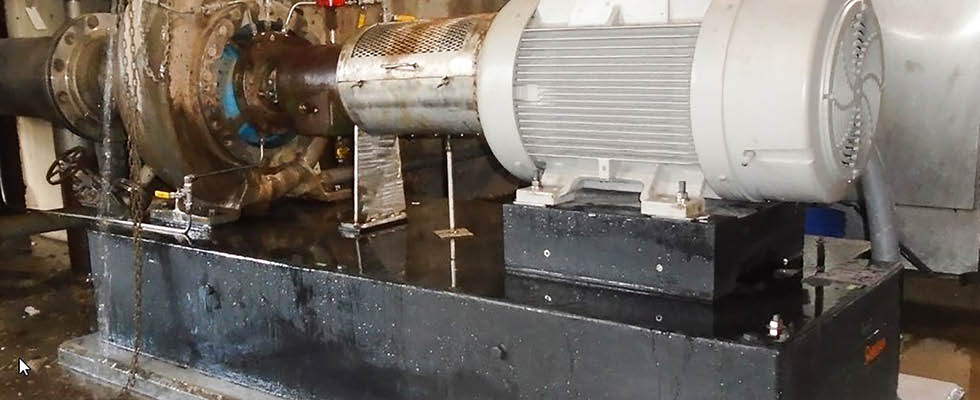
The ever-increasing cost of products and services, coupled with the difficulty of securing parts and labor for existing equipment, is a growing concern for those who work to keep industrial plants running for products the world depends on. Workforce challenges continue to be a growing pain point. Innovative products can aid in providing cost savings and efficiency with increased reliability and lower installation and maintenance activities.
One example of an innovative product continuing to gain attention is polymer concrete-based pump and rotating equipment foundations. These corrosion-resistant and easy-to-install foundations support a more than $100 billion worldwide pump industry.
Polymer concrete containing epoxy and vinyl ester resin systems were introduced over 40 years ago in the design and manufacture of a typical pump baseplate. They have continued to gain popularity, offering increased reliability by eliminating corrosion, damping vibration, preventing troublesome voids and speeding up installation. Polymer concrete baseplates will not twist, bend or diaphragm like most standard metal designs. Alignment is easier to perform and maintain while grouting is simplified by reducing the amount of material required and eliminating the need for detailed surface preparation.
Traditional Installations
Historical installation of a solid polymer base, or hollow steel or cast-iron baseplate, is to combine the unit with some type of elevated structure to raise the equipment further off the ground floor. This is done to align with suction piping and to
promote better housekeeping and maintenance activities.
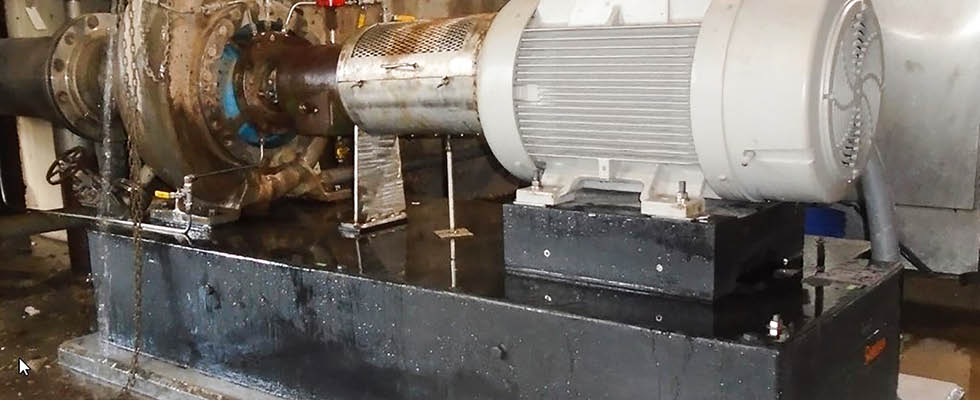
These elevated pedestals have customarily been constructed of concrete and are formed and poured on site. New installations take considerable time, ranging between three and four weeks for the concrete to cure before a secondary operation is performed to mount and grout the separate pump base to the cured concrete structure. Concrete will be susceptible to harsh plant environments, and while coatings can be applied, they still tend to deteriorate and fail in aggressive applications.
