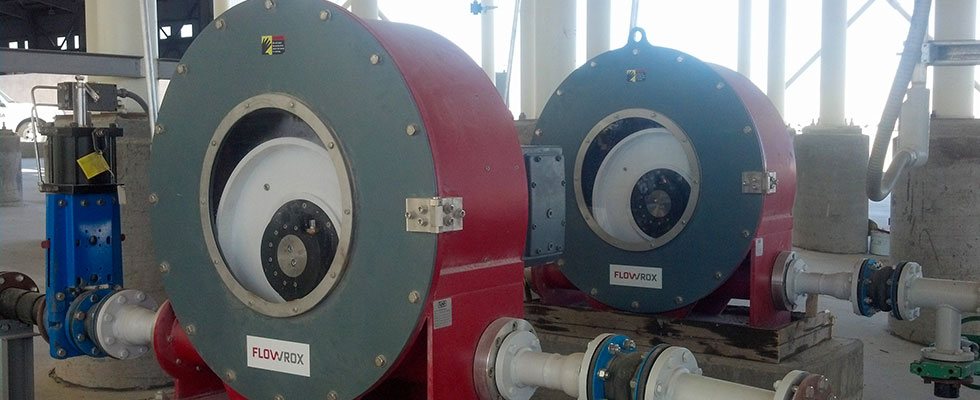
Pumping in harsh conditions can be interpreted in many different manners. The environment where the pumps are located could be corrosive, dusty, dirty or foul. Perhaps the medium is so harsh that it creates difficulties. Many pumps will not be compatible with 97% sulfuric acid because of the corrosive nature of the acid. The pump housing and components that contact the medium may need to be made of exotic alloys, polytetrafluoroethylene (PTFE) or corrosion-resistant rubber. So, corrosion issues may be considered harsh. Pumps may need to pump high solids that are harsh due to the abrasion they will create on wear parts. Some pumps are submerged, which can be a harsh environment.
This is why there are so many different types of pumps. Some pumps carve out a niche to be best in class in a specific application or industry. Finding those brands or types of best-in-class pumps is not always easy for the user. However, equipment of all types is getting better every day. Well-managed pump companies are limiting low-cost country components and still manufacturing high-quality pumps. A pump impeller from a low-cost country may be 50% less expensive than an impeller from an OEM, but the lifetime of that impeller in harsh environments may be 70% less. The age-old adage of “pay me now or pay me later” or “you get what you pay for” is alive and well.
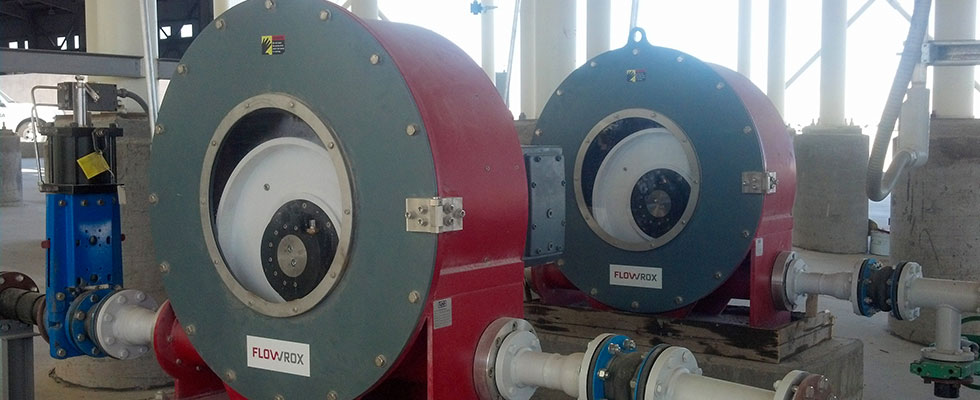
So, what are the options when the medium is extremely high solids content and extremely abrasive? Few pumps are capable of pumping 80% solids—piston pumps or peristaltic pumps are two that come to mind. Piston pumps are often used for higher pumping pressures and peristaltic pumps for lower pumping pressures. Each style has its niche. Focusing on peristaltic pumps, a typical application is thickener or clarifier underflow pumping. This niche is often inhabited by both peristaltic pumps and centrifugal pumps and, in many cases, the consumer has the option of either one. A centrifugal pump typically has a higher pumping capacity than a peristaltic pump. If the thickener or clarifier is large with a high flow rate, then a centrifugal will likely be one of the pumps of choice. When desired flow out of the thickener is 400 gallons per minute (gpm) or less, then the peristaltic pump may be the right choice. If the thickened sludge to the pump is 60% to 80% solids, then the peristaltic would be the better choice.
