Cryogenic products are produced globally and are critical to industries such as refining, steel, medical, plastics, chemical, petrochemical, brewing, welding and fuels. Liquid nitrogen (LN2), liquid oxygen (LOX) and liquid argon (LAR) are some of the specific liquefied gases used in these products. During cryogenic production and distribution, operating conditions can be extreme. Pumps may operate at speeds of up to 8,000 rotations per minute, operating pressures may reach 400 pounds per square inch (psi) and temperatures can be as low as -320 F (-196 C). While many users in these industries have an on-site air separation system for their cryogenic needs, others rely on cryogenic trailers to deliver products. Because pumps and mechanical seals can be affected during transfer, the transportation of these products to multiple destinations is an everyday challenge. The centrifugal pumps on cryogenic trailers start and stop often, and startup procedures are often not followed consistently. These conditions cause conventional liquid-lubricated mechanical seals to perform poorly. If the centrifugal pumps are not cooled before starting, priming will be difficult, and the seal faces will be exposed to a gas instead of a liquid. Gas is a poor lubricant and can be detrimental to the life of the seal faces. The coefficient of friction of face materials depends on the ability of the fluid to maintain a film across the faces. Because the pumps are started hundreds of times each month, the opportunity for seal failure is exacerbated.
History
For more than 40 years, trailer pump mechanical seals have been evolving to handle the challenging task of sealing cryogenic products in centrifugal pumps. Oxygen compliance makes the function of these seals even more critical. Trailer pump performance is often measured in the number of hours the pump has run before the mechanical seal is replaced. This run time is expressed as the mean time between seal failure (MTBF). A typical seal life ranges from 50 to 1,700 hours, depending on the amount of lubrication available at the seal faces.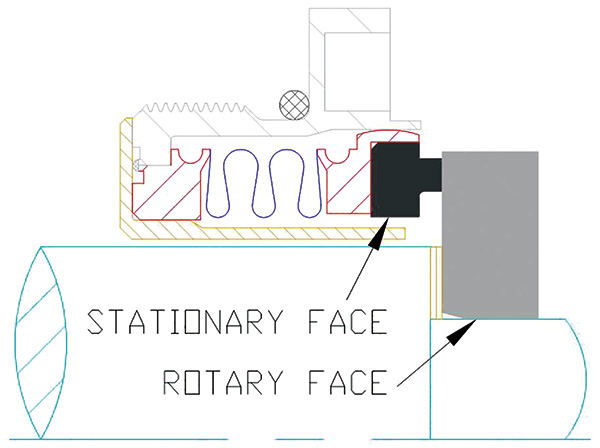
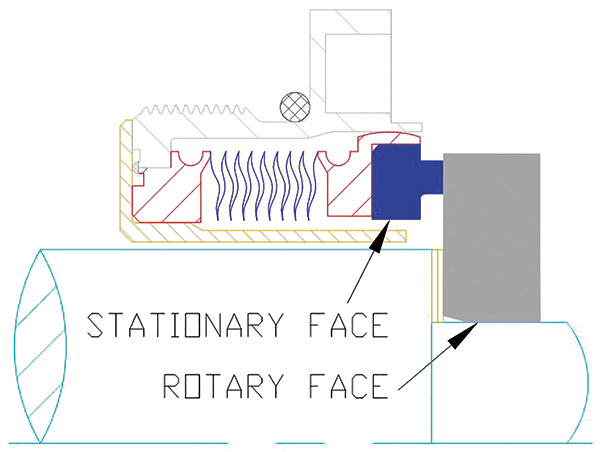
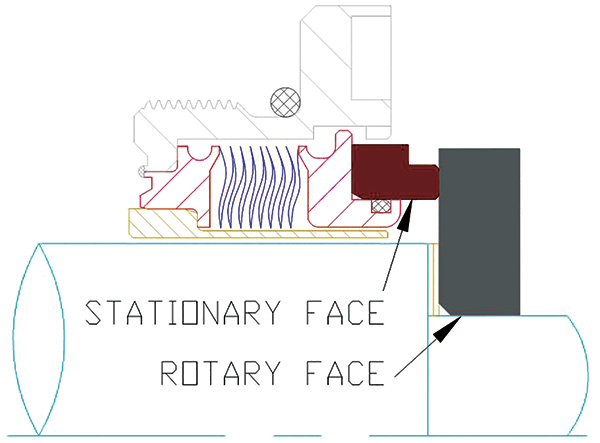
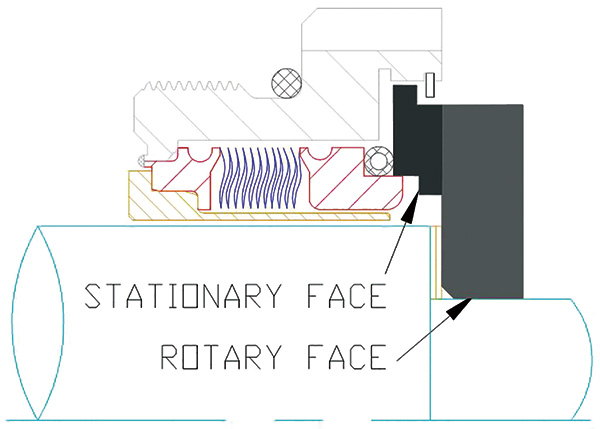
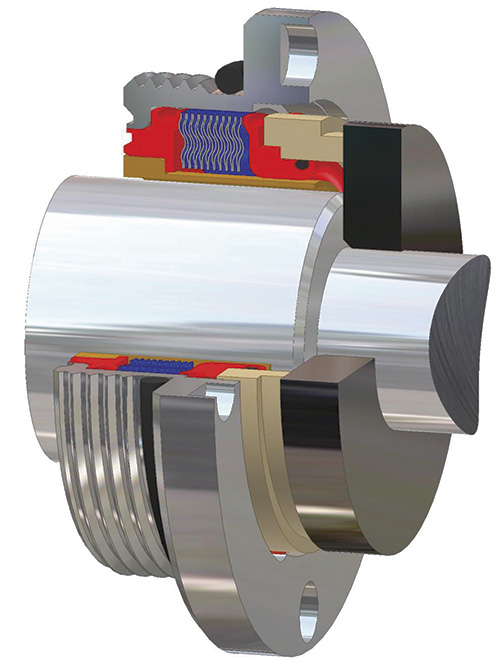