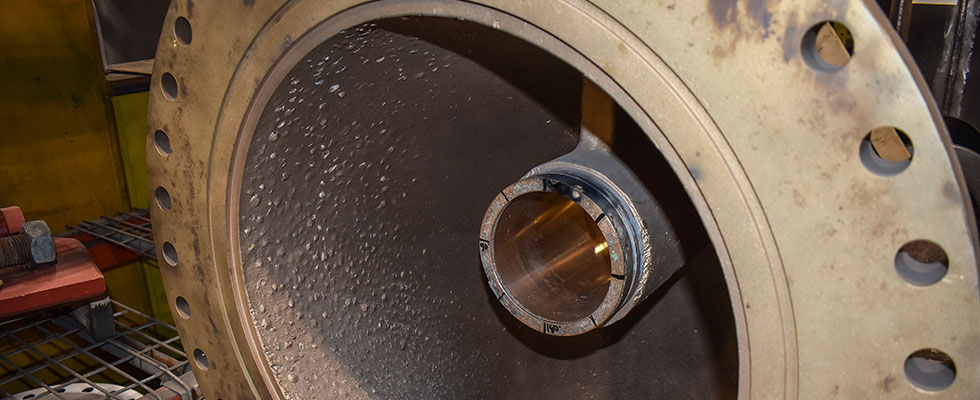
The average age of the U.S. nuclear reactor fleet is 39 years old [1] and many plants are forecast to continue operating for years to come. Many nuclear pumps, especially those in aggressive services, are now at or beyond their original design life and experiencing degradation that is difficult to repair during routine maintenance. In the case of service and circulating water pumps, particularly those in seawater or brackish waters, recent experience has shown worse than expected levels of corrosion. This not only poses a challenge in the repair of pumps, but also brings into question the integrity of the main pressure boundary components, especially during or after seismic events.
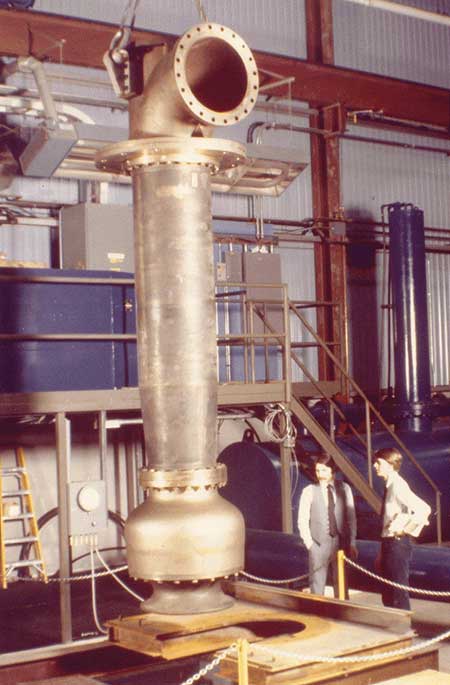
Both service water and circulating water applications typically use large vertical turbine or axial mixed flow pumps (Hydraulic Institute VS1 or VS3) to circulate water from nearby estuaries, rivers, or reservoirs for cooling of plant components. Service water and/or essential service water systems are critical to plant operation and their ability to safely shut down in “design basis event” scenarios. Circulating water systems are not considered “safety related,” however still provide a vital role in the operation of a nuclear power plant. Unplanned repairs and complications during routine maintenance due to corrosion are costly and detrimental to plant operation.
For many U.S. plants, the main cooling water sources are seawater and/or brackish water which constitute harsh service conditions for pumps and piping systems. In addition to the natural salinity, it is likely that water quality and microbiological activity have changed since equipment was originally installed due to human factors such as nitrogenous runoff from ammonia fertilizer use. Water quality issues and increased microbiological activity are known contributors to degradation of aging pumps and plant equipment.
