The company faced flooding problems, and its existing pumps were old, with many of them out of operation.
MZT PUMPI
09/21/2016
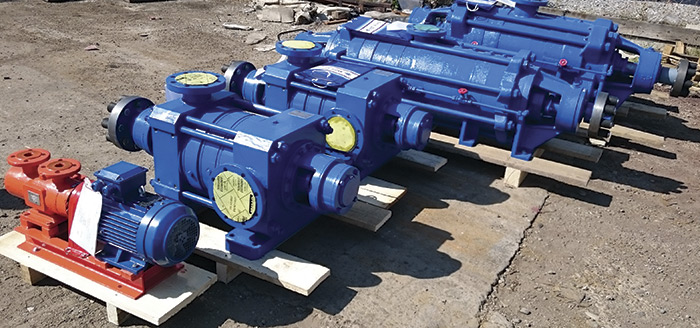
Tomi Ognjanovski is head of the engineering and development department, as well as pump designer and project manager, for MZT PUMPI A.D. in Skopje, Macedonia. Ognjanovski has a Bachelor of Science in mechanical engineering. For more information, visit pumpi.com.mk.