Choose appropriate wetