System designers frequently place strainers on the suction side of a pump. This practice, ostensibly based on good intentions, is rarely a good idea and will create serious issues for the pump from the aspect of reduced and turbulent flow, inadequate net positive suction head available (NPSHa) and eventually blocked flow. The consequential reduction in NPSHa will create deleterious effects for the pump and the downstream system. These effects will always manifest as negative and expensive issues. Due to vibrations from cavitation and poor seal face lubrication from mixed phase fluids, the mechanical seals, like canaries in the coal mine, are typically the first component to fail, followed shortly by the bearings. These events create reductions in efficiency and add to unscheduled downtime, which all add to the total cost of ownership. There are several acceptable methods and alternative designs to avoid these issues. There are also situations where placing the strainer on the suction side is the right thing to do, but it must be done correctly.
Background
Normally the reasons for placing the strainer on the suction side of a pump seem like good ones, as it is prudent to protect the pump and the other ancillary components in the system. This preventative design approach can work to preclude or mitigate fouling of heat exchangers, valve blockages and other component issues with small operating clearances and annulus voids, to name a few. In the case of some positive displacement pump types such as gear and screw pumps, it is imperative.General Comments
There are several issues with placing the strainer in the suction line. The first issue is that the strainer will inevitably clog. The clogging will reduce, and at some rate of closure, completely shut off flow to the pump suction, creating serious damage to the pump. The blockage also creates issues with the system and downstream components that rely on the flow provided by the pump. Example: another pump in series with the first pump. The second issue is a marked reduction in NPSHa. The formula for NPSHa is shown below for reference. Every pump has a requirement for a given amount of suction energy that is referred to as net positive suction head required (NPSHr). The specific requirement is determined by the manufacturer and is published on their performance curves. The NPSHr data is determined by empirical means. If you have read some of my previous articles, you already know that the suction side of the system must provide energy to deliver the liquid to the pump. The pump does not reach out and pull the fluid into the impeller. The pump does not suck the fluid into itself, as fluids do not have tensile strength. The suction system must provide a level of NPSHa. The level of NPSHa is either calculated or measured by the owner or operator of the system. It is imperative that there is more NPSHa than NPSHr. This difference is referred to as the margin. The Hydraulic Institute (HI) and American National Standards Institute (ANSI) have a published standard that covers this subject—ANSI/HI 9.6.1-2012. The issue with insufficient margin is cavitation and the subsequent deleterious effects from cavitation, which include material damage (usually manifests on the impeller), vibration, mechanical seal and bearing damage, loss of efficiency and loss of flow or partial flow.The formula for NPSHa
Remember that we are calculating NPSHa, so we do not need to include velocity head. Velocity head would be included if we were measuring NPSHa. Equation 1 NPSHa = ha – hvpa + or - hst – hf Where: ha = the absolute pressure. Absolute pressure as measured in feet of head of the liquid being pumped at the surface of the liquid. hvpa = the vapor pressure. The head in feet corresponding to the vapor pressure of the liquid at the temperature being pumped. hst = the static head of the liquid over the pump centerline for a flooded suction in feet (positive value for flooded suction) hst = the static head of the liquid below the pump centerline for a lift situation in feet (negative value for lift situations) hf = the total friction loss in feet of head for the suction side systemIssues with a Reduced Margin
The friction component of the NPSHa formula becomes increasingly large when the strainer becomes clogged. This is a negative component in the formula and as a result the reduction in available NPSH will cause the pump to cavitate. If you look deeper into the cavitation phenomena, the reduction in flow caused by the restricted strainer will result in a higher velocity across the device. The fluid in the suction line must obey the law of conservation of energy, which states energy can neither be created nor destroyed, but it can be altered in form. This is best summarized in Bernoulli’s equation. Bernoulli’s Law, simplified for this article, explains why the pressure will drop correspondingly as the velocity increases. The clogged strainer is why the velocity has increased in the first place. As the pressure drops, the vapor pressure will also be affected, and it is possible at some point for the liquid to change state and form a vapor. Centrifugal pumps are not capable of pumping air, vapor or non-condensable gases. If there is as little as 4 percent entrainment in the liquid, it can bind (vapor lock) the pump. The higher the temperature of the liquid, the higher the possibility for this phenomena to occur. I have covered details of these phenomena in four other articles in Pumps & Systems magazine.- How to Reduce or Eliminate Air Entrainment (December 2017)
- Most Common Reasons for Air Entrainment in Pump Systems (December 2017)
- Guidelines for Submergence & Air Entrainment (April 2016)
