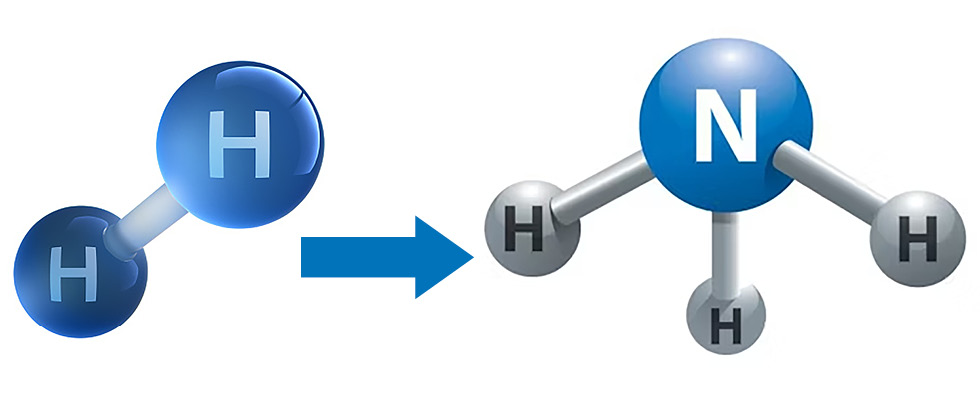
Ammonia (NH3) is a chemical that has revolutionized the world in multiple ways. Its use as a fertilizer has enabled the agricultural industry to match the food demand of our growing population for a century. Its thermal properties and lack of ozone-depleting characteristics allowed us to replace environmentally harmful refrigerants like chlorofluorocarbons (CFC) and hydrochlorofluorocarbons (HCFC). It now promises to change the world again—by transforming the world of fuel.
As the global trend to reduce carbon emissions and displace the use of fossil fuels advances, hydrogen has taken center stage as the primary alternative. Unfortunately, hydrogen (which exists as a gas at atmospheric pressure) can only be transported over long distances in a liquid state, which is only attainable at the extreme temperature of -253 C at atmospheric pressure. This, as one can imagine, creates a high technical barrier for use. Is there a solution? Enter ammonia.
Ammonia’s Role in the Energy Transition
Ammonia is a highly effective hydrogen carrier, as it is comprised of three hydrogens and one nitrogen atom. It has a high ignition temperature and can be easily liquefied (-33 C at atmospheric pressure), making it perfect for high volume transport. By combining with nitrogen to create ammonia, hydrogen can now be shipped to end users in large quantities and with high efficiency, allowing the access to and use of hydrogen fuel to scale much more rapidly. This longstanding barrier to the growth of hydrogen fuel now has a solution.
Problem solved, right? Not so fast. While promising, the ammonia carrier solution does not come without its challenges. Its unique chemical properties pose challenges to the pumps required to move the fluid. Said properties include a low net positive suction head available (NPSHa), low viscosity, poor lubricity, low boiling point and high vapor pressure—all of which drive complexity in the pumping process (material selection, design considerations, reduced efficiency, etc.). If that was not enough, ammonia is a toxic chemical that is especially hazardous in a gaseous state. If ammonia were to leak beyond its pressure barrier (the pumps and piping containing the fluid) and be exposed to atmosphere, it would vaporize and pose a health risk to anyone in the nearby environment. Typical sealed pumps—a pump with a mechanical seal between the rotor shaft and atmosphere—are a poor choice for this application, as even minor mechanical seal issues will result in off-gassing ammonia to the local atmosphere. The question is then raised: Is there a pumping solution that can handle the complex chemical properties while mitigating the risk of a leak? The answer lies in sealless pumps.
Sealless Pump Solutions
Due to the many difficulties with pumping ammonia, end users are looking to sealless pump solutions for many ammonia applications. Sealless pumps allow for higher system pressurization of ammonia, which can reduce vaporization and overall cooling requirements without the dangers of leakage. A sealless pump uses a static containment shell rather than a mechanical seal to contain the fluid in the pump boundary. For centrifugal pumps, sealless options are canned motor pumps and magnetic drive pumps. Both have advantages and disadvantages, so how does one decide what is the best option?
Mag drive pumps offer a sealless design, multiple hydraulic configurations and a more familiar pump with an externally coupled motor design. Canned motor pumps offer a more compact design with the impeller and rotor sharing a common shaft, standard dual containment, multiple hydraulic configurations and only two replaceable bearings. In Image 1, you can see the physical differences between the two sealless options. On the canned motor pump, the dual containment is highlighted in orange and red. If the primary shell or can (orange) is breached, the fluid is contained safely within the motor casing (red) for an unlimited period of time.
A Sealless Solution
Many engineers have turned to canned motor pumps for their compact design, true dual containment and the limited spare parts requirements. Often, canned motor pumps can be designed specifically to match difficult applications, and their circulation plans can mitigate vaporization issues with vertical, self-venting plans (American Petroleum Institute [API] 685 Plan 13-SE). The additional benefit to this type of circulation plan is that the motor adds less heat to the ammonia, which reduces the likelihood of vaporization.
Canned motor pumps can also be configured with innovative hydraulic solutions to provide a plant with a reliable sealless solution. A few examples of this are large multistage pumps for high head and low flow applications, submerged in tank canned motor pumps and vertical in-line pumps that provide NPSH required (NPSHr) with the pump suction submerged in a barrel (similar to an API VS6 pump). When evaluating new and existing ammonia applications, it is important to know that canned motor pumps can be used in a wide range of difficult applications.
Application Considerations
When deciding to go with a canned motor pump for a pump application, it is critical to consider and provide the aspects of the fluid, pumping characteristics, system properties and any other important considerations. Some of these characteristics to consider for ammonia are the temperature, system pressure and NPSHa. As discussed throughout this article, ammonia is a great medium for transporting hydrogen but comes with specific challenges that can be mitigated with canned motor pumps.
As the world transitions away from hydrocarbons as our primary energy source, ammonia has become a transition fuel to carry one of the primary clean energy sources: hydrogen. In parallel, the world is looking to limit chemical emissions overall, and sealless pumps can play a part in achieving this goal. For ammonia applications in current plants and the next generation of clean fuel production and transportation, canned motor pumps are the answer.