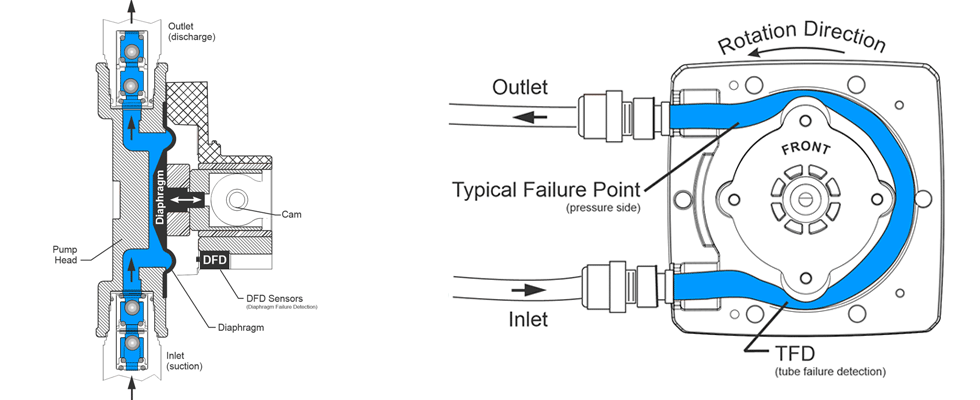
When treating water or wastewater, two types of chemical metering/dosing pumps are often considered: diaphragm and peristaltic.
Requirements that must be met begin with chemical feed. Whichever style of unit is chosen, it must be able to measure and dose precise amounts of chemical to meet, but not exceed, the chemical demand of the particular application.
The biggest question is: what type of pump? This article will discuss the benefits and challenges of two styles—diaphragm metering pumps and peristaltic pumps. Which is best suited to meet the demands of the application? Which of these is most cost-effective and reliable? Which requires the least regular maintenance?
Both types are positive displacement pumps, but they work in different ways. Diaphragm pumps have a pumping cycle that consists of a suction and discharge phase. This intermittent pumping of chemicals, specifically during the suction phase of the cycle, can cause gas buildup in the pump head. This buildup of gases can result in vapor lock (i.e., loss of prime).
Diaphragm pumps have check valves at both the suction and discharge ends of the pump head. If either set of check valves becomes fouled, the pump will not meter chemical accurately or may stop pumping altogether and a loss of prime may occur.
Diaphragm pumps can also create shear stress on fluids, particularly if the pump employs a high velocity stroke action. Fluids containing particulates and gas forming chemicals can foul heads and valves. To try and avoid these issues, routine maintenance procedures must be performed. So, although initially the diaphragm pump may appear to be the more cost-effective choice, it does have its challenges.
Particular attention must be paid to the regular cleaning of check valves and to the routine inspection of diaphragms. With peristaltic pumps, the fluid is pumped through a flexible tube. Roller assemblies are attached to a rotor, which is controlled by a motor. As the rotor turns, the rollers pinch the tubing to force the fluid through. When the tube is not compressed, the fluid flow is brought into the tube.
This gentle squeezing action of the tube and valve-less design of a peristaltic pump head design results in near continuous injection of chemical.
If there is a drawback, it is in the wear to the pump tube caused by this continuous action. Pump tubes require routine changing at regular intervals throughout the pump’s life span.
A positive is that peristaltic metering pumps excel at pumping fluids that contain particulate matter into lower pressure systems because there are no valves to clog. In addition, the gentle forces created during the peristaltic pumping action will not damage delicate fluids within the tube.
Peristaltic pumps are also effective when pumping gas forming fluids, such as sodium hypochlorite; whereas diaphragm pumps tend to lose their prime and fail when gases build up in the pump head, and the gas is simply “pumped through” the peristaltic tube.
It is important for a user to find the right type of pump for the application. Calling on a manufacturer that offers both diaphragm and peristaltic types of pumping units will help users reach a nonbiased decision and ensure the best pump for the job.