In many cases, a thickener is used to thicken the solids for delivery to a filtration process of some type. Pressure filters often perform best when the thickener delivers a more highly thickened slurry to the filters. Poorly controlled thickeners may result in less-than-optimal percent solids to filtration. This can result in longer filtration times, increased use of compressed air and increased energy consumption. If the cake coming off the filter is not at the desired moisture content, then thermal drying of the cake may be required. The amount of time and expense lost can be in the hundreds of thousands of dollars annually.
The thickener performance is often tied closely to how the pump performs. A centrifugal’s flow rate begins to fall as pressure begins to build within the pressure filter. Conversely, a peristaltic is a positive displacement device and flow remains constant as pressure builds. This may allow the slurry to be further packed into the filter in the pumping process. Peristaltic pumps do not have a traditional pump curve and, for this reason, are accurate even when running at low flow rates. The same amount of discharge is achieved with each revolution of the peristaltic pump. When centrifugal pumps are run at a low rotation per minute (rpm), they can fall off the pump curve and controlling the thickener can be difficult. Many centrifugal pumps also require gland seal water, which dilutes the slurry the owner thickened. Peristaltic pumps require no gland seal water.
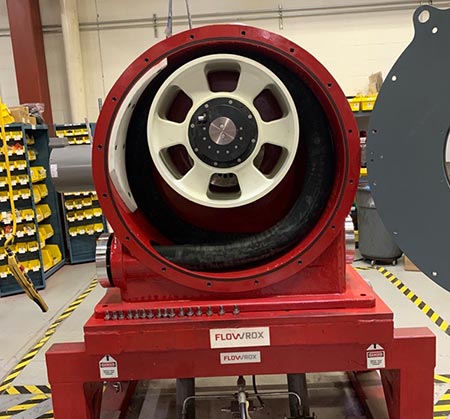
Pumping High Solids Slurries
When pumping 80% solids, there is only 20% water or other make-up liquid in the slurry. There can be benefits of pumping thicker solids. A normal centrifugal pump’s target is 35% solids, which means there is also energy invested in moving 65% water. After filtration of the example, the recovered water must be treated for reuse or disposal. If you pump 80% solids, then piping, instrumentation and infrastructure can be smaller and less costly. And in the end, it may benefit the filtration process. Pumping 80% solids may be harsh, but peristaltic pumps can handle slurries that are 35% solids or 80% solids. The rubber hose lifetime in the peristaltic pump in most cases will be approximately the same regardless of the percent solids.
Suction Lift or Run-Dry Capabilities
A peristaltic pump is capable of suction lift applications up to about 30 feet. When suction lift is 20 to 30 feet, a peristaltic pump may lose some of its pumping capacity but is still capable of delivering the pumped medium. Some of the lost pumped volume in suction lift applications can be recovered by placing a vacuum inside the pump housing. When a peristaltic pump hose is compressed, it pushes the fluid forward in the hose until the medium discharges out of the pump. When the compression device comes off the hose, the rubber hose rebounds to an oval or round shape. That rebounding action draws the medium into the pump, creating the suction lift ability. No damage will be done to a peristaltic pump if it runs dry for hours or even days.
Roller or Shoes?
Peristaltic pumps have a limited number of wear components and low cost of repair. In most peristaltic pump repairs, the most commonly replaced part is the rubber hose, which can typically be changed in a half-hour or less. A lot of designs do require glycerine inside the pump casing, but deciding between a shoe design or a single roller design can determine how much of this glycerine will be consumed annually.
In shoe designs, the rubber hose is being rubbed continuously by a pressing shoe or metal bump to compress the hose. This shoe design generates a lot of friction and heat. Typically, the main factor determining how long a peristaltic pump hose lasts before it needs replacement is how many times it is compressed. However, shoe designs often generate significant heat. Heat is the second-greatest determinant of how long the rubber hose will last. The combination of high rpm and shoes rubbing can make hose lifetime short in shoe-design peristaltic pumps.
Due to the high heat generation of shoe peristaltic pumps, they consume a large amount of glycerine. This glycerine is used to help dissipate the heat that the rubbing shoes are creating. A 4-inch (100 millimeters [mm]) shoe design can require as much as 16 gallons of glycerine in the pump housing. Glycerine costs approximately $125 per gallon. Thus, 16 gallons at $125 a gallon is $2,000 of glycerine to dispose of and replace every time the rubber hose is replaced.
