Price, operating costs and reliability are key factors in any TCO calculation.
06/24/2014
Last of two parts.
Part One of this two-part series (Pumps & Systems, May 2014) explained how factors other than initial purchase price work together to generate the total cost of ownership (TCO) for medium-voltage variable frequency drives (VFDs). Part Two discusses what creates high reliability in a medium-voltage VFD.
Drive Innovations Improve Reliability
Some suppliers use a simplified, integrated design that results in a drive with a smaller footprint. A traditional drive can have up to five separate components: harmonic filter, power factor correction components, transformer, power converter and motor output filter (see Figure 1). An integrated design drive, however, only has two components, an isolation transformer and a power converter. To achieve an integrated design, the drive must be high-performance so that, unlike a non-integrated design, additional components are not required. For example, the design for advanced drives has progressed to more levels at the output and these multilevel topologies extend motor life, which is stressed by the lower level counts that a less expensive drive may offer. Output filtering is not required. These filters add components and assemblies, but they are rarely considered when calculating the reliability of drives that focus on converter part count only. The simplicity of an integrated design results in a more straightforward system with fewer components, which increases reliability and reduces downtime.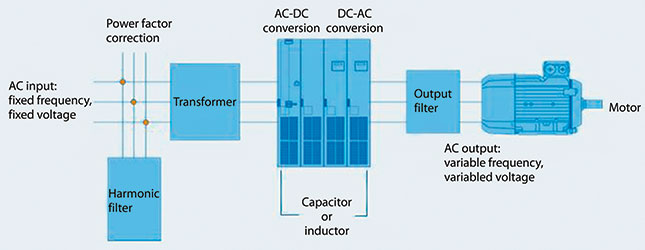