When a pump needs to be pulled from service, the maintenance manager often needs to make the decision to either have the pump rebuilt or to replace the pump entirely. Money is often the biggest motivator when it comes to making that choice. Maintenance dollars only go so far, and when older pumps are involved, the cost to rebuild can be higher due to the difficulty of sourcing some of those replacement parts. When one chemical manufacturer pulled their sump pump, they made the decision to replace rather than rebuild. Chemtrade Logistics Inc. provides several types of chemicals to industrial companies around the globe. One of their production facilities in Virginia manufactures alum. Alum, which is also known as aluminum sulphate, is used for wastewater treatment, pulp and paper, and industrial processing applications. The chemical manufacturing plant worked with their service provider to select a pump that would allow them to reduce maintenance costs and improve pump reliability.
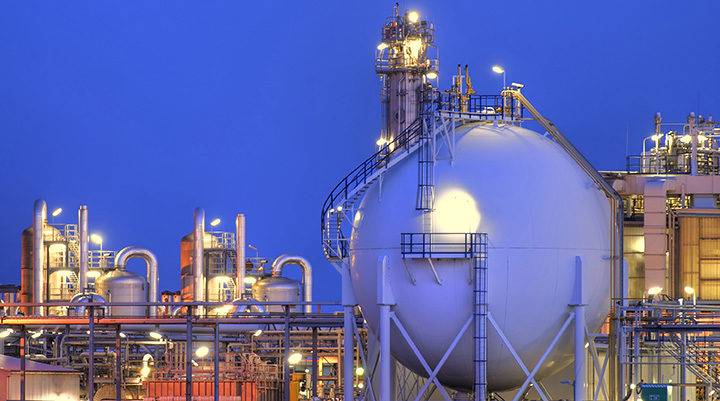
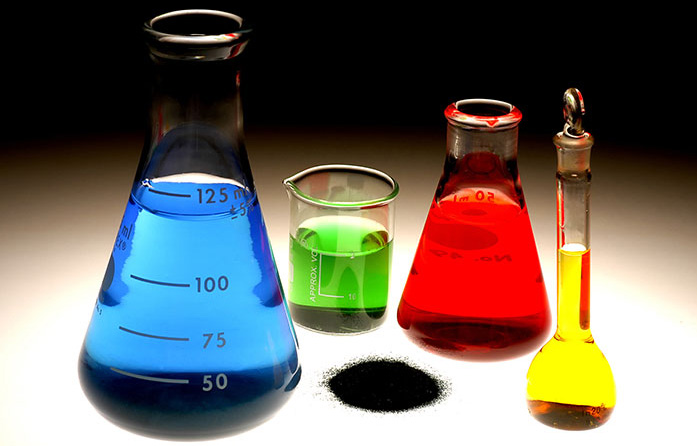
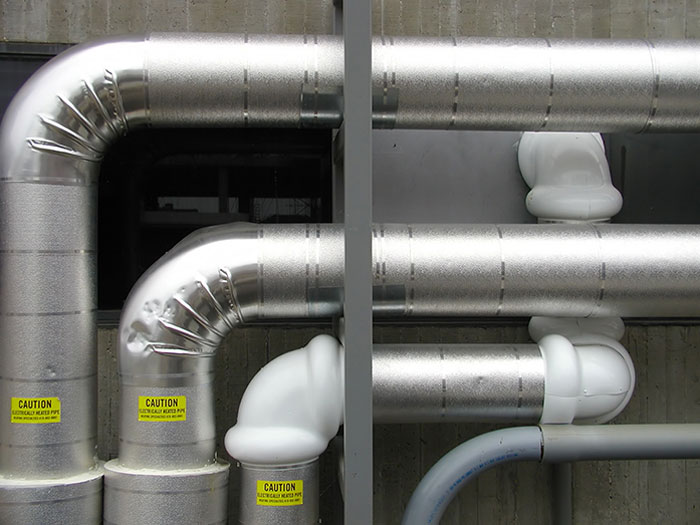
Chrome Iron Agitator to Suspend Solids
Made from abrasive resistant 28 percent chrome iron, the agitator in the pump makes it an ideal solution for handling the bauxite slurry. The bauxite is comprised of a mixture of aluminum hydroxides, clay minerals and other insoluble materials, so it was critical to have the high-chrome agitator suspend the solids in the slurry and allow the pump to transport the slurry to the recovery process.Chrome Iron Semi-Open Impeller to Pass Particulate
The pump is engineered with a semi-open impeller and has been proven to handle slurries with solids concentrations as high as 70 percent by weight.Chrome Iron Wear Plate to Resist Erosion
The pump included a replaceable 28 percent chrome iron wear plate, which makes it erosion-resistant. Erosion on the suction side can reduce pump performance, so the hard iron replaceable wear plate helps to increase overall pump life.Durable Construction for Industrial Applications
The pump includes a stainless steel shaft and shaft sleeve, which reduces shaft wear from abrasive slurries. The pump volutes are cast from hardened ductile iron, which—at 300 Brinnell hardness—are twice as resistant to abrasives as standard ductile iron. The hardened ductile iron volutes are cast with extra thick walls at the point where the pumped slurry enters the discharge.Motor Protection for Reliable Operation
The pump is protected by double silicon carbide mechanical seals that are housed in a separate oil-filled seal chamber, and the heavy duty lip seal offers additional protection for the mechanical seals. The motor is further protected with Class H motor insulation, built-in amperage (FLA) and temperature overload protection.Slim, Top Discharge Design
With a slim, top discharge design, the pump is cooled by the pumped liquid and can pump a sump pit down to within inches of the bottom. A side discharge pump without a cooling jacket must stay submerged to avoid overheating, leaving as much as 3 feet of un-pumped slurry. The pump would be perfect for the 4-foot deep central drainage sump.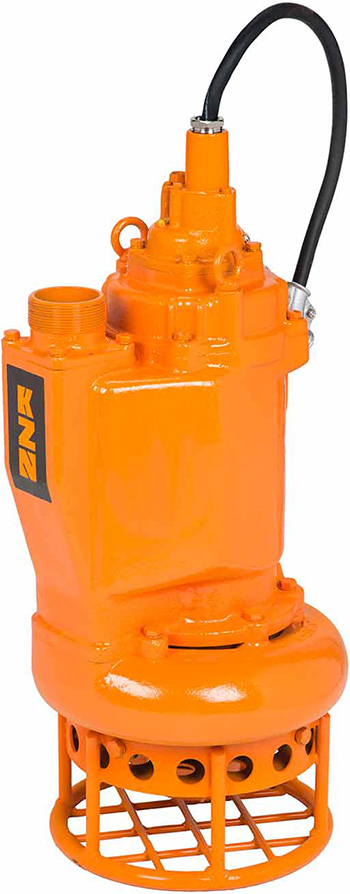