Over time, these concrete foundation/pedestals often show signs of stress cracks, and the upgrade of old failed steel bases can extenuate cracking during the removal process. These failing concrete structures often must be removed or repaired to provide a reliable solution for the mounting of a new base plate.
New Designs
Precast polymer equipment foundations offer a one-piece solution that incorporates both the pump mounting surface found in the conventional baseplate and the poured concrete pedestal. The original concept has been around for years, and newly patented designs allow for quick and reliable installation. This eliminates most of the typical processes and headaches associated with conventional construction procedures. These foundation systems increase reliability, speed-up installation and save cost (Image 1).
Key design features and benefits of a pump foundation system include:
- Combined base and pedestal: eliminates field labor and potential errors of mounting base in the field, proving single point accountability.
- Reliable construction: eliminates multiple parting lines and sources
- for failure while maintaining full corrosion resistance for the entire foundation system.
- Quick installation: removes forming, curing and coating of concrete. A single unit is delivered to the jobsite ready for installation. Typical installation is reduced to only two to three days. Turnarounds and outages are more accommodating. Labor is greatly reduced.
- Eliminates voids: grout delamination from metal bases cannot occur, and voids are non-existent by design, as the entire assembly is manufactured in a controlled environment.
- Precision mounting: all mounting surfaces are factory built to tight tolerances that are not subject to stresses and potential change during installation. Soft foot and bolt binding is greatly reduced, if not eliminated.
- Easy retrofit: greatly reduces issues with existing old concrete repair.
- Less maintenance: no need to provide or maintain expensive engineered coating or paint.
- Vibration damping: polymer concrete is proven to dampen vibration more than 20 times better than steel, cast iron and other natural products such as granite.
Advancements in Design
The first concept of a one-piece polymer foundation was introduced in the early ‘90s, and many users quickly found the benefits, especially for new installations and larger scale construction projects. Earlier designs were primary hollow core polymer boxes that required additional field work to adjust to final height and fill. Advancements in the second generation of this product include solid polymer foundations arriving, requiring much less labor to install. These designs are cast to exact height and are typically epoxy grouted to an existing surface for final installation or can even be buried below grade.
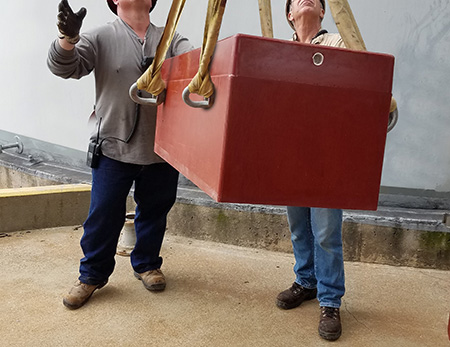
The latest technology may also include thick, internally reinforced walls that eliminate stress cracking and also do not require filling. All designs include mounting locations for the pump and motor that are extremely flat and parallel, facilitating easy alignment without being bolt bound or causing excessive soft foot. Equipment mounting inserts are available in a wide range of materials, and provisions exist for field replacement or addition if required.
Internal grounding is common, as the corrosion resistant polymers are non-conductive, and a wide range of motor adjusters and polymer mounting blocks to maintain equipment centerlines are available. Threaded leveling locations aid in proper installation, while anchoring locations are typically either non-existent or completely sealed from the process elements. Side lifting locations (Image 2) help easily position units in place, and some designs even include leveling vials for rough initial alignment.
Reliability With a One-Piece Solution
In most cases, the reliability of rotating equipment can be traced directly to the surface foundation. Some estimate that over 75% of pumps are pulled from service due to mechanical seal and bearing failures. A sound foundation can certainly increase the mean time between planned maintenance.
As labor and resources continue to be scarce moving forward globally, new advancements in designs can aid in both increasing reliability and reducing ongoing maintenance and initial installation costs. A new method has arrived for installing pump assemblies, incorporating both the typical equipment base and pedestal into one simple foundation system, providing a reliable structure, arriving field ready and eliminating and minimizing many of the typical steps during installation.