Original Materials of Construction
Service Water Pumps
Many pumps in service water and related applications were originally constructed using aluminum bronze to withstand the demanding service conditions. Aluminum bronze alloys have excellent wear, galling, and corrosion resistant characteristics while providing high strength. When compared with other readily available corrosion resistant alloys such as austenitic stainless steels, selection of higher strength aluminum bronzes often allowed for reduced material thicknesses and lower overall costs for vertical pump applications. These pumps typically consist of large castings and fabricated components where appreciable savings could be realized. Selection of aluminum bronze also offered enhanced seawater corrosion resistance and resistance to biofouling compared with many similarly priced alloys at the time of original construction.
For service water applications, highly alloyed, two phase (duplex) aluminum bronzes, such as alloy C95400, were commonly employed. These alloys contain between 8% and 11% aluminum which results in higher strength due to formation of a hard, body-centered cubic “beta” phase in the microstructure upon fast cooling. Other alloying elements such as iron and nickel further increase strength and corrosion resistance. Despite their desirable physical and mechanical properties, these alloys can become susceptible to a form of selective phase corrosion known as dealuminification due to their inherent two-phase microstructure.
Circulating Water Pumps
For circulating water applications, the materials of construction for major castings were commonly specified as grey cast irons such as American Society of Testing and Materials (ASTM) A48 CL30 and ASTM A278 CL30. Cast irons provide reasonable mechanical strength at a low cost, making them practical for very large components. However, grey cast irons are subject to selective phase corrosion know as graphitic corrosion. In some cases, austenitic cast irons such as ASTM A436 Type 2 were employed to mitigate corrosion and erosion in service. Austenitic cast irons are commonly referred to as Ni-Resist, and include nickel and chromium additions for improved toughness, corrosion resistance and wear properties over grey cast iron.
Selective Phase Corrosion
Selective phase corrosion, otherwise known as selective leaching or dealloying, is a corrosion mechanism found in certain alloys which have a difference in nobility (electrochemical potential) between phases or elements within their microstructure. The less noble phases of the alloy are susceptible to preferential corrosion resulting in dissolution of certain elements from the alloy. The selective corrosion of the more active phase(s) leaves behind a porous material with reduced tensile strength and ductility. Put simply, certain elements corrode out of the microstructure leaving behind voids in the material lowering its overall strength.
The Nuclear Regulatory Commission (NRC) is aware of selective phase corrosion issues (particularly graphitic corrosion and dealuminification) in plants and has addressed them among other mandatory requirements for plant life extension in NRC document “Generic Aging Lessons Learned (GALL) Report- NUREG 1801.” In support of this guidance the Electric Power Research Institute (EPRI) has released several papers such as “EPRI Report 3002008013: Assessment of Available Nondestructive Evaluation Techniques for Selective Leaching; Technology Review” and “EPRI Report 3002013168: Nondestructive Evaluation: Guidance for Conducting Ultrasonic Examinations for the Detection of Selective Leaching” to aid in inspection and detection of these issues. All sites have a documented plan for addressing selective leaching concerns which often includes options for cathodic protection systems and coating regimes; however, given the age of in-service equipment, selective phase corrosion can still manifest into issues.
Dealuminification
In the case of aluminum bronze, selective phase corrosion takes the form of dealuminification, characterized by selective leaching of aluminum from the metal. Dealuminification is attributed to formation of an electrolytic cell between the copper-rich alpha phase and the aluminum-rich beta or gamma 2 phases in duplex alloys; the less noble aluminum-rich phase corrodes.
Typically, the components susceptible to dealuminfication are those with a continuous or semi-continuous network of gamma 2 phase, which has a higher likelihood of corrosion than the beta phase. The gamma 2 phase is formed upon slow cooling through the temperature range of approximately 1100 – 1000 F. Adequate heat treatment processes during material manufacture and after weld repairs can promote beta formation and limit formation of gamma 2. Solution treatment followed by annealing or tempering is commonly employed to promote a microstructure with less susceptibility to selective phase corrosion.
Castings and Weldments
Dealuminification is most prevalent in cast aluminum bronze components with prolonged exposure to saltwater environments. Cast components in large vertical pumps typically include impellers, diffusers, suctions bowls, and discharge elbows. When compared to other material forms, castings and weldments present a higher likelihood that slow cooling has occurred during the manufacturing process, allowing formation of gamma 2. The larger and less refined grain structure in castings also contributes to susceptibility and increases probability of a continuous network of gamma 2. One issue is that some aluminum bronze casting specifications such as ASME SB148 C95400 include provisions for heat treatment to improve corrosion resistance and strength, but do not explicitly require it. Careful review of material specifications and proper prescription of heat treatment and cooling rates is critical to reducing probability of dealloying for highly alloyed aluminum bronze castings and weldments.
Graphitic Corrosion
Similar to dealuminification, graphitic corrosion is the selective leaching of iron from cast irons. The iron selectively corrodes while the continuous graphite flake remains intact. The mechanism is similar to dealuminifcation in aluminum bronze and is a form of selective phase corrosion: a difference in electrochemical potential creates a corrosion cell between the anodic iron and cathodic graphite, promoting preferential attack of the iron. Graphitic corrosion has been identified as an issue for buried cast iron piping but is also a concern for any grey cast iron components actively submerged in an electrolyte, such as seawater.
Microbiological Induced Corrosion (MIC) and Dealloying
Experience has shown that dealloying can be more pervasive when coupled with microbiological induced corrosion (MIC) in seawater and brackish water environments. MIC designates corrosion caused or accelerated by the presence of microorganisms; microbiological activity can both increase corrosion rates and modify corrosion mechanisms entirely. When comparing current plant conditions to conditions at commissioning, it is possible that changes in water chemistry, namely heightened nitrogen levels from increased use of ammonia fertilizers over the past 40 years, are increasing microbiological activity and MIC in water bodies and estuaries used for plant cooling water.
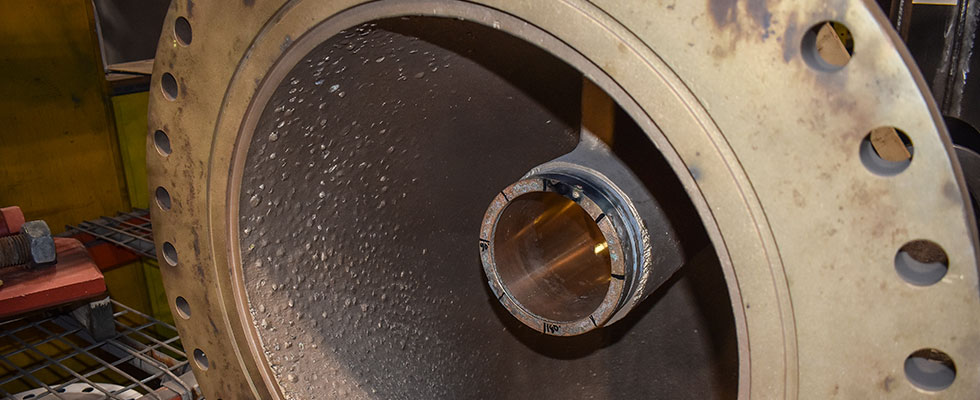
Diagnosis
The U.S. NRC document NUREG-1801 Generic Aging Lessons Learned (GALL) addresses selective leaching under section XI.M33. For identification and diagnosis of selective leaching, this document recommends a one-time visual inspection coupled with hardness testing or mechanical evaluation techniques [4].
Selective leaching can be difficult to identify by visual inspection alone as it often does not cause dimensional changes along with the changes in microstructure and reduction in tensile strength. However, more severe dealuminification can manifest macroscopically as dark, copper-colored areas on the metal’s surface. The use of acid etching can also aid in identification by visual inspection. Dealloying can be more conclusively identified by destructive testing, but this is not often possible for diagnosis of in-service equipment. It should be noted that selective leaching may be localized, and therefore taking a range of representative samples from different areas is recommended if destructive testing is employed.
Ultrasonic Testing
Various industry bodies and independent organizations have reviewed the merits of ultrasonic inspection methods for de-alloying, such as normal-beam ultrasonic, phased array ultrasonics and time-of-flight diffraction (TOFD). The most common ultrasonic testing method employed is TOFD, which typically requires taking material samples for examination. This method requires accurate measurement of material thickness in order to verify the results of inspection.
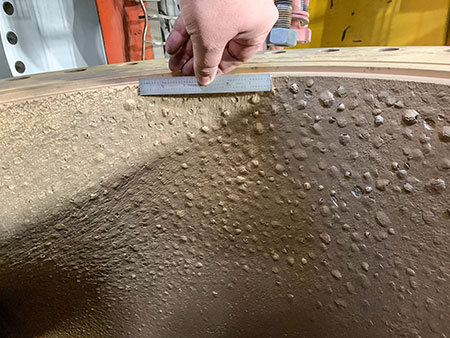
Microscopic Examination
In addition to identification of existing dealloying, another option is to test for general susceptibility to de-alloying via microscopic etch testing. This testing is commonly performed on representative material samples upon procurement of the pump components but could also be performed during service of existing equipment. Using a nitric acid or dilute ferric nitrate etchant and magnification, the aluminum bronze microstructure is examined for diagnosis of susceptibility. A continuous network of eutectoid (alpha + gamma 2) microstructure indicates susceptibility to dealuminification, while the lack of a continuous eutectoid network and the presence of martensitic beta phase indicate lower risk.
Pressure Testing
An alternative method that has been used on large vertical pumps is to perform an extended, low pressure hydrotest of individual pressure retaining components. This method can be useful to detect if there is a continuous network of dealloying through the thickness of the component pressure boundary. A pressure indicator can be used to monitor the pressure inside the components and the outside surface can be monitored over a set period (typically a few days) to identify any seepage through the material. This is an absolute way to determine the components’ ability to retain pressure, but it should be noted that this method will only detect cases of continuous dealloying through the wall thickness. Components that pass this test may still have some degree of dealloying throughout their structure which could compromise part integrity.
Repairs
Performing repairs on dealloyed components becomes difficult as the corrosion mechanism progresses. Due to the porous structure and altered alloy composition in de-alloyed areas, welding tends to collapse the existing base material making it difficult to achieve adequate buildup; weld integrity is also questionable due to the difference in composition between the filler metal and leached base material. Biological residue and corrosion byproducts can manifest in and underneath the porous base metal, creating impurities in the small pockets and voids. These impurities further complicate achieving adequate weld repairs.
These complications can be a major issue when servicing affected pumps as they can cause unexpected delays in the repair, or inability to repair altogether. To successfully weld repair in these areas requires grinding to sound metal. In severe cases this may not be achievable as there is no sound material left to grind back to in the corroded area. Inability to achieve a sound weld repair generally leaves complete component replacement as the only practical option.
Material Upgrades for Prevention
U.S. NRC document NUREG-1801 section XI.M33 does not provide guidance on preventative action, however it does note that monitoring of water quality to control pH, concentration of corrosive contaminants, and treatment to minimize dissolved oxygen are effective at reducing selective leaching [4].
One of the most effective solutions for prevention of dealloying is implementation of material upgrades. Some nuclear power plants have already opted to replace major castings and fabrications in service water pumps with new materials such as duplex stainless steel, 316 stainless steel and nickel aluminum bronze (Ni-Al-Br).
It is not always necessary to replace all major components of the pump to mitigate issues. Experience has shown that some plants opt to change only the materials below the water line in the sump. These components are subject to the harshest environment as they sit in the intake water for most of their lives and are usually also hydraulic components exposed to high velocity flows that can accelerate corrosion/erosion mechanisms.
