Over the last 20 years, most people have come to associate the term “hybrid” with fuel-efficient cars that combine an internal combustion engine with an electric motor. It has become mainstream technology that has spread to six-figure luxury cars. Now, the world of pump bearings may be on the cusp of a similar seismic shift in technology, except that the “hybrid” in question does not involve regenerative braking or lithium-ion batteries. Rather, the hybrid technology that is set to revolutionize the pump industry is known as the “hybrid ceramic bearing” or simply “hybrid bearing.” This term refers to a bearing that combines inner and outer rings made from standard bearing steels with ceramic rolling elements. The most common ceramic material for these applications is silicon nitride (Si3N4), although other ceramics are possible as well. The combination of these two different materials creates certain advantages that are ideal for the challenging conditions under which bearings operate.
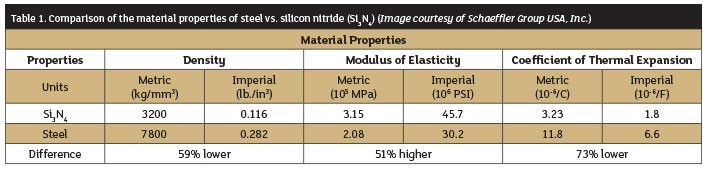