A more efficient and less-costly type of peristaltic pump is a single roller design. A single roller only compresses the rubber hose once every 360-degree revolution. Shoe designs compress the rubber hose two or more times every revolution. Since the single roller design does not generate heat or friction, the hose lifetime can be two to five times longer than shoe-design peristaltic pumps.
Also, the shoe design is limited in its pump capacity. Because the rubbing shoes generate too much heat if run at a high rpm, these shoe pumps need to run at relatively low rpms. The single roller eccentric shaft design can run at roughly double the rpm of shoe pumps without generating significant heat buildup. In many cases, a one-size smaller, eccentric single roller pump can be used to perform the same work as a larger shoe-design pump. Even running at higher rpms, the eccentric single roller pump will still post longer hose lifetime and less maintenance. The user saves energy, maintenance expense and has greater uptime with an eccentric single roller-designed peristaltic pump.
Packaged Skid Systems
Pumps face harsh conditions due to how they are installed and how many of the manufacturer’s recommended auxiliaries and installation instructions are ignored. Pumps may be doomed to fail simply because of the way they are installed without required elements.
A packaged pump system or pump skid may be a way to protect a user’s pumps. The idea behind a packaged system is that the pump is installed on a spill containment skid. All of the auxiliaries and safety equipment are also housed on the skid. The skids are factory acceptance tested at the manufacturer’s site and then delivered to the user’s site. These systems are typically plug and play by connecting piping and electricity, then the system is functional. The pump is snuggled in a safe and efficient environment that protects both the pump and users.
Beneficial auxiliaries are included on packaged systems from the manufacturer. Pressure relief valves are necessary for positive displacement pumps to protect the equipment. Pulsation dampeners smooth flow and eliminate piping hammer and increase tube life in peristaltic pumps. Pressure relief valves also eliminate the possibility of over-pressurization of the system and protect the pump, piping and instrumentation.
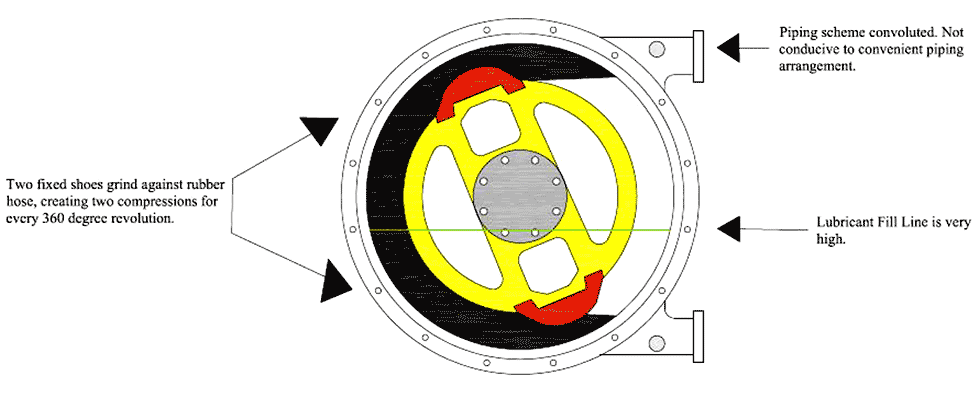
IIoT-Enabled Pumping Technologies
Pump digitalization and monitoring of critical dynamic machines can help achieve savings. There are numerous platforms and instrumentation to choose from to perform pump monitoring. Some newer pumps are enabled with industrial internet of things (IIoT) technologies upon delivery. These pumps can be monitored from any smart device or computer anytime and anywhere where there is an internet connection. This connectivity brings advanced insight by users and early warning alarms when components are starting to fatigue. A digitalized pump is capable of sending warnings that bearings are failing months before downtime or disruption occurs. In pump intensive operations, the savings can be in the millions annually.
Pumping 80% solids or pumping 97% sulfuric are examples of harsh pumping conditions. But there are many other variables that lead to harsh conditions. The external environment and pumped medium characteristics are all factors in pump reliability and survivability. A seemingly similar pump application can have hidden obstacles that are not known until the pump actuation starts up.
Hose lifetime has been one of the main complaints from users regarding peristaltic pumps, but eccentric rolling design peristaltic pumps increase hose life compared to shoe or multiple roller peristaltic pumps.