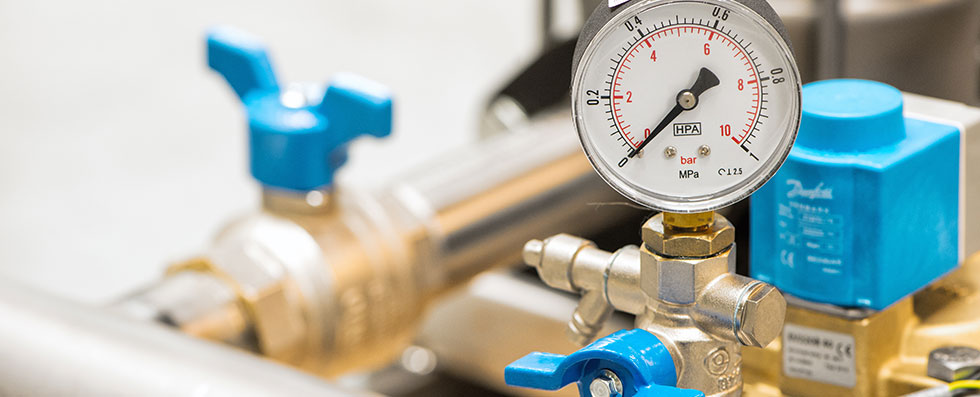
Bourdon tubes are a popular pressure gauge used to measure the gauge pressure of liquids and gases. Gauge pressure is the pressure of a fluid media relative to the atmospheric pressure. Bourdon tube pressure gauges are mechanical. They do not use an electrical signal to work. They measure fluid pressure within the range of 0.6 to 7,000 bar or 8 to 1,000 pounds per square inch (psi). Since this pressure gauge can be used for low-pressure, vacuum and high-pressure applications, it is common in most industries.
Bourdon Tube Working Principle
Before looking at how the bourdon tube works, first highlight its parts and components.
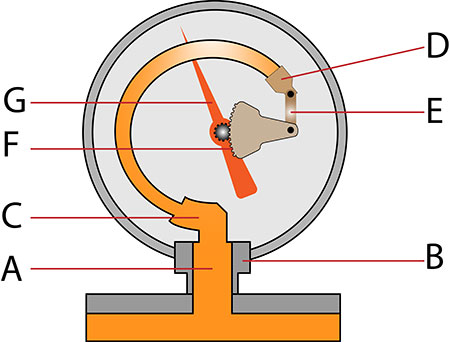
(C) stationary end, (D) moving end, (E) pivot and pivot pin, (F) sector gear, (G) indicator needle.
From Image 2, it is clear that the bourdon pressure gauge is attached to the pipeline of the system’s inlet pipe. The socket block holds the inlet pipe in place, allowing the pressure to flow into the stationary end of the tube. This pressure is distributed throughout the elastic C-shaped tube between the fixed and the moving ends. As the inlet pressure increases, the C-shape tube straightens. The pivot and pivot pin attached to the moving end of the tube connects this movement with the sector gear. This leads to an amplified motion which causes a deflection of the indicator needle for every small change in inlet pressure. When the inlet pressure increases, the indicator moves clockwise (from left to right) over a calibrated scale. Once the pressure drops, the tube regains its helix shape, and the indicator moves in an anticlockwise direction (from right to left).
Due to its design, the bourdon tube is sensitive to pressure changes, making it suitable for high-precision applications. It is also resistant to corrosion and vibration.
Selection Criteria
When choosing a bourdon tube pressure gauge, users need to pay attention to your current and future system requirements. Some of the factors to consider include:
Gauge material and diameter
Common gauge materials include stainless steel, copper alloys and aluminum. The right material will depend on the chemical properties of the fluid media. When working with corrosive fluids, it is advisable to use stainless steel or aluminum. However, aluminum is not suitable for high-temperature applications. Copper, on the other hand, is not ideal for high-temperature applications and does not handle highly corrosive fluids.
The dial size of bourdon tube pressure gauges ranges from 1 to 16, representing a 25 millimeter (mm) to 406 mm range. That said, users should consider the readability and space limit requirements when choosing a dial size.
Temperature and pressure range
The system’s maximum and minimum operating pressure will determine the right pressure gauge to choose. Always ensure the bourdon tube is not subjected to excess stress. For optimal operations,
the maximum working pressure should not exceed 75% of the gauge’s full-scale range (for steady pressure) and 65% of the maximum scale value for pulsating pressure.
For dry or silicon-filed pressure gauges, the normal temperature ranges are (-40 F to +140 F) or (-40 C to +60 C). That said, oil or glycerin-filled pressure gauges handle pressures within the range of (-20 C to
+60 C) or (-4 F to +140 F). From the two types, glycerin-filled gauges are best used with warmer fluids. They are also suitable for measuring pulsating pressure.
Vibration resistivity and corrosion resistance
In applications or environments with little to no vibration, a dry gauge works fine. However, when the application or system involves some vibration, it is best to choose a wet gauge since the dry gauge will distort measurement readings. The liquid in the pressure gauge is designed to absorb any vibration and pulsation, allowing for easy and accurate readings. If the pressure pulsation or spikes still interferes with the readings, users can use a pressure gauge snubber to suppress the unwanted force. With highly corrosive fluids, liquid-filled stainless steel gauge pressures are recommended. The glycerin or oil inside the gauge helps lubricate and protect against corrosion of the deflecting pointer.
Other aspects to consider
Besides the factors identified above, there are other small and seemingly insignificant aspects to keep in mind. These include the mounting options and the pressure units. Ideally, bourdon pressure gauges are available with panel mounting or vertical/ horizontal threaded connections. The two common pressure units are bar and psi. Always check on these factors before buying a bourdon pressure gauge.
Use Cases & Benefits
As one of the most common pressure gauges in the market, the bourdon tube type finds application in different industries. Some of the common use cases include:
Manufacturing and processing: They are common in processing plants where pressure measurements of the various fluids are critical for optimal system operation.
Agriculture: Bourdon tubes are used in agricultural sprayers to keep the pressure at the desired range.
Water supply systems: These pressure gauges are used to maintain optimal working pressures to ensure water is delivered to the desired distances at the right pressure.
Other use cases are in the automotive, marine and aerospace industries and heating, ventilation and air conditioning (HVAC) systems. Some advantages offered by bourdon tubes include:
high accuracy when used in low and high-pressure applications
enhanced safety when used in high-pressure systems
a compact and durable design
relatively low cost for its premium features
supports dynamic pressure loads and works well under heavy vibration
Bourdon tubes are popular pressure gauges used in different industries thanks to their flexibility, high accuracy and sensitivity. When choosing a bourdon tube pressure gauge, always prioritize the system requirements and pay attention to the factors discussed in this article.
Users will also want to choose bourdon tube gauges from reputable manufacturers. This minimizes the risk of picking a low-quality product. Where possible, consider seeking professional guidance from an expert and trusted third-party professional during the selection process.