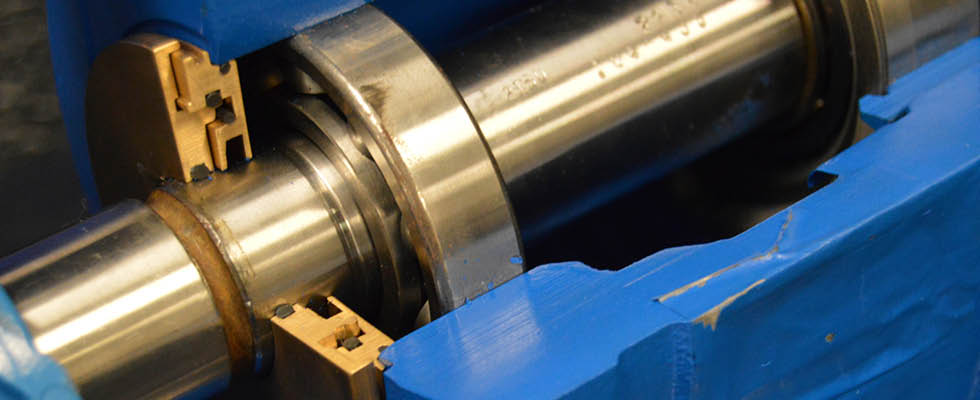
Bearing isolators enhance the performance and longevity of machinery by offering a dual function: they keep contaminants out and retain lubricants within the bearing housing. This dual functionality is crucial for efficiently operating rotating equipment across various industrial sectors.
Uses of Bearing Isolators
Pumps: To protect the bearings from the ingress of corrosive and abrasive fluids.
Motors: To prevent contamination and lubricant escape, maintaining motor efficiency and life span.
Gearboxes: To isolate bearings from contaminants and retain lubrication within the system.
Fans and blowers: To protect bearings from dust and moisture, ensuring smooth operation.
Any machinery that relies on bearings for rotational movements can benefit from the use of bearing isolators.
Functionality of Bearing Isolators
Traditional technology
Bearing isolators typically employ a noncontact labyrinth seal design, which is key to their effectiveness. This design consists of a complex path for contaminants trying to enter the bearing housing and for lubricants attempting to escape. The intricate pathway, created by multiple tortuous channels, effectively traps contaminants and lubricant, preventing direct ingress or egress. Since this methodology collects and drains contaminants, it is subject to internal obstructions, potentially allowing the external contaminants to flow internally, contaminating the oil and causing premature bearing failures. Some bearing isolators also incorporate static sealing elements, like O-rings or V-rings, to enhance sealing performance, especially in environments with fluctuating pressures or when dealing with liquid contaminants.
Newest innovations
Labyrinth bearing sealing uses the centrifugal rotational forces of the equipment to move contaminates away from the internals of the seal. These new designs do not function utilizing the condense, collect and drain method of collecting contaminants to protect the bearings. They offer excellent protection and a long bearing life.
Manufacturers use a variety of materials to produce bearing isolators, including metals, engineered plastics and elastomers. The choice of material depends on the application’s specific requirements, such as temperature resistance, chemical compatibility and wear resistance. Advanced materials like polytetrafluoroethylene (PTFE) or specialized alloys can be used for extreme conditions. The design and material selection are tailored to offer the best protection for bearings in any given environment, whether exposed to corrosive chemicals, high temperatures or abrasive particles.
Industrial Applications
Chemical processing: In environments where aggressive chemicals are present, bearing isolators made from chemically resistant materials protect the bearing from corrosion and failure.
Food and beverage production: Hygienic and cleanable designs are crucial. Bearing isolators in this sector are designed to withstand regular washdowns without compromising the bearing’s integrity.
Mining and construction: Equipment in these industries face dust, dirt and water ingress. Durable bearing isolators are essential for protecting bearings under these harsh conditions.
Oil and gas: Bearings in pumps, compressors and turbines in this sector are protected from sand, water and other particulates, ensuring smooth operation in critical applications.
Benefits of Using Bearing Isolators
Extended bearing life: By preventing contaminants from entering and lubricant from exiting, bearing isolators extend the service life of bearings.
Reduced maintenance costs: With bearings protected, the frequency and cost of maintenance and replacements are reduced.
Improved equipment reliability: Cleaner bearings means fewer failures, leading to more reliable operation of machinery and reduced downtime.
Increased operational efficiency: By maintaining optimal lubrication conditions, bearing isolators help maintain the efficiency of the equipment.
Environmental protection: By preventing lubricant leakage, bearing isolators help minimize environmental contamination.
Versatility: Bearing isolators can be designed to fit a wide range of applications, making them suitable for use in various environments and conditions.
The role of bearing isolators goes beyond simply protecting bearings. They are a critical component in ensuring the reliability, efficiency and durability of industrial machinery. Through advanced designs, materials and manufacturing techniques, bearing isolators have become an indispensable solution in a wide array of applications, contributing to the operational success and sustainability of industrial operations.