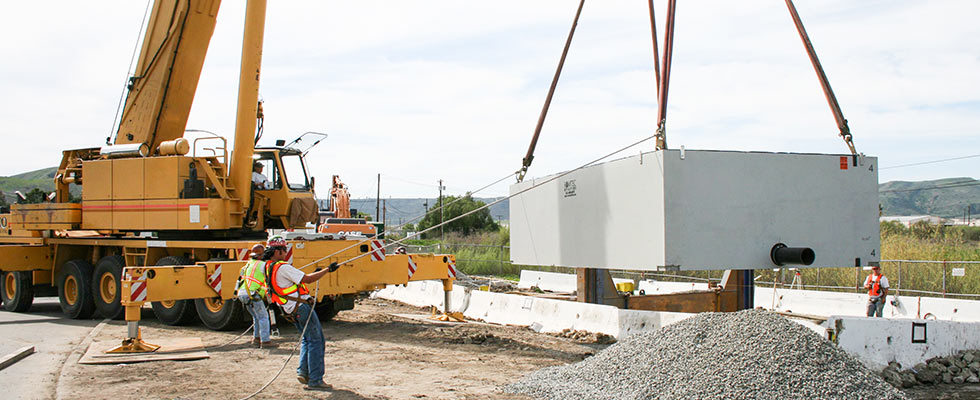
The oil and gas industry has been a leader in collecting and treating stormwater on-site for many years. The circumstances vary from site-to-site, but the requirements remain relatively constant: collect all rainwater runoff, move it to and through treatment and sampling and discharge it to a body of water or back to the earth.
Most notable is the rapid pace of the switch to electronically commutated motors (ECMs), commonly referred to as brushless direct current (BLDC) or brushless permanent magnet (BPM) motors. These motors share many common features.
In most on-site water treatments, the task is typically to filter out the solids and to separate the hydrocarbons from the water. There are many methodologies that are available and will be effective. This article will focus on the collection and conveyance of water to and from treatment.
Stormwater is one of the principal sources of water pollution. Imagine 90 to 100 days without rain in the Los Angeles basin and then a major downpour. The water content heading to the bay, river or lake is then loaded with various solids and liquids that could be separated from the water prior to their discharge. The objective is typically to collect it all and to treat it. The following are four different oil and gas sites and the process they used to collect, convey, treat and discharge stormwater.
Major Gulf States Refinery
This project involved a large site with an existing sheet pile sump that was approximately 80 feet long, 20 feet wide and 20 feet deep. The existing sump was failing, and the pumping configuration was not able to handle the inflows which ranged from 100 gallons per minute (gpm) to 60,000 gpm.
Requirements
The requirements included the design of a new enclosed sump that would fit inside the existing sheet pile sump. The sump would include a series of chambers that would both collect solids and house multiple pumps called to operate as the volume of water grew greater and called to slow down and to ultimately stop as the water flow decreased.
The pumping system would be configured to a series of existing piping that was connected to six different large, abovegrade holding tanks. These tanks would then gravity-flow the water to and through treatment.
NOTE: The six aboveground storage tanks each had level control and that data was sent to the intake pumping systems control panel. The pumping system could then determine which tanks had capacity and open the appropriate valves and pump the water to those tanks which had available storage space.
The Major Problem
The downtime the refinery allowed between decommissioning of the existing sheet pile sump to the commissioning of the new concrete sump was short. The refinery wanted it done in weeks, not months. Fortunately, there was a precaster reasonably close by who had 10x20 feet rectangular concrete. Using their standard flat base, top slab and rectangular risers, the three 10x20x20 feet rectangular sump sections were precast, precored and most of the in-sump mechanical was preinstalled.
How are three 10x20x20 feet rectangular sumps turned into one big sump? In this case, each of the three sumps included a precast 10x20x9 feet riser that was the first precast section coming up off the precast base slab. That riser section was cast with two 36-inch knock-out sections on each of the 10-foot ends. These knock outs were all located near the bottom of the sump. They were cut out to allow four 24-inch pipe sections to interconnect the three rectangular sections of the overall 60x10x20 feet new concrete sump.
Advantages
There were multiple advantages to connecting the three sump sections together with the 24-inch pipe to form the total sump. The first benefit was that it allowed the water level to float equally between all three sections.
Next, it allowed for the configuration of a weir wall in the first section which created an area that both collected solids and which also reduced turbulence between the first section on one side of the well wall and all the rest of the space in the overall sump.
NOTE: When designing a pumping system for a high discharge pumping rate, it will inevitability have a high rate of inflow. Pumps, level control and just about everything in the sump does not do well with turbulent flow and the associated air entrainment.
The third benefit is the ability to ship and handle them with a crane of moderate size.
NOTE: This was a rebuild within an existing sump and in and around an existing (and operating) refinery. There was not a lot of extra space to work in.
The fourth benefit was the ability to prefabricate all the overall system mechanical including all three top slabs and their related hatches, vents and other equipment.
NOTE: This new sump and all related in sump mechanical was installed and interconnected in one week. The buildout from the various penetrations into the existing pipe racks took another two weeks.
The new power control and supervisory control and data acquisition (SCADA) panel from the new sump was installed, tested and connected to the tank level signals at each of the six above grade storage tanks in the next two weeks.
Pumps & Their Configuration
When moving a lot of water against significant total dynamic head (TDH), there is nothing that works as well as line shaft turbine pumps. However, turbine pumps cannot handle solids of any significant size. When reviewing the system design, it was noticeable the first sump section before the well wall used submersible wastewater-type pumps.
The first pump
The first pump is intended to handle low flow which occurs during most of the year. This type of pump is capable of handling solids up to 3 inches and the bar screen set up prohibits trash (anything above 4 inches in diameter). It stops all the big stuff before it gets to the first section of the sump. In short, the wastewater solid handling pump is often the only pump that will operate.
The weir wall
As the inflow grows and ultimately overwhelms the pumping capacity of the first pump, it also rises to a level that allows the water to go over the weir wall. Once the level in the overall sump rises to the start level of the second and third pumps, they then start, and then along with the first (low flow) pump, continue to operate.
The middle section of the sump
This section again houses submersible pumps. They are reliable, and if the water is still too dirty for the turbines, they will do the job. This section also has two line-shaft turbines. With all pumps running in the first and second sections, the sump system will be discharging about 30,000 gpm.
The third section
Here, there are three more turbine pumps. By the time these pumps turn on, there is a big event going on and the entire system will be producing about 60,000 gpm. Turbines are reliable if the water and the power are clean. In this precast sump, there are some advantages.
A. The top slab is precast and is nice and flat. Turbine pumps need to be vertical and plumb. When they ramp up, they do so fast, and any misalignments can cause wear and vibrational problems.
B. The pumps could be installed in a precise location to connect with existing site piping without having to make major modifications to the piping.
Like any pumping system that collects stormwater to be pumped to treatment, prescreening is essential. There is also going to be regular clean out required in the first stage of trash collection and on the trash side of the weir wall.
NOTE: Raw stormwater pumping systems always require some level of ongoing clean out in the trash catching portion of the system.
Control & Communication
Like most major industries, oil and gas, and in this case a refinery, has lots of existing control preferences and a defined SCADA system that must be adhered to.
This project reflects a true system in that a single entity was responsible for the design, supply, construction oversight, startup testing and training of all structural, mechanical, electrical, control and communications in the pumping system. This breadth of scope is unusual, but when available, it is a step in the right direction.
Quality Level Control
The primary system consists of a radar level transmitter mounted to each basin. The transmitters were located such that there would be no interference with the installed mechanical equipment.
Each transmitter would relay the level signals in that basin to control the pumps within that basin. The secondary system consists of mechanical float level switches in a secure float tree configuration which allow for backup alarming. The level instruments are connected through a watertight traffic-rated junction box to the control panel.
This refinery rebuilt and updated their ability to collect, pump, store and convey to treatment flow levels ranging from zero to 60,000 gpm. It used a systems approach to this rebuild which ultimately gave them better, longer-lasting concrete sump, with better trash collection, as well as better low, medium and high flow pumping capability.The refinery was able to control the pumping to six different above grade tanks which then conveyed the untreated water to treatment primarily by gravity.
The trend is toward more and better stormwater treatment. This Gulf Coast refinery can rest easy knowing every drop of water that falls on their property is being collected and treated prior to discharge.