Active magnetic bearing (AMB) reliability and availability levels have surpassed oil bearings after 10 years of technological advancements. These advances have made an impact on the industry, drawing attention from major original equipment manufacturers globally. In 2002, an oil and gas processing company required a bearing for a hermetically sealed integral motor compressor. The natural gas from the well contained hydrogen sulfide, which lead the company to pursue a corrosion-resistant canned bearing. Finding a reliable bearing for this hermetically sealed integral motor compressor was a challenge—but one worth the cost. The solution included sealed bearings and electrical connectors, which eliminated the need for a costly enclosure surrounding the motor compressor. Installing the motor compressor outdoors, without a building or enclosure, saved the company significantly in capital expenditures. The hermetic sealing of the bearings and motor compressor also ensured that emission limits were not exceeded for sites in which operating licenses limited hydrocarbon emissions.
Process Gas Immersion
Magnetic bearings are an effective solution for many oil and gas applications because they can be immersed in the process gas. A canned magnetic bearing with metallic lined stators segregates the electrical connections and windings from the corrosive gas. Canned bearings allow for the placement of the magnet core and windings behind an impervious pressure-rated barrier constructed of corrosion-resistant alloy or other nonmetallic material.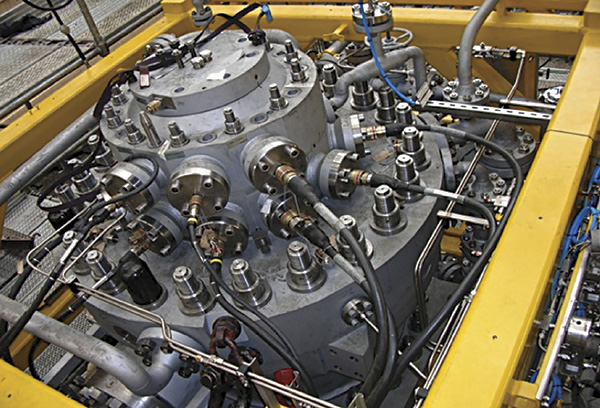
Managing Corrosion Risks
Magnetic bearings must conform to the corrosion safety standards for oil and gas applications, such as National Association of Corrosion Engineers (NACE) MR0175. The bearings’ electrical components are protected from process conditions, including chemical attack by process gas and condensates. The motor compressor can eliminate the use of dry gas seals, avoiding natural and sour gas damage to the environment. Figure 1 has been adapted from NACE MR0175. It details regions of increasing sour gas corrosion to metal alloys used in oil and gas processing equipment. Corrosion is defined by reference to sulfide stress cracking (SSC). Figure 1 shows in what levels of sour gas service sealed and canned designs may be applied while still expecting a reasonable service life, based on documented corrosion rates. The dividing line corresponds to a concentration of about 600 parts per million of sulfides.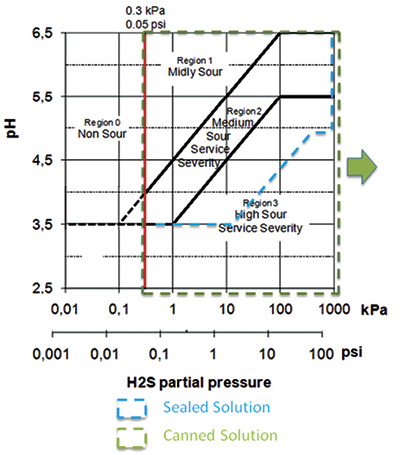