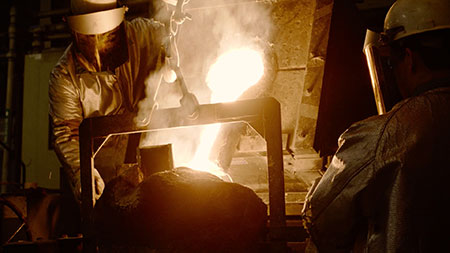
Repairing critical pieces of equipment can be a time-consuming task, especially if they have been in service for a long time and original parts are difficult to source. One solution for a fast repair is to give the challenge to a specialist parts manufacturer, which can reengineer new parts for a wide range of rotating equipment. OEMs will always do their best to provide a comprehensive array of spare parts for their products. However, after decades in service, it may not be possible to deliver this level of support. The manufacturer may have been acquired by another entity or ceased trading altogether.
Whatever the cause, the requirement for replacement parts remains, and when larger pieces of equipment are involved, their role is often more critical.
The Latest Technology
When creating new parts for crucial pieces of equipment, speed is of the essence to avoid costly downtime. Using the latest generation of laser scanner enables engineers to gather 1.3 million points of data every second, and 11 intersecting laser lines ensure even the most complex geometry is captured accurately. This type of scanner outputs a high-definition mesh geometry that can be imported into 3D computer-aided design (CAD) software.
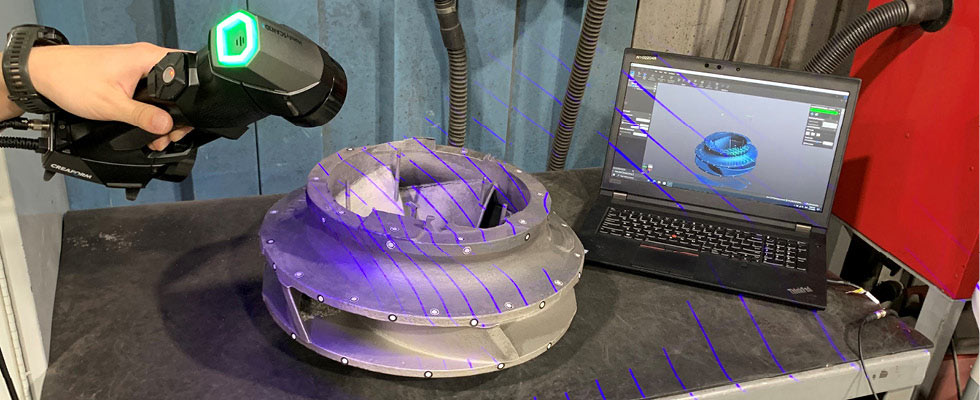
Precision data acquisition allows dimensions to be repeated within 0.001 inch. (0.025 millimeter) (Images courtesy of Sulzer)
Fine-Tuning the Design
Having acquired the basic dimensional data for a project, engineers can fine-tune the design of the new component. Adjusting machine stock, integrating wear rings and upgrading hydraulics to make pumps more efficient are a few changes that can be made. In this way, it is possible to make alterations to the original design to account for changes in the application.
After scanning is complete and the 3D models are created, these components are stored in a digital inventory. This allows engineers to have a database of digital artifacts that can be referenced at any time. With this digital stock-holding, various avenues may be pursued using different additive manufacturing techniques.
Modern Casting Methods
Traditionally, casting a new component involved creating a wooden pattern of the original and putting it into a sand-casting box. This is a lengthy process and subject to considerable inaccuracies, especially if the wooden molds are stored for any length of time and become distorted. As part of the modern process to create a digital mold, the first step is for design engineers to create a rigging and gating system to adequately sustain the initial flow of molten metal all the way to the final solidification of the part. The design is based on numerous calculations that allow the engineers to create these complex systems.
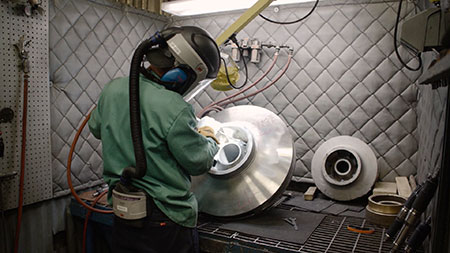
Specialist cleaning and polishing equipment
From here, an analysis is performed to predict the flow and solidification of the molten metal within the designed system. The design engineers then have an expected outcome and can deem the system acceptable or not, based on their acceptance criteria. The next step is to create the mold using 3D CAD software. The rigging and gating system will be derived out of the cope and drag to get the proper replication of the designed systems. From there, the individual pieces of the molds are exported for further processing.
Exported files are then sent to a 3D sand printer that uses the data to gradually build a mold of the new component. Using layers of sand and adhesive, the 3D printer creates a mold that can withstand the high temperatures of the molten metal that will form the new component.
Retrieving the Data
A foundry is central to creating new parts and pouring numerous different alloys for castings. The exact make-up of the metal alloy is determined by the component and its application.
Having been poured, the cast component is then returned to the engineering group, where a 3D scanner is used to retrieve data from the casting. It is overlayed with the original 3D model to verify there is enough stock to create the final machined product. Once this verification step is completed, the part is returned to production for final processing.