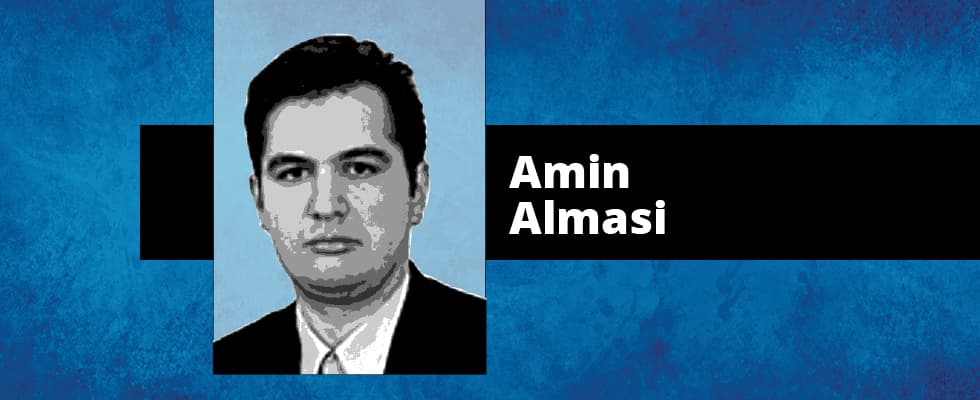
There have been many reports of high vibration, operational problems and failures of pumps due to misalignment. Considering all these effects, can users accept a deviation to the misalignment limit for a pump?
Misalignment
If alignment is not achieved, shaft misalignment occurs, which may be parallel, angular or both. Misalignment can cause increased vibration and high loads on the key pump parts and components. This leads to improper operation and problems. The more misalignment, the greater the rate of wear and likelihood of premature failure and loss of pump efficiency—plus, misaligned pumps consume more power.
Parallel & Angular Misalignment
There are two types of misalignment: parallel and angular. With parallel misalignment, the centerlines of both shafts are parallel but are offset. With angular misalignment, the shafts are at an angle to each other. The parallel misalignment can be further divided up into two perpendicular directions such as horizontal and vertical.
Misalignment should be reduced to the minimum value possible—practically and economically. On the other hand, absolute perfection in the alignment of shafts is not realistically possible, nor is it even needed. A critical issue is quantification of the alignment quality and determination of allowable deviation to the alignment tolerance.
Can a Deviation Be Acceptable?
The fact is the alignment of pumps, particularly large, critical ones, has been a difficult trial and error task, and sometimes the targeted alignment values cannot be reached, even after many attempts. In those cases, misalignment values measured for the final alignment are more than allowable (specified) values. A deviation might be temporarily accepted pending thorough verifications, provisions and satisfactory operation and vibration measurements during startup and actual operation, including various cases of operating conditions. Vibration signatures have been promoted for studying pump malfunctions, such as misalignment.
This can be used for such verification to make sure the accepted deviation will not cause any problems.
In those cases of deviations, a proper investigation should be done first to make sure there is no issue or damage with the involved pump components. There have been cases where the misalignment limit could not be reached and later it was found that there was serious damage during the installation of the pump. Many pumps are sensitive pieces of equipment and if the step-by-step installation procedure is not followed strictly and the site installation is done carelessly, then damages and problems might be expected. Good site inspection is the key to success.
However, there is always the possibility of damage. For instance, a bearing might be damaged or the shaft might be permanently deflected or bowed. There is a possibility that such a problem or damage could cause difficulties in the alignment. In other words, if proper alignment cannot be achieved in many attempts, the contractor or manufacturer should explain why such a deviation happened and how it may affect the long-term operation and reliability of the pump. A comprehensive report dealing with all these matters is needed in any case of deviation.
Tricks, Options & Solutions
In the wake of an unsuccessful alignment, some vendors or contractors may attempt to change the alignment criteria, limit or even the alignment procedure. New interpretation or manipulation of alignment procedures, criteria and limits might also be tried by some vendors or site contractors. The fact is, any case of deviation should be treated with great care. A deviation might be accepted if safety and reliability are ensured and additional provisions and measures are considered. However, this is not a good practice to try to change alignment criteria or specified limit in case of a deviation. The modification of limits or criteria is usually not acceptable.
The good news is excessive misalignment during operation can be found by accurate analysis of vibration. Therefore, in case of a deviation given for misalignment, the situation can be reevaluated or verified by accurate vibration measurement during startup and the initial period of operation. In such a case, a comprehensive vibration measurement exercise should be done and reported using all available vibrational sensors. The exercise should fully prove that there is no sign of pending issues or developing problems for all possible operating cases. Although a comprehensive vibration measurement is required and all aspects should be considered and evaluated, “2× harmonics” and “axial measurement” need more care as these are usually indicators of an alignment issue.
Flexible Couplings & Misalignment
Flexible couplings are provided to allow different shafts of pumps (and machinery in general) to be connected with little misalignment. In other words, flexible couplings use one or two flexible members or an elastomeric insert to allow a slight degree of misalignment. There are many flexible coupling types. Some couplings, called disc couplings, use shim packs. There are always some limits for tolerated misalignment by flexible couplings.
When the shafts of two machines are coupled via a flexible coupling, a misalignment more than the limit between their centerlines of rotation can result in vibration and additional loads which, depending on severity, can cause problems. Modern high-quality, flexible couplings are designed to tolerate more misalignment than previous ones. When either offset or angularity exists, there will be a back-and-forth movement for each revolution. In other words, flexible elements are flexing to and from their original shapes. This action over a long time can cause fatigue or other problems in couplings. Therefore, even when a high-quality flexible coupling is used, it is still beneficial to reduce the amount of misalignment.
Case Study
For a large 3.5 megawatt (MW) vertical pump for a critical service, the alignment limit that could be achieved after 32 attempts was 64 microns. This was more than the allowable misalignment value of 50 microns that was initially specified and agreed upon. The pump was essential for the plant, so startup was delayed and a proper decision was needed to facilitate operation. The alignment was temporarily accepted pending verifications, satisfactory operation and vibration measurements.
The operation and vibration measurements were satisfactory and after one month of various operational verifications and thorough vibration measurements, the final acceptance of the misalignment value was issued to the vendor and site contractor.