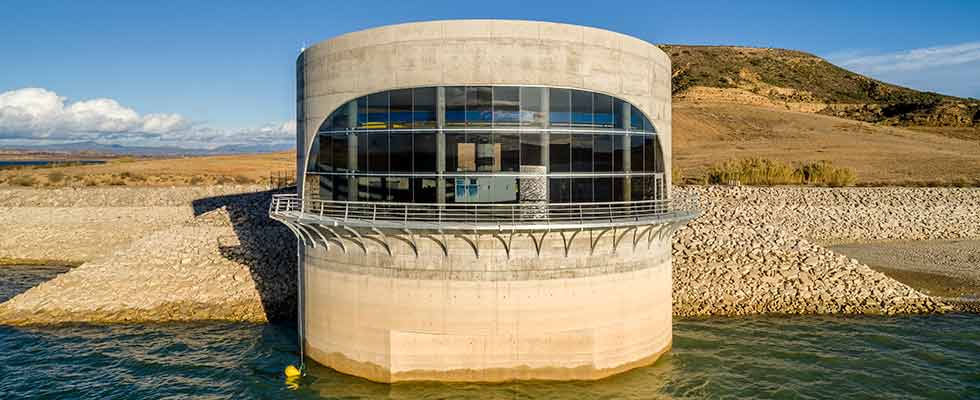
Increasing the volume of water available to an irrigation channel in Northeast Spain was necessary for local agriculture, especially during the dry summer season. The desired outcome of this expansion project was to successfully commission the reservoir of San Salvador with energy consumption kept to a minimum.
Maintaining an effective agriculture system is essential to keeping food on the supermarket shelves—and in homes—and this requires an efficient and reliable supply of water.
As the demand for this resource increases, it becomes more important to optimize the storage and delivery of freshwater supplies.
Efficiency First
From the outset, the project owners were clear that operational efficiency was the top priority to ensure that annual running costs were kept to a minimum. The owners chose an approach that would later be shown to offer between 15 and 50 percent improvement, depending on the conditions.
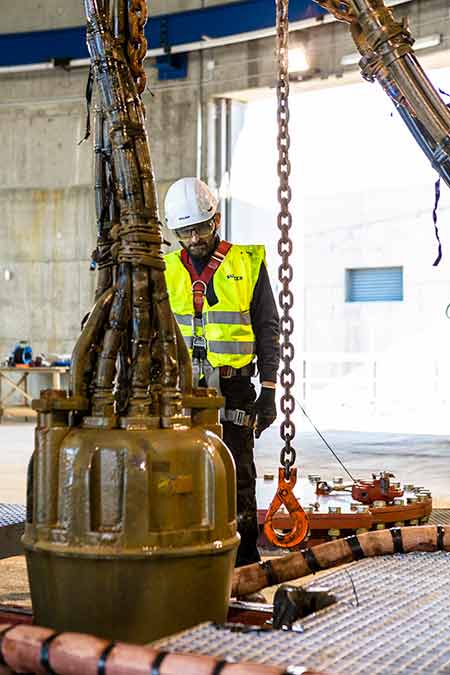
The project also delivered a partnership that included pumping solutions. So, rather than just provide pumps that could deliver the necessary water flows, a solution was selected that included the control infrastructure, as well as maintenance equipment.
The design of the final installation involved siphon-effect discharge pipework meant to improve the performance of the pumps by reducing the static head.
For this project, pumps equipped with premium efficiency IE3, PE7 motors were used as a starting point for an energy efficient installation. Variable speed drives (VSDs) and a pump controller were installed to ensure the pumps operated close to the best efficiency point (BEP) with low energy consumption.
Ground-Up Design
The owners needed a system and the infrastructure for removing and installing the pumps for maintenance. This required careful consideration to ensure safe handling of the pumps. Additionally, all of the lifting equipment and procedures had to be approved by an independent assessor.
The circular shape of the pumping station building posed many challenges for the designers, especially the lack of space for all the equipment. One solution was the installation of one pump control center to operate two sets of pumps. This proposal saved space and expense. The pumping station had to be built in two independently operated sections, allowing pump maintenance to be carried out without affecting capacity.
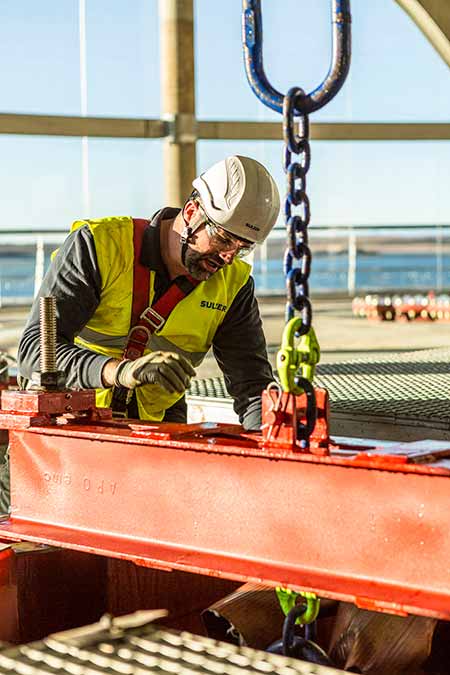
Each set of four pumps is made up of two different pump models, chosen by the engineers to offer the most efficient pumping solution for every level of water in the reservoir. The pumps are controlled by VSDs, and this combination allowed the creation of a chart that showed how different combinations and settings of the pump control system would operate depending on the water levels in the reservoir (Image 2).
Optimized Control
The pumping station is designed to maintain a sufficient water level in the distribution channel so that the irrigation system remains operational.
However, the water levels in the reservoir can change substantially, especially between the dry and rainy seasons. So, establishing the best pump arrangement and pumping regimes posed a considerable challenge to designers.
The pumps were installed over two levels and split into two independent sections. Each pump was designed with its own siphon effect system at the discharge point that can deliver energy savings over the pump’s service life.
How Efficiency Was Delivered
Three factors that play an essential role in energy optimization were considered: pump hydraulics, frequency variation and the siphon priming system.

In installations where large electric motors are operating around the clock, small improvements in efficiency can make a significant difference in energy costs.
When this is combined with optimized valve designs, the addition of the siphon effect and precision control, the overall efficiency is magnified. To ensure the level of efficiency that was desired, close technical cooperation was required. The OEM and user needed to work as a partnership to develop a more effective and efficient project.