A top U.S. pulp and paper plant in the forest products industry recently faced an extended, unplanned shutdown due to improperly designed pump couplings installed in a paper machine. The plant installed a new paper machine that was failing to start due to its use of improperly designed couplings, rendering the mission-critical machine inoperable. Once the problem was identified, the manufacturer required more than one week to turn around design and installation of new couplings to get the paper machine running. This would incur substantial revenue loss and unplanned downtime. Potential production losses of market pulp, tissue, wood products, newsprint and specialty papers were significant, estimated at $500,000 in revenue loss per day and more than $2.5 million in revenue loss per week.
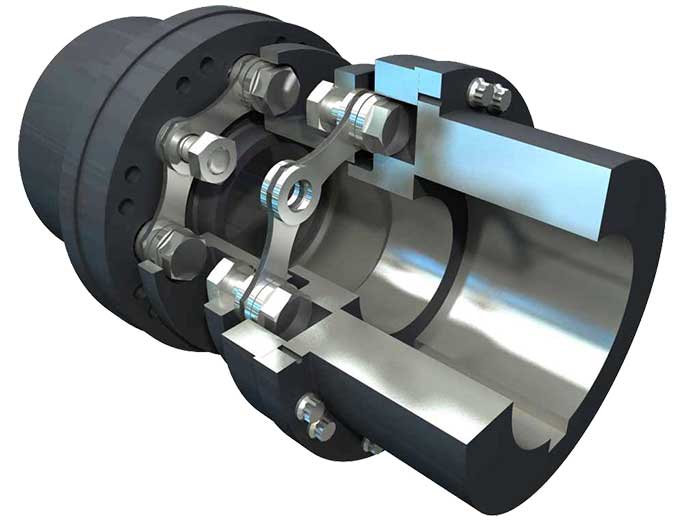