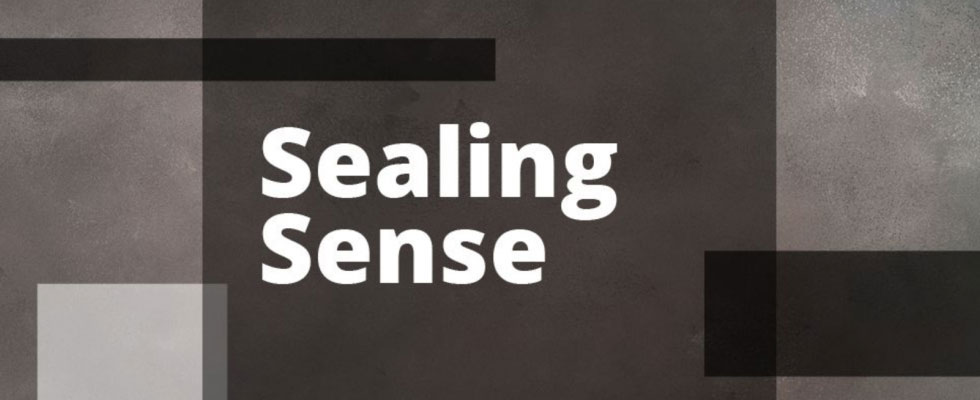
Often, plant personnel is put into the awkward position of balancing running for longer to meet the demands of expanding production and lowering downtime to maintain equipment. Companies are looking to extend operating efficiencies by prolonging scheduled maintenance. Premature pump packing failures caused by other pump components can cause expensive delays.
The bearing of a pump is critical. If it is not performing properly, it can put other pump components at risk such as the impeller, shaft sleeve, packing, gear box, motor and bearing seals. This article will identify the specific relationship between packing and pump bearings, and it will provide options to correct problems using the best available braided mechanical packing solution for an application.
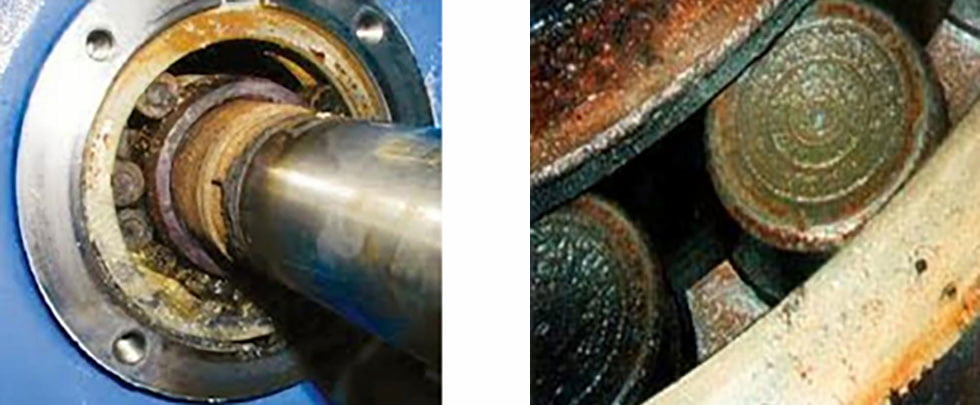
Bearing Specifications
Keeping bearings properly lubricated and maintained is critical to keeping a pump operating at its proper efficiency. Monitoring the health of the equipment during its hours of operation will help improve the overall performance of the plant’s systems. Understanding the common causes of bearing failures such as inappropriate selection, overloading, equipment misalignment, incorrect installation, lubrication failures and contamination will result in making better decisions to maximize plant productivity. It is important to identify the correct type, style and material component of the bearing being used for a particular application. Using a bearing that has been incorrectly sourced (like a spherical roller versus a deep groove ball) or one that is the inappropriate material, race, cage type, load or performance range can lead to failures. Another important parameter of the application is the rotational speed. Equipment’s operating speed, or rotations per minute (rpm), can generate heat for the application that may adversely affect the bearing and the adjacent components.
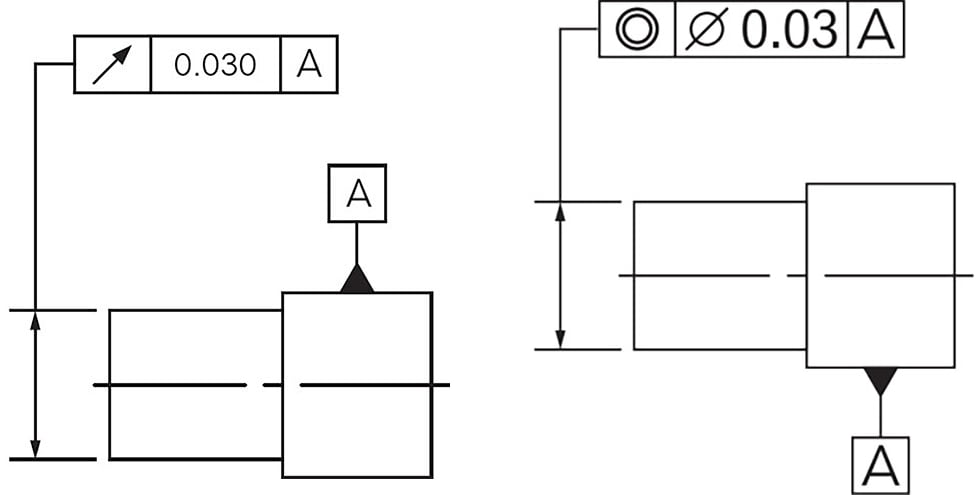
Conditions & Challenges
Once a pump starts to experience some component of a bearing problem, the pump shaft will begin to move, creating an increase in clearance. As the clearances to the equipment’s shaft/sleeve change, the runout or concentricity (commonly used terms) will change.
How do these conditions influence a proper seal? Runout is defined as the total variation that a reference surface can have when the part is rotated around the datum’s true axis. Concentricity is the tolerance used to establish a tolerance zone for the median points of a cylindrical part. Another case that can certainly exasperate both tolerance conditions would be the use of a bolt-on stuffing box. There are many times users can be so focused on the condition of shaft surface finishes that they overlook the connections between the stuffing box bolt circle and inside diameter (ID) of the box bore to the outside diameter (OD) of the shaft or sleeve. These points of measurement on a shaft or shaft sleeve can play an important part in understanding the relationship between the stuffing box ID dimension, the pump shaft OD and packing cross-section. It is always useful to check a shaft and/or sleeve with a dial indicator gauge. This is one way to get an accurate measurement of pump’s concentricity. It is not always clear to plant personnel when these occurrences start but incrementally the packing life will become shorter and shorter. There will be a point when the user will start to question the performance of the equipment’s mechanical seals or packing sets. The next step would be to consider other recommendations for a new seal face combination or even a new type of seal. If mechanical packing is being used, the plant may want to consider new material types or even special packing arrangements to help extend and improve sealing life.
Plants are confronted with equipment experiencing shaft movement from either pumps, mixers or other applications like hydro pulpers. Hydro pulpers can run into these problems as a result of being a bottom entry design where the bearings can easily become contaminated from the pulp and water process media. Large bales of recycled cardboard are dropped into this large device that acts as a centrifuge, and if the water levels are too low, there is a risk of slight momentary shaft movement. This movement will occur to one side of the shaft as these large bales hit the spinning blade and are broken into smaller pieces, mix with water and become the process medium. Because of the nature of the equipment design, there are tendencies to increase the flush pressure to a higher flow rate to overcome the process medium migrating into the stuffing box, bearings and gearbox.
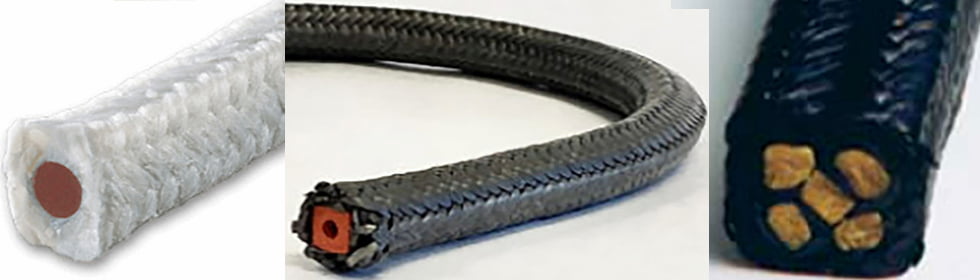
Packing Materials & Styles
Mechanical packing manufacturers have always been up to the challenge to develop many types of braided packings to help improve sealing performance for these troubled applications. Packing manufacturers have combined many types of the latest yarn materials such as polytetrafluoroethylene (PTFE), graphite/carbon, aramid fibers, PTFE/graphite with a variety of rubber O-ring materials like fluorocarbon-based fluoroelastomers (FKM), silicone, nitrile and ethylene propylene diene monomer (EPDM) in the packing cores to help improve and extend sealing performance. These same manufacturers have also developed rubber core packings using one single, solid center core to packings using hollow center core designs. There are packing styles that even use up to five cords in their braided packings, which not only use the center core but now add smaller size rubber cords into the four corners. Beyond using the typical round O-ring cord in the center of packing, manufacturers have introduced other shapes like squares and diamonds into the design to improve sealing performance.
When comparing packings and manufacturers, end users should know that they are not all the same. Beyond the material differences of the yarn, the packing is constructed with rubber cord compounds that can have different hardness (durometer) and sizes. These factors will contribute to the amount of deflection a packing can absorb. Working with a packing manufacturer that understands the needs of the application and equipment and can guide users to the best braided packing sealing solution is important.
We invite your suggestions for article topics as well as questions on sealing issues so we can better respond to the needs of the industry. Please direct your suggestions and questions to sealingsensequestions@fluidsealing.com.