Some common material substitutions are discussed below, however this is not an exhaustive list:
Duplex SS (Alloy 2205, CD4MCu, Alloy2507)
Duplex stainless steels are viable alternates for aluminum bronze due to their high strength and high corrosion resistance. Duplex refers to the two-phase microstructure that is part austenite and part ferrite. They have superior strength and corrosion resistance compared to both aluminum bronze and austenitic stainless steels. Duplex stainless alloys are also highly resistant to chloride stress corrosion cracking and pitting, making them suitable for brackish water and seawater applications. CD4MCu (alloy 1A) is the most commonly specified cast form of duplex stainless steel and has been applied successfully in certain brackish service water applications.
Super Austenitic SS (UNS S20910 i.e. XM-19, Nitronic 50 etc., UNS S32654 / UNS S31254 i.e. 654/254 SMO etc.)
Super austenitic stainless steels are typically more corrosion resistant than duplex stainless steels, slightly weaker, and are easier to weld however are generally more expensive. They are commonly used in modern vertical pumps in seawater applications. Some of the most common materials in this group that are used in vertical seawater pumps include XM-19 / Nitronic 50 and 254 / 654 SMO.
316 SS
A member of the austenitic stainless steel family, 316 SS is widely used for pumps in corrosive service. It is less corrosion resistant than both duplex stainless steels and super austenitic stainless steels. It is more frequently used in clean water applications, however can be used in brackish or seawater. In brackish or seawater applications, it can be susceptible to crevice corrosion and pitting therefore the water chemistry should be reviewed prior to selection as a replacement material.
Ni-Al-Br (Alloy C95800, C95500)
Nickel aluminum bronze offers additional corrosion resistance over aluminum bronze and is a common material for seawater applications. It has a higher strength and the added nickel content reduces the risk of de-alloying. It is naturally resistant to biofouling and marine growth.
Considerations for Design Code Compliance
For equipment designated as USNRC “safety-related” and those designed and/or stamped according to ASME Section III, there are specific calculations and documentation packages that require updates to document material changes. Examples of documents updated by the pump supplier include the pump design report, seismic analysis, and bill of materials. There are also site-controlled documentation updates required to document the design changes. Depending on the original design code year of construction additional reconciliations may be required. For example, SB148 95800 (Ni-Al-Br) was not included in ASME 1974 edition with winter Addenda 1975 for Section III usage. This may require the site or a designated company to prepare the relief request with the NRC. When choosing a repair facility to work on this equipment, there are benefits working with one who has the capabilities to carry out the detailed design changes as well as the repairs.
Conclusion
Service water and Circulating water pumps are an essential part of nuclear power plants and are critical to plant safety. Many existing pumps are now past their original design life and, in some cases, have begun to present significant levels of corrosion and degradation. Among other types of corrosion, dealloying is a corrosion mechanism of concern due to its ability to progress largely undetected in lieu of targeted examination. The weakened material poses a safety concern in retaining the pressure in the pump which is amplified in the instance of a seismic event. This weakened material could invalidate the seismic analysis of the pump.
Once detected, the mechanisms discussed make it difficult to weld repair affected components, especially large pressure retaining parts, which makes routine maintenance increasingly difficult. Discovery of extensive damage during routine maintenance can lead to major problems for short term maintenance cycles. Affected components are often major pressure boundary castings which have long lead times and can be difficult to replace without proper planning. Consequently, some power plants have opted to replace castings and major components with alternate materials not subject to dealloying concerns. Due to criticality and the age of these pumps, it is essential to have a comprehensive inspection plan on addressing these issues. This allows plants to assess the condition of their installed equipment and plan for any long lead time items, such as castings, prior to scheduled maintenance, helping minimize disruption to outage schedules.
References
- https://www.eia.gov/energyexplained/nuclear/us-nuclear-industry.php
- https://www.copper.org/applications/marine/nickel_al_bronze/pub-222-nickel-al-bronze-guide-engineers.pdf
- https://www.ampcopumps.com/wp-content/uploads/2016/12/WhyNAB_application-series.pdf
- https://www.nrc.gov/docs/ML1034/ML103490041.pdf
- “Non-Destructive Detection of Dealloying in CU-AL using ultrasound”. R. Royer, C. Searfass.