps (API OH2), which are commonplace due to the relatively low cost and ease of implementation. However, these same principles can also be applied to between-bearing style pumps and achieve many of the same benefits.
Typically, pumps manufactured before API 7th edition (~1989) have outdated bearing styles, poor cooling ability, insufficient lubrication methods and cast-iron construction, making them great retrofit candidates. With these upgrades, operators can take advantage of the fact that the pump case, nozzle locations and feet positions will stay the same while modernizing the pump to the most reliable and latest API design.
This proactive approach to maintenance removes known failure modes to greatly reduce the risk of failure and unplanned downtime events. As part of the retrofit process, the bearing housings and all associated components are replaced with API 610 11th edition bearing assemblies.
When working with an OEM, these engineered pump housings and internal components are often the same as those supplied on new equipment.
Upgrading Designs
New equipment standards have been lab and field tested with better technology, ensuring current components deliver maximum service life. Additionally, there is interchangeability and commonality with current design pumps, allowing for fewer parts to be stocked, reducing overall inventory. Reduced inventory expense and extended service life make these retrofits a cost-effective option for older pumps.
Precision engineering should be applied when replacing the bearing assemblies as the retrofit process needs to account for thrust profile, loading, oil delivery and rotor dynamic stability. During the upgrade, new bearing housings castings and a new shaft make up the long lead-time items. When working with pump experts, the upgrade can often be engineered before the pumps arrive for repair, reducing the total downtime of the pump.
Improved Cooling
One big advantage to the modern bearing assemblies is the advanced cooling ability of the new housings. Incorporated in the design are advanced air-cooling features, like the fully finned geometry of the housings, larger outboard fans to increase airflow across the housing and inboard fans to exchange heat with the surrounding atmosphere. These features result in reduced temperatures and extended bearing life.
Along with the advanced air cooling, the new assemblies typically use a larger oil sump to remove heat from the bearings more effectively. With better oil delivery and modern nonmetallic oil rings, the oil can efficiently lubricate the bearing while removing heat, resulting in cooler operation.
Further, the new housings are designed with oil mist systems in mind and include provisions to accommodate pure mist and purge mist systems to suit individual applications. This results in more effective distribution of mist to the bearing for the best possible bearing life.
With improved cooling ability, the new bearing assemblies typically do not require cooling water to the housings. This eliminates problematic cooling water jackets that were commonly cast into old bearing housings and removes common failure modes, maintenance activities and associated utility costs.
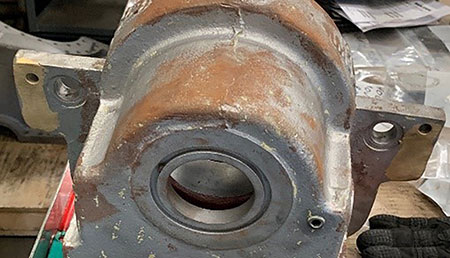
Carbon Steel Housings
Due to its competitive pricing, cast iron was a common bearing housing material in older pumps in oil and gas applications. However, this material has its drawbacks and does not meet current API standards. The 6th edition of API 610 required that bearing housings, in flammable or toxic services, be steel construction. The 11th edition extended the steel construction requirement to all services except for I-1 and I-2 material classifications.
Cast iron bearing housings are not weld repairable and can lead to increased maintenance costs. Areas needing repair often must be brazed, but this does not always result in a quality repair. Oversized bearing bore fits should be sleeved or spray-coated, which requires extra time and expense. Furthermore, after many iterations of repair, the bearing housing flanges have a reduced area to drill new dowel-pin holes, and the integrity of the part is often reduced.
The bearing assembly retrofits use new carbon steel housings that meet API 610 11th edition. This means the housings can be weld repaired and machined back to original OEM specifications, giving a like-new replacement. The reduced cost of repair can pay back the initial improvement cost in a few iterations. Some OEM pump vendors stock these upgraded assemblies, making it possible to upgrade during an unplanned outage.
Modern Instrumentation
Instrumentation has come a long way since many API pumps were originally manufactured, and these heritage designs can often be a challenge when adding modern sensors.
The retrofit assemblies include milled pads for both radial and thrust bearing vibration probes to improve asset monitoring capabilities. Axial probe and key phasor provisions are standard for pumps to be outfitted with advanced analytical systems.
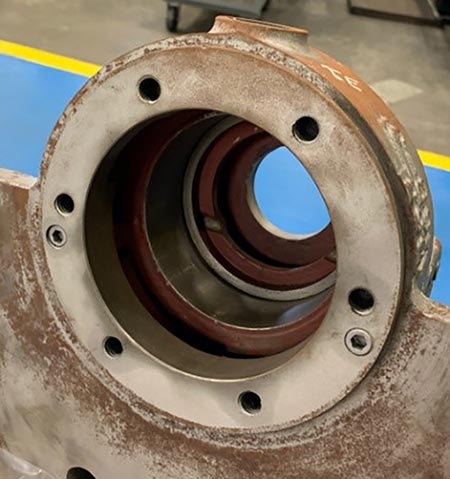
New bearing metal resistance temperature detectors (RTDs) for measuring ball bearing skin temperatures, which can get as close a 1/8-inch (3 millimeters [mm]) from the bearing bore, allow for better determination of the actual bearing temperature. Sump RTDs can be installed to determine oil temperature. Together, these RTDs aid in determining preventative maintenance intervals and provide insight on machinery health.
Upgraded Sealing
Keeping contaminants out of the pump’s bearings is crucial to extending service life. Older pump models are standardized on lip seals or deflector designs. The bearing assembly retrofit includes modern bearing isolators meeting the requirements of API 610 11th edition. These isolators eliminate oil leakage while preventing dirt and moisture from entering the bearing housings.
Bearing Designs
The retrofit project is an opportunity to analyze a pump’s needs and address recurring issues in performance. During the retrofit process, all components of the pump are taken into consideration. Typically, rotor dynamic stiffness can be improved by shortening bearing spans and increasing shaft diameters at the mechanical seal faces and the bearings. These improvements give a chance for improved mechanical seal life and reduced overall vibrations.
Older style 1.0 length of bearing/diameter of bearing (L/D) style journal bearings are updated to newer 0.75 L/D to further increase rotor dampening. Double row thrust bearing arrangements can be upgraded to the more effective paired, single-row, 40-degree angular contact bearing in a back-to-back configuration. At the same time, older ball/ball designs can be reviewed and upgraded to a sleeve ball arrangement for increased bearing life and an improvement in pump efficiency.
High-temperature applications can consider 360-degree bearing brackets to remove flexibility from the pump case to the bearing bracket and milled bracket slots to reduce thermal conduction from the case. Together, these improvements have the potential to make a considerable difference to the reliability and performance of the pump. In the oil and gas sector, where a pump’s operational parameters can change during its time in service, a retrofit project offers the opportunity to assess any other improvements that can be made. These can help to reduce both running costs through increased efficiency as well as maintenance costs, thanks to optimized reliability.