Finding an efficient, cost-effective, low maintenance system to increase dissolved oxygen levels in wastewater is not always easy. Or is it? It is as simple as a pump, a venturi injector and nozzles—a venturi aeration system. The pumped water enters the injector inlet and is constricted, creating a vacuum. This enables air to be drawn in and become entrained into the water stream. The mixing nozzles downstream of the injector impart additional mixing by shearing the coalesced gas and creating micro-bubbles, allowing the rest of the gas to mix into the solution. By the time the gas or water solution leaves the nozzle, it is like a cloud of mist filled with tiny bubbles resulting in effective mixing and contacting. The pump and injector are installed outside of the basin or lagoon for easy maintenance. The injector’s lack of small orifices or sharp edges make them ideal in handling high concentrations of solids with no concerns of plugging. The simplicity of the physics behind the venturi aeration process belies the importance of a precise design. Because the system does not rely on increased horsepower to overcome gas transfer challenges, venturi aeration should be carefully analyzed using computational fluid dynamics (CFD) modeling to ensure optimum sizing and placement of each injector and nozzle in order to facilitate complete mixing with minimal energy use. Pump horsepower, pipe diameters and oxygen transfer rates are set based on the volume and profile of the basin or lagoon as well as the biochemical targets for the system. For instance, a facility eager to reduce biochemical oxygen demand (BOD) in its wastewater lagoon may use a larger pump and more nozzles to maximize gas transfer, while a plant just trying to eliminate odor complaints may be able to succeed with fewer injectors and less oxygen. Discharge standards, downstream treatment processes or re-use targets for treated wastewater can also guide aeration system specifications. CFD ensures optimum flow and reduces costs associated with extra pumping or cavitation that can result from turbulence. CFD analysis can also pinpoint the optimum placement for measurement sensors to obtain the most accurate readings of the system’s performance. An accurate CFD analysis provides insight and confidence that a design is optimal for the actual physical and chemical processes it was designed to achieve. As water-quality standards become more rigorous, it becomes paramount for companies and utilities to ensure proper mixing and reliable measurement.
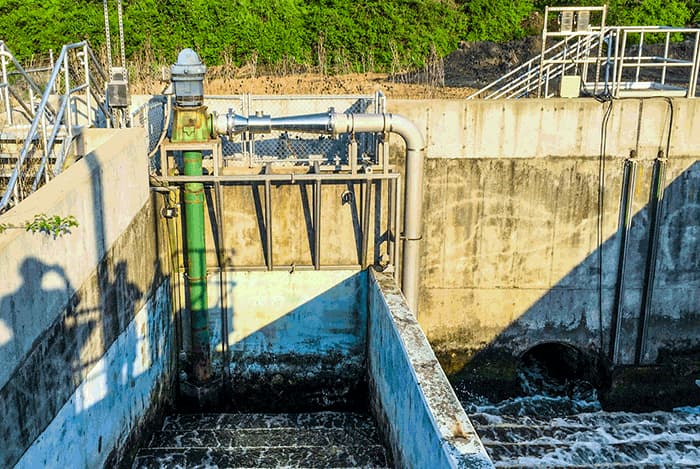
Case Study 1
A municipal wastewater treatment plant in Ohio must meet dissolved oxygen levels at their outfall. During normal operations, dissolved oxygen increase is accomplished in a cascade basin, but during storms the river can rise to levels that flood the cascade basin rendering it useless. Due to the confined space in the cascade basin and limited access to the site, a drop-in system incorporating a pump, a venturi injector and a nozzle manifold was adopted, eliminating the need for blowers or diffusers—and the footprint and maintenance they require. Soon after implementation of the system, a storm caused the river to rise, flooding the cascade basin. The new system easily met and maintained the outfall dissolved oxygen requirement and continues to do so today.Case Study 2
For pure oxygen injection into an activated sludge system, a textile manufacturer in Brazil installed a venturi aeration system for wastewater treatment in 2011. The system consists of pumps, stainless steel injectors and a nozzle manifold. The pumps deliver pressurized flow to the venturi injectors, drawing oxygen gas to the injectors and mixing with the motive flow. The mixed flow is then sent to the nozzle manifold inside the basin for additional mixing and contacting of the oxygen with the sludge. The manufacturer was so pleased with the effectiveness, efficiency and low maintenance required with this venturi aeration system that, in 2015, it installed an additional unit at another facility.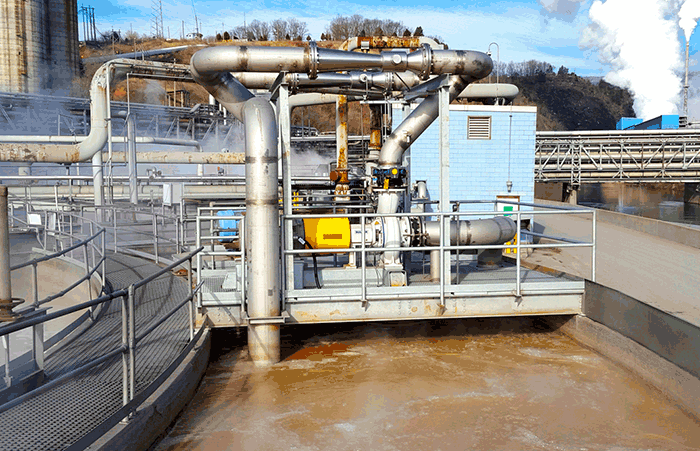
Venturi Benefits
Venturi aeration systems also work well in other industries that generate wastewater with high-solids concentrations such as pulp and paper and dairy industries. Venturi wastewater aeration delivers dissolved air/oxygen from the bottom up for complete aeration. The efficiency of the system increases with depth, allowing for deeper basins or lagoons with smaller footprints. The most powerful surface aerators can only push oxygen about six feet deep; after all, they are fighting the physics of bubbles that naturally float to the surface.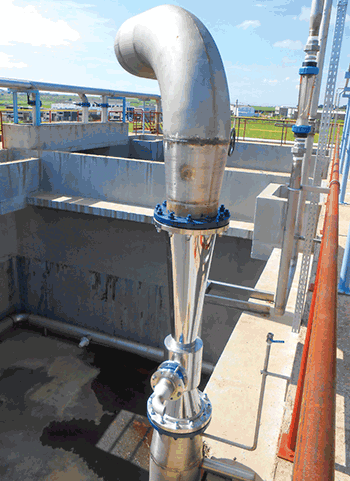