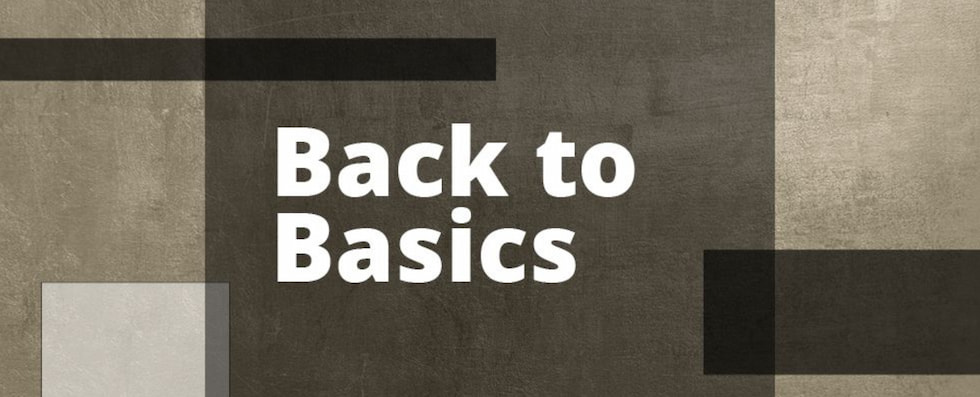
There are many reasons for such overwhelming interest on best efficiency point (BEP) and performance curves. BEP and desired operation at or around BEP is closely related to energy savings. Also, the operation at/around BEP is logically related to the pump selection and it links to some serious points such as the pump sizing, bid tabulation, manufacturer selection and tense discussions often happening between pump vendors, purchasers, consumers and operation teams at key stages of projects. BEP is also closely related to the operation, reliability and possible failures, repairs, maintenance, etc. BEP, particularly plausible deviation from BEP during parallel operation, is one of the main considerations for the performance and reliability related to parallel operation of pumps. Nearly all parties involved in a project deal with BEP and performance curves.
Operation Far From BEP
The internal flows of pumps are complex, and it is difficult to note what will exactly happen for pumps when they are operated far from BEP. This article covers some general guidelines and approximate figures about BEP and its effect on the selection, sizing, operation and reliability of pumps. This is to help better assess dangers and risky operation.
Many engineers and experts agreed that pumps should be sized and selected to operate most of their life at or near BEP. There is no question about this key requirement. But, how can this be achieved? What factors should be considered to achieve this important goal? What might prevent or impair that ideal long-term operation at or near BEP? How will each party involved (engineers, consumers, purchasers, vendors, operators, etc) affect this requirement, and how each will be affected.
Possible Overestimation of Head
Users often overstate head requirements when they specify pumps. Too often, there are multiple engineers involved in the overall design and sizing process. Each one may add 5 to 10 percent factor to the head or capacity, and as a result, added margins to the head would be remarkable.
Overstating the head with a pump selected to operate at BEP finds the actual duty point moving right on the curve. In other words, as different safety factors and margins are added to the head by process, operation and mechanical engineers during the design, the selected pump might be bigger than needed and, in the operation, the pump might operate most of the time to the right of BEP.
In fact, the above-mentioned cases of the overestimation of head and the selection of the pump with more power ratings and head capability actually happened. However, there are two other factors that prevent such cases of gross overestimation of the head.
The first and most important limiting factor is tense competition of pump vendors and manufacturers over the cost reduction particularly at bid tabulation and selection stages. Although vendors and manufacturers use state-of-the-art software and programs to size/select pumps accurately, those software and methods seldom oversize the pumps or their drivers due to the pressure to keep costs down. In other words, the actual performance of pumps is usually at the predicted performance or slightly below it.
The author has been invited to different shop/site performance tests and at nearly all of them pumps were performed at theoretical predicted curves or below the curves. In most cases, the actual performance at the performance tests were just slightly below the predicted performance curves. This shows the accuracy of those so-called predictions or theoretical curves by reputable pump manufacturers. However, cases of over-performance were rare.
As pumps are selected based on lowest costs, pump manufacturers tune the overall sizing, selection and design process to bare minimum margins and factors on their side. Obviously pump manufacturers should not be blamed for this practice, because cost-based selection is imposed by end users. However, everybody should be aware of this process, the interaction and their consequences.
Another consideration is the actual system including piping and equipment in the process can impose more friction and head loss than what were initially predicted. In nearly all cases, the final/actual length and complexity of the piping are more than predicted during pumps selection. This leads to the fact that in real plants and facilities, more head is usually needed than the initial head estimate.
This is not just for commissioning and startup, but virtually any degradation or deterioration in the system including pump itself, piping, downstream, etc., means there will be more friction and head loss as time passes and more power will be wasted. In other words, nearly all unpredicted events during different stages of detail design, installation, commissioning and operation leads to more head being needed in the system. Most often, those independent factors added by different people turn out to be required.
It is true that independent safety factors and margins added to the head by different engineers and representatives might theoretically lead to overestimation of the head and power, and purchasing of a larger pump than needed. However, there are other limiting factors that have prevented such an overestimation in many cases. There has been a limited number of pumps that were actually oversized. In real world cases, where cost-cutting and cost-based selection dominate, most pumps were slightly undersized, and there are more complaints about low power ratings and low heads in actual operation.
BEP, NPSH & Temporary Operation at Left/Right Sides of BEP
Every pump should be sized to work most of the time at or near BEP. However, it is wrong to assume every sizing parameters or factors, such as net positive suction head (NPSH) margin, should be checked and verified only at or near BEP. Just the opposite: Pumps might be pushed to operate temporarily at left or right side of BEP and everything should be ready, safe and reliable for such plausible operation.
Typically the NPSHr (required) curve begins to swing up quickly at BEP (or just left of BEP). If the only NPSH margin (NSPHa – NPSHr [NPSH available – NPSH required]) at BEP is considered and verified, there is a possibility the pump operation at the right side of BEP, even slightly right of BEP, can lead to cavitation. A selected pump should be able to operate temporarily at any point on its performance curve. NPSH margin should be checked and verified for the entire performance curve. As NPSHr is at highest at right side of the BEP, it should be verified that there is enough NPSH margin at right side of the performance curve as cavitation is not acceptable even if the pump is pushed to operate temporarily at high capacity points.
So, here is the general rule: A pump should be sized to operate most of the time at or near BEP. At the same time, temporary operation at the left or right side of BEP is possible and plausible. Such an operation might not be desired but may happen during transients or predicted/unpredicted events. Therefore, it should be safely and reliably managed. Every sizing factor and parameter including NPSH margin should be checked and verified accordingly.
BEP & Parallel Operation
Parallel operation of pumps is one of the most oversimplified concepts in the pump industry. As a result, there have been many operational problems, complaints, failures, shutdowns and financial losses associated with mistakes and wrongdoing in the parallel operation of pumps.
One risk of parallel operation is that one pump is pushed to operate at points far from BEP. In long-term operation, this can mean energy waste, low reliability and risks of failure. There can be many reasons for such an undesired operation where a pump is pushed to operate far from its BEP. The complete list of reasons and root causes of such faulty operation are outside the scope of this article.
One reason for operational problems could be differences, tolerances, deviations and degradations in so-called identical pumps in parallel operation where a pump is pushed to operate at points far from its BEP to catch up with the head generated by other pumps. This prolongs operation far from BEP and can lead to operational problems or failures. In fact, parallel operation of pumps should be avoided where possible.
However, all the above-mentioned risks and precautions do not mean that the parallel operation of pumps is impossible.
There are cases where the only feasible pump options are pumps operating in parallel. If pumps are selected properly for parallel operation, and if all operational cases were carefully simulated and verified, the parallel operation would be safe and reliable. To start, the performance curve of pumps in parallel should not be flat or relatively flat as any small change in head would lead to a shift of the operating point away from BEP. There should be other precautions and requirements depending on each specific case of pumps in parallel operation.
A more complicated and riskier situation is the parallel operation of dissimilar pumps. In fact, this topic is an overlooked and neglected one in the pump industry. In many cases, different pumps have been installed to operate in parallel without proper assessment and the result would be problems, failure and breakdowns.
An interesting configuration is when multiple pumps are operated in parallel where a couple of pumps are operating at fixed-speed and one (or two) pump(s) is controlled by a variable speed drive (VSD). Such a configuration is used with the promise of fine flow management, where the fixed speed pumps provide the base-flow and the VSD pump(s) operates at variable-flow for the flow adjustment. A concern is that this VSD pump would operate against so-called fixed headed pumps and, therefore, can potentially operate far away from BEP. For instance,
it might operate at lowest possible speed with a low flow, whereas the operating point is at the far-left side of BEP. Obviously, such an operating case in the long run would cause problems.
The configuration of fixed-speed pumps and a VSD pump has been widely used due to low initial costs. However, it should be recognized that this is a complicated configuration and it is theoretically categorized as the parallel operation of dissimilar pumps. Although the pump casing of the fixed-speed pumps and VSD pump may be identical, their operational details are different (fixed-speed drivers versus VSD driver), and they are actually dissimilar pumps in parallel operation.
Within cases of the parallel operation of pumps, the parallel operation of identical pumps is considered less risky and the parallel operation of dissimilar pumps should be avoided.
However, there have been still cases where the parallel operation of dissimilar pumps should be selected as the only available option and it should be managed properly. For such a risky operation, pumps should be selected carefully, and everything including the control system, operating envelope, operational procedures, etc., should be managed to avoid dangers and risks.
Obviously, a significant risk is the situation where a pump can be pushed to work far from its BEP over a prolonged period of operation. Simulations of all possible operating cases and considering all possible factors and parameters such as plausible deviations, degradation and others are important for proper risk assessment. In the next step, corrections and improvements are needed to prevent such problems and risks.