Since the installation, the ozone systems have kept both pulp bleach lines operating with more than 99 percent reliability.
07/08/2016
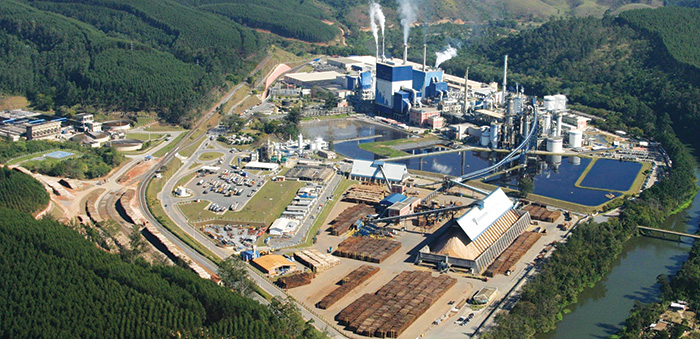
Franz-Josef Richardt is global product manager for ozone systems at Xylem and has been with the company for more than 20 years. He has more than 30 years of industry experience. Richardt has a degree in process engineering from the University of Applied Sciences in Cologne, Germany.