Pump system performance testing can be used in conjunction with a decision support system to provide real-time instructions guiding users to the minimum possible operational cost for a pumping system—much like a SAT NAV system does for car drivers. In the water industry, one of the primary ways for a water company to maintain profit is to reduce the unit cost of delivery (i.e., increase efficiency). Improvements in technology have the potential to greatly assist with this, with measurement leading to informed decision. As Lord Kelvin (1880) said, “If you can’t measure it, you can’t improve it.” Pumping consumes the greatest quantity of electrical energy in water company operations by far. Indeed, pumping often forms at least 20 percent of process operations, making the knowledge of pump performance a key metric in many industrial processes. The fingerprint of a pump’s performance consists of total differential head, electrical (or mechanical) power, hydraulic efficiency and volumetric flow rate. Therefore, step one of pump system testing is to be able to effectively measure these key parameters, with the aim of reducing pump operating costs to a minimum.
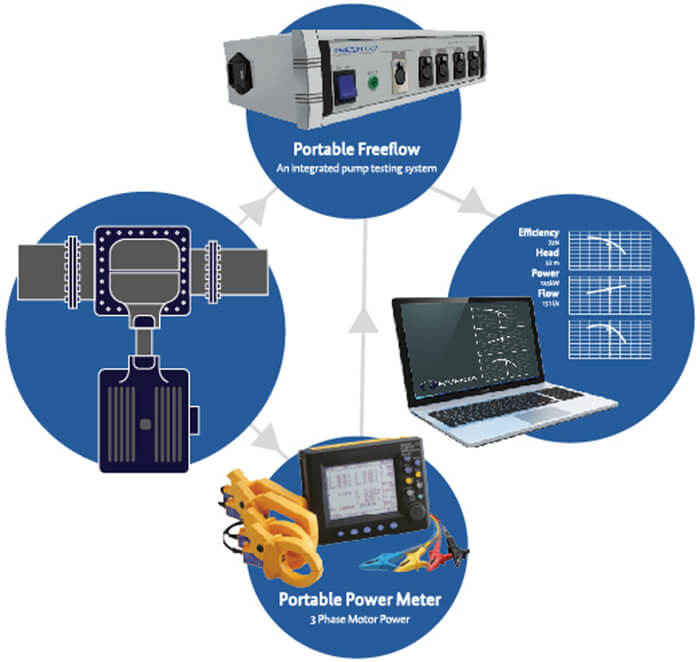
Methods of Pump Performance Measurement
There are numerous ways to measure pump performance under different circumstances and with many types of equipment. However, when considering system testing, it is worth knowing that the methods, and therefore the equipment that would be used, can be broadly grouped into two categories: conventional and thermodynamic.Conventional Method (Pressure-Flow Rate)
This method computes the output power of the pump through measurements of differential pressure across, and volumetric flow rate through, the pump. The input power to the pump is usually obtained by measurement of gross electrical power and an assumption of motor efficiency. Features of the conventional method:- resilient for all head ranges from zero upwards
- requires the measurement of flow rate—therefore, suitable and accurate for a test loop
- mostly unsuitable for site use due to absence of straight pipe in the individual pump main
- prone to error in pump efficiency computation due to any errors in flow rate measurement or motor efficiency estimation
- simple mathematics for beginners
Thermodynamic Method (Enthalpy-Entropy)
First documented by a French scientist in 1912, and at that time named the thermometric technique, the thermodynamic method uses enthalpy-entropy mapping to determine pump efficiency without the need for flow-rate measurement. The premise is rooted in fundamental thermodynamics in that if you measure any two thermodynamic state variables (TSV) that include temperature and pressure, then you can calculate any other TSV, including enthalpy and entropy. Using the equations shown below, the fingerprint of a pump can be established, and the pump measurements calculated using the thermodynamic method. Features of the thermodynamic method:- half-inch tapping on each side of the pump to measure pump efficiency
- does not require the straight lengths of the pipe as with the conventional method
- excellent for in-situ, on-site pump performance testing and monitoring
- superior accuracy at higher heads
- purchase cost is lower and irrespective of pump size, with installation cost also low
- poor accuracy at low heads 10 meters
- requires accurate difference thermometer sets 0.001 C
Choosing the Best Method for Your System
The outcomes are the same for each method— measurement of head, power, efficiency and flow rate—each is suited to different applications, as shown in this comparison. Conventional method:- is costly to implement, on-site, requiring a flow meter on every pump
- usually cannot include a flow meter on each pump due to physical space constraints, which also limits the accuracy of application
- is well suited to test loops but not for site use
- has no upper or lower head limitations
- is comparatively low cost for a site use purchase
- has simple installation requirements and, as such, is low cost to install
- is not dependent on straight lengths of pipe to determine an accurate measurement
- is well suited to on-site application, generally for heads greater than 15 meters
- has head limitations to obtain the best accuracy

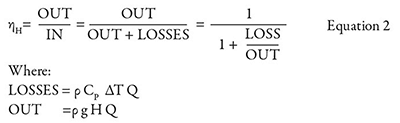
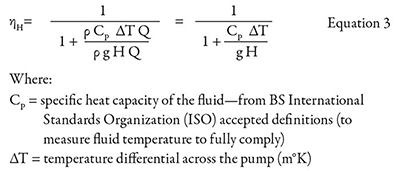
