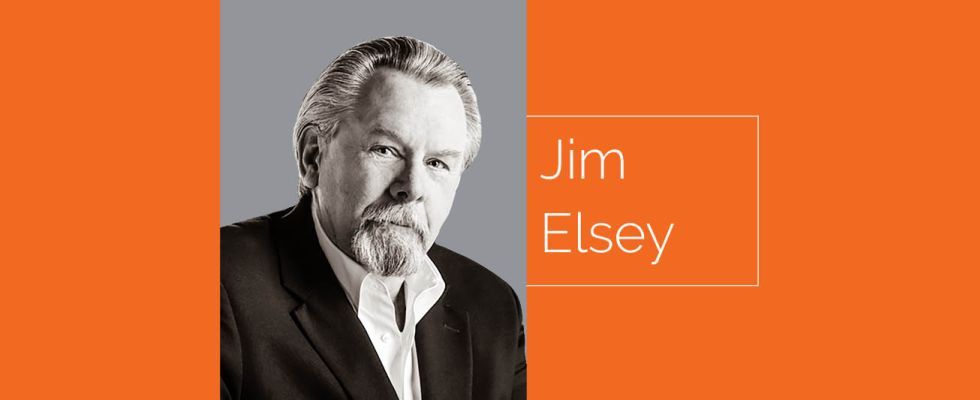
Walking the System
The intent of my last column was to provide an introductory level to the subject of system curves. A sort of primer, because you have to learn to walk before you can run.
In the previous column, I mentioned the expression “walking the system” as a method to define the curve and/or its accuracy by conducting due diligence for the system resistance curve. I didn’t have space to include the explanation in the previous issue; therefore, I am offering the information as a short column this month.
Be Prepared
When I am called to troubleshoot system problems, the user/owner typically does not have a system curve, so I come equipped at a minimum with a clipboard, paper, pencil, a flashlight, a rag, a 25-foot tape measure and a hydraulic data book. If facility rules allow, I will also bring a camera and a handheld infrared temperature detector. Tip: If you use an ink pen, use waterproof ink. Proper and appropriate personal protective equipment (PPE) is assumed.
Starting at the pump, I walk every foot (meter) of the system from beginning to end and write down measurements and locations for all pertinent components in the system. Another way of explaining this procedure is that I inspect and record the system “hand over hand.” I note the length and diameter of the pipe and all transitions. I record the number and type of valves. I note any variations in elevation because that is also critical. Note that most multifloored plants have elevations marked on the stanchions. I also count the number and type of pipe elbows (45 or 90 degrees) and note the radius (short or long) and don’t forget tees and wyes. Furthermore, I record any components such as heat exchangers, reactors, tanks and strainers/filters. It is important to note the manufacturer and model to facilitate garnering the valve flow coefficient (Cv) and K-factor information from their website or directly from their engineering department. Moreover, I also log any instrumentation, sampling taps and/or drains. At the conclusion of the process, you should have a workable one-line diagram of the system.
Discovery
During the due diligence process (with permission and perhaps an operator), I also check each valve position and operational state of the equipment. In industry, this process is known simply as a system/valve lineup. More than once, I have found manual valves in the wrong position, automatic control valves (pneumatic and electric) that were not operating or programmed properly and empty tanks that should be full or vice versa. For example, one rising stem gate valve had the stem in the correct position, but the actual valve gate had become detached. So, while the valve indicated it was open, it was actually closed. I have also found pump drivers operating at the wrong speed and even in the wrong direction. Often, the system is not constructed to the print or unauthorized changes have been made. Too often, there is no print or drawing of the system. On one system, I detected a previously unknown and improper pipe diameter change. Under the lagging (insulation), a 6-inch pipe had a 15-foot section of 4-inch pipe installed. At one remote site, the electric power was supplied by a large diesel generator where I found the frequency switch in the 50-cycle position for a 60-cycle system. Finally, at a large, automated reverse osmosis plant for making fresh water from seawater, I found the computer program was allowing each pump to “run out” too far to the right on the performance curve before the next pump in parallel was started. This discovery explained why the pumps were cavitating.
Not for the Weak
Why do you need the rag, you ask? Unless it is a nuclear, pharmaceutical or food grade system, the nameplates for the components will be covered with dirt, oil and grease. The process of walking the system is often hot, noisy, wet, tedious, foul smelling and just plain nasty, but after all my years in the field, I have found it is the best way to ascertain what is really and truly going on in the system.
Stories
Here are just a few anecdotes from my walkabout experiences. Once on a job in Wyoming, the units for the total length of piping was in miles. I successfully used the odometer (trip meter) on my rental car as a measuring device. We found the system design calculations on the length of pipe were off when compared to the actual build. At several different pulp-paper mills, I found that the main line piping for the principal cooling system had been “tapped” (unauthorized) at several places for additional components with ostensible disregard for the original design needs of the main system. More than once, I have found self-primer pumps in applications requiring more than 34 feet of lift or with small holes in the suction line. You should already know why 34 feet is an issue and that on a lift situation the water does not leak out of the hole, but the surrounding air does leak in.
The pump will operate where its performance curve intersects the system resistance curve if it can operate at that juncture. The pump performance curve is equipment dependent, but the system curve is equipment independent.
I walk the system because bathed in the bright light of the due diligence process is where you will find the truth. Or simply stated in the spirit of Kaizen, Six Sigma and W. Edwards Deming, “go to Gemba.”