Valve and pump packing performance improvement is usually approached from a procedure or specification process. Engineering and purchasing determine the parameters for the plant and create a procedure for selecting the packing type and how it is used. At many plants, this document is not often referenced or updated. Also, this process does not involve many stakeholders and is often one direction (top down). As a result, this process can make the procedure thin and leave out important packing fundamentals details. This can lead to plants that rely on misleading and potentially incorrect information or word-of-mouth information. This affects the success of packing performance. A better method is to use the continuous improvement process illustrated in Figure 1 to target improved packing performance.
The Costs of Poor Packing Life
Many plants do not understand the total costs associated with poor packing life. By analyzing the mean time between failure (MTBF) for critical valves and pumps and applying overall life-cycle cost models, large savings can be achieved through improved performance. In many situations, short packing life can cause a pump or valve to have a significant impact on plant production output and cost.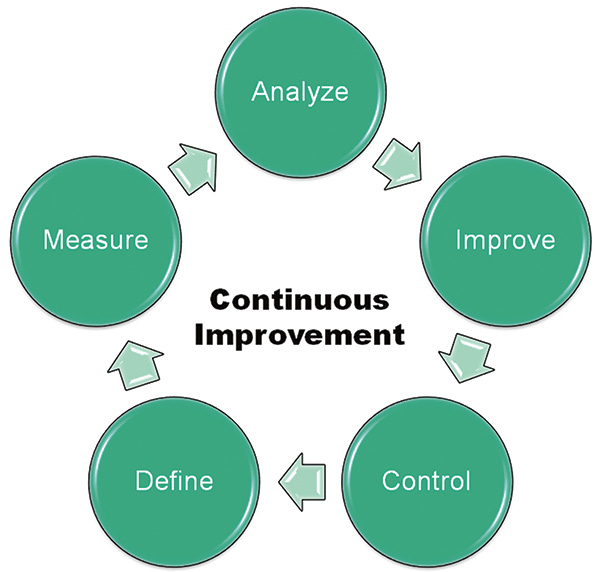
Collect & Analyze Used Packing
One of the fundamentals of continuous improvement is gathering and analyzing data. For packing improvement, a best practice is to gather packing removed from equipment, taking into consideration the appropriate safety and decontamination procedures. Examining this packing can help determine what happened during its service life. In most plants, used packing is destroyed. Because the causes for failure and damage were not analyzed, mistakes are repeated. A good maintenance practice is to use a zipped plastic bag to collect used packing with a few basic pieces of information—the date removed, who removed it and the equipment identification number. Photos of any damage to the equipment (for example, valve stem or pump sleeve damage) are also important data. In some plants, cameras are not allowed for security reasons. However, having an accurate image of the valve’s or pump’s condition is useful for improving performance. Stem corrosion can be linked to overall valve packing performance but needs to be noted and corrected. A picture of the damage can assist in prioritizing the repair and help make packing choices that reduce galvanic corrosion.Cross Functional Team Review
The stakeholders of this cross functional team must be connected directly with packing performance. Some stakeholders who should be considered are maintenance, engineering, operations and management. The reason to focus on a cross functional team is to make sure that all stakeholders are part of the solution. For example, operations can rely on how the packing performs and without their involvement their packing adjustments practices could jeopardize overall plant performance. Also, the packing supplier can help identify the root causes of problems and suggest best practices. One of the main action items for this team is to review and examine the bagged packing and categorize the root cause of the failure modes, which may include:- Poorly cut packing rings
- Packing extrusion
- Chemically attacked packing
- Solids embedment (pump packing)
- Wrong packing selection
- Poor packing consolidation
Updating Packing Procedures and Training
To have a robust packing program, the team should ensure that packing procedures are listed in a “living” document. It should be updated and contain detailed information. For example, when reviewing packing failures, a trend is noticed in the blossoming/fraying of the cut ends that leads to a leak path and a shortened MTBF. This would prompt the group to include a section in the procedure about using the correct technique to cut the packing, such as using a sharp knife. Another example is a trend that pump packing removed from above the lantern ring shows signs of solid embedment. Determining the root cause of this failure type could open discussions that include:- The cleanliness of the flush media
- Lantern ring location
- Using an advanced solids management technology