Learn about the advantages and disadvantages of different pumps used for stationary fire protection.
Steven Brown & Associates
05/23/2019
Typical buyers of fire pumps are interested primarily in the hydraulic performance of the pump in question—specifically the gallons per minute (gpm) and the pressure boost (pounds per square inch [psi]) of the pump. If a pump can be found to deliver a specific gpm and psi, and it is listed by a trusted third-party agency, then the evaluation often ends there. Rarely is the type of fire pump considered. This article focuses on centrifugal fire pumps that carry either an Underwriters Laboratories (UL) or FM Global label, and are used specifically for stationary fire protection.
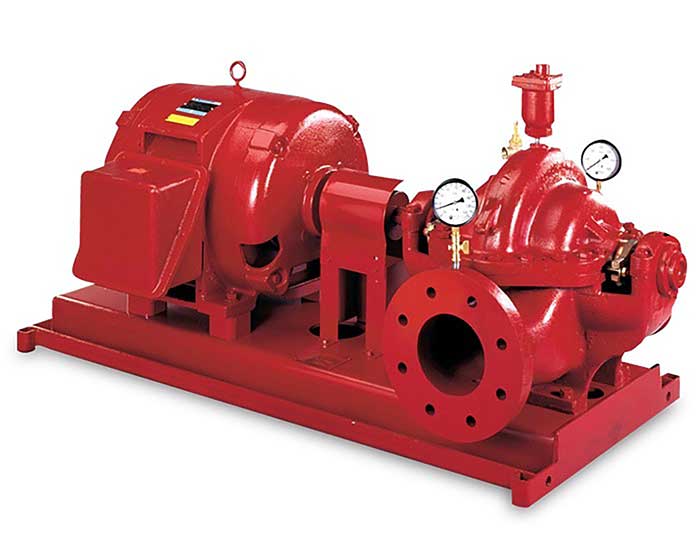