For the last decade or more, globalization has driven tremendous changes in the worldwide marketplace, forcing industrial companies to adapt to an ever more competitive landscape both at home and in export markets. These competitive pressures have driven innovation and cost savings in all aspects of plant operations from the simplest process to the most complex system. Historically, maintenance, repair and operations (MRO) departments and their budgets have been under constant stress to become more efficient. With the intense pressure and rapid changes caused by globalization, these operations have had to accelerate the review of all aspects of their management, systems and processes to obtain gains in efficiencies and associated cost reductions. Using a continuous incremental improvement approach combined with new, innovative technologies, MRO organizations can identify and implement simple changes that can save time and money. One such area for a new, simple change in approach is the purchase and usage of mechanical packings. While often not viewed as a significant cost driver, inefficient usage of mechanical packing can result in substantial unnecessary costs and wasted time. Since it is generally viewed and treated as a commodity, mechanical packing has not received much attention with regard to efficiency improvements. But with some innovative changes to the storage, handling and cutting of packing, users can find substantial savings. One company reviewed the process of packing in-situ equipment in plants and found certain time consuming, inefficient processes that can be eliminated. Maintenance mechanics usually have to find the appropriate packing, cut it to size in the maintenance workshop (a controlled environment with the proper equipment) and then bring the cut packing rings to the equipment to be serviced, which can be a significant distance and journey time if the plant is large. If on arrival to the equipment there are any issues with the cut packing rings that prevent their proper installation and performance—such as wrong length or too few rings—a return trip to the maintenance workshop is required. That trip consumes valuable maintenance man hours. One way to avoid this possible waste of time is for the mechanic to carry the packing to the equipment and cut the required rings in the field. This is generally a more efficient means of accomplishing the task. But it is rarely done because the mechanic has to carry all of the appropriate measuring and sharp cutting tools to the equipment and perform the operation in much less than ideal conditions. With a new packing system, the more efficient process of cutting packing rings in the field near the equipment can be accomplished quickly, accurately and, most important, safely.
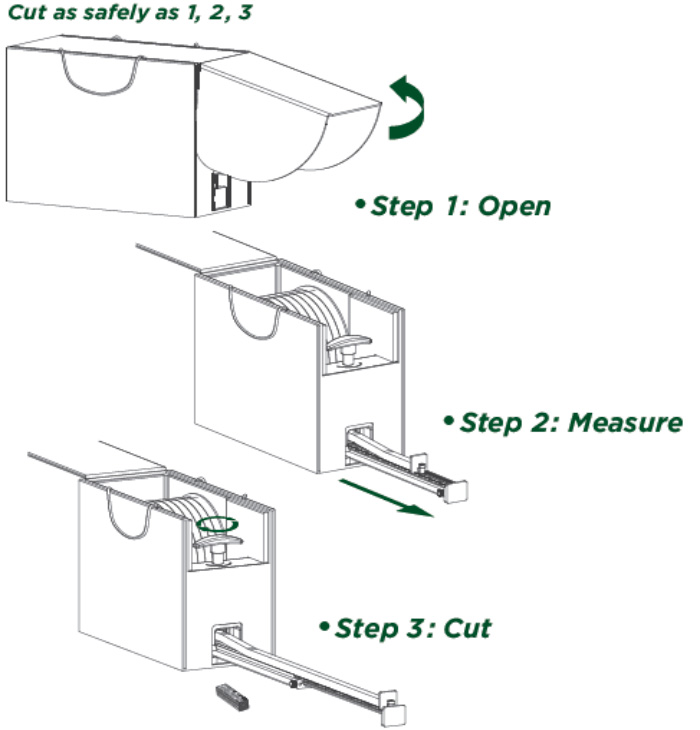