- 10 Common Self Priming Pump Issues (September 2015)
Oil & Gas Applications
In oil and gas applications where the pump is upstream at the well head, there is simply no way to avoid the introduction of solid containments and dual phase fluids to the pump suction. It is extremely rare that a fluid coming out of the ground will be 100 percent gas free. A centrifugal pump cannot pump (compress) air or gas. The comparative difference in the range of fluid densities is a factor of approximately 800. Different designs and sizes of pumps handle this issue in better ways than others, but at some level all centrifugal pumps will vapor lock and fail. The impeller eye will become blocked by the air, vapor or gas.Lift Situations
If the pump is a self-primer or simply a centrifugal pump placed in a lift condition application (externally primed), there can or will be performance issues should any restriction be placed in the suction line. Note that “lift” signifies that the level of the source liquid to be pumped is below the centerline of the pump impeller. The available NPSH will already be low because the static head component in the formula is now a negative quantity due to the lift condition. Further restrictions will add to the negative component of friction and for any temperature above ambient the vapor pressure component will also work against the pump. “OK, I understand you, but I need to have strainers on the suction side.” Assume you must have strainers on the suction side of the pump. Now what? If there are strainers on the suction side of the pump, the best step you can take is to add instrumentation and continuously monitor the differential pressure (DP) across the strainer. The strainer will have a resistance coefficient assigned by the manufacturer. This is a great place to use an automated alarm system. The DP across the strainer for both clean and dirty conditions should be known. There must be a low value of DP for the new and clean strainer; I prefer less than 2 pounds per square inch gauge (psig). Also, you can compare the low clean value of DP to a higher value for a clogged strainer as indication for action. Note: You have to know the head loss across the strainer anyway to do the NPSHa calculation. How else would you know if there is sufficient margin in your design? If the DP across the strainer is not automatically monitored and alarmed, then an operator must check on a scheduled basis. All changes must be recorded and action must be taken if the DP is out of specification. Even a difference of 1 or 2 psig DP can be the difference between success and failure. I suggest using a duplex gauge rather than two separate gauges, due to differences in system losses and gauge inaccuracies. A differential pressure transducer is normally better than a duplex gauge. Some of the better designs incorporate a duplex strainer arrangement so that one strainer can be offline for cleaning and maintenance with no disruption in service. Some designs automatically change over and clean with no operator action required. The size of the suction pipe must have an adequate diameter to keep friction losses down and velocities in an acceptable range. I always recommend to keep liquid velocities on the suction side below 2 meters per second (6.6 feet per second) at the maximum, and one meter per second (3.3 feet per second) is better. Just as the suction pipe size must be adequate, so must the strainer size.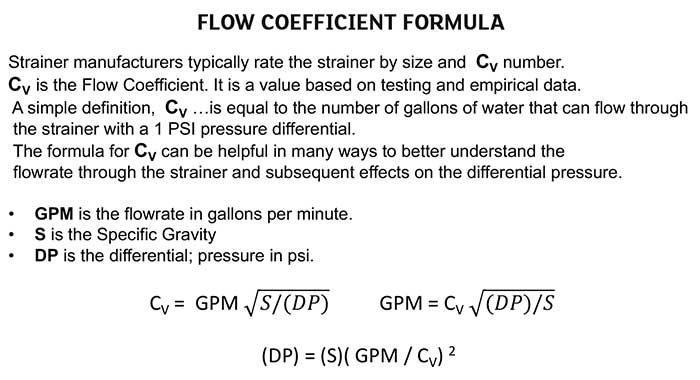
Acquiesce on Strainers & Filters on Suction Side
It is noted and acknowledged that many processes are purposely designed to have strainers on the suction side of the pump. Some processes actually rely on the reduced pressure (vacuum) created in the process. An example would be a filter press. Note these systems and pumps are designed and instrumented for the additional stress.Conclusion
Every rule usually has exceptions, but from the perspective of an industry best practice, I suggest thinking long and hard before the placement of strainers on the suction side of the pump—and you “exceptions” already know who you are. Many pumps are designed to handle some amount and size of solids. The manufacturer can or will advise what size solids the pump will handle. It is typically a better idea to place the strainer on the discharge side of the pump if possible. If you must place the strainer on the suction side for a valid design reason, then take the proper steps to design the system to prevent pump issues caused by clogging. For more than 48 years, I have watched in amazement as operators destroyed their pumps by starvation.Strainers & Filters
One person’s strainer may actually be another’s filter. Some people use the terms interchangeably, but typically the term “strainer” is actually a subset of “filter.” I have used the word strainer throughout the article, but note it could also be a filter.
A strainer removes solids from a solution using a purely mechanical and particle size-based sieving process.
If the particle is larger than the size of the holes, it will not pass. If the particle is smaller than the holes, it will pass.
Filter is really a general term. It describes a device that removes solids from a fluid that is passing through the filter media. The solid could be removed by straining, but it can also be removed by other methods.
Technically, some people define a filter at less than 75 microns and a strainer at 75 microns and larger. In my experience, the colloquial expression is to use the word “strainer” if the device has a metal screen, regardless of the mesh size. Otherwise, the word “filter” is used if the device has bags or cartridges, regardless of the micron rating. You may have other definitions in your facility.