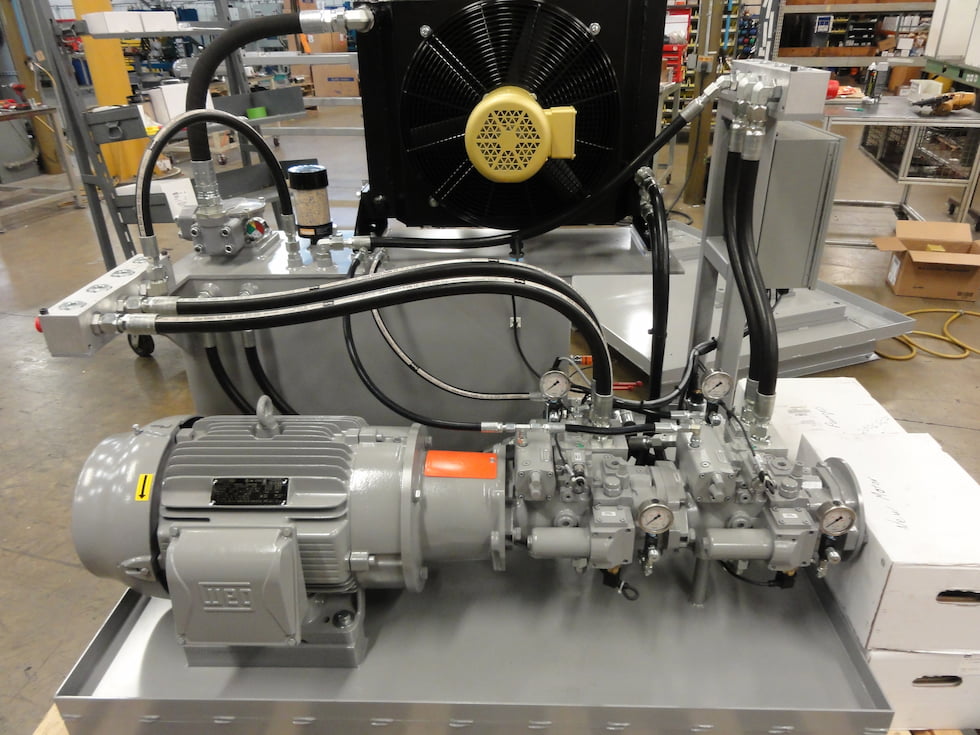
Adaptability has been the theme of the last year. A global pandemic really makes everything look different. To survive, and even thrive, a company needs to be able to adapt, pivoting on a dime when needed.
This is the case, too, for many older manufacturing plants that contain older machines and equipment, many from the 1950s and earlier. When it is too costly to completely overhaul an entire plant, but the machines can no longer be repaired in the traditional manner or fail to run efficiently, aftermarket solutions come into play.
According to the Merriam-Webster dictionary, the term aftermarket is the market for parts and accessories used in the repair or enhancement of a product. Aftermarket solutions are many times a direct result of a third-party vendor that has found an answer to a problem that companies are facing every day, and pumps are often a piece of an aftermarket solution.
Finding a Solution
When a large consumer lawn and garden manufacturing company experienced an out-of-order press on its stamping line, they were told replacement parts would take roughly eight weeks to arrive. Eight weeks would have cost the company thousands of dollars and resulted in downtime that could be detrimental to their production line. But what other choice did the company have? They needed to get the pump repaired. This is where third-party engineers and the aftermarket space comes in.
An engineer was able to look at the broken pump and see that there was another answer to the problem. He was able to source parts for an expedited repair and suggest potential replacements of newer pump technology. Together, these solutions could provide improved availability to make the machine run faster, more efficiently and with an increased output.
The updated technology the engineer offered was pumps with proportional control. Proportional control valves allow pumps to work at only the level necessary —instead of only being in an on or off setting. This proportional control acts almost as a dimmer on a light switch, allowing the user to control how much output the pump is putting into the system.
Proportional control is a cost-saving measure. Companies can spend less in energy, and because the pump and valve do not need to be continuously running at full speed, there is less wear and tear on the devices. This can save a company money on machine maintenance and repairs as well. The lawn and garden manufacturing company upgraded numerous pumps on the plant floor with this technology, improving output exponentially.
Aftermarket Uses for the Future
Aftermarket solutions continue to retrofit older machines and broken mobile systems, but they are taking a new approach with the internet of things (IoT) and smart technology. This technology is still in the early stages, but it is impacting the pump industry and helping manufacturers and machine operators improve process, eliminate downtime and even get ahead of preventative maintenance.
IoT technology is integrated with the pump installed on a machine. That IoT pump technology documents everything the pump does through operational sensors and a fully connected, predictive analysis engine. A plant floor engineer is able to read each IoT-fitted pump and see the condition on day zero, or the first day it was installed, and on day 234, for example.
The pump can even alert a user if there is a problem or if something is off. This allows plant floor employees to correct the problem before an entire machine breaks and downtime is required.
Some of the ways this technology can help shorten downtime:
- proactive responses: predicting pump failures before they happen
- efficient repairs: spending less time diagnosing problems and more time fixing the specific issue
- right parts at the right time: knowing what needs to be replaced and having OEM parts delivered prior to assembly, speeding up the downtime process
Getting a read on the life span of the pump can help a plant engineer stay on top of regular maintenance because they know how long the first pump lasted and can plan for the estimated length of time that a replacement pump will last.
Many of these IoT-synchronized pumps are connected using the latest technologies, including Wi-Fi or Bluetooth. This allows technicians to connect from virtually anywhere to monitor a pump on a machine.
Partnering With Third Parties for Aftermarket Needs
Many companies will have a need for an aftermarket part at some point. A company can benefit from working with a third-party vendor for aftermarket needs, resulting in the company expanding its network.
Why is having an expansive network important? The answer is simple. Developing a broad network of different vendors allows a company to have access to different aftermarket repair parts.
Machines can get back up and running in a shorter amount of time when companies work with a diverse group of vendors, all with different aftermarket products at the ready. It is a similar strategy to the well-known saying “two heads are better than one.” It is always a smart strategy for a company to have a diverse number of resources to help when something goes wrong.
The aftermarket industry has strong staying power. The need to find solutions to problems will never cease to exist. And, with continued adaptation to current trends in technology, it will only continue to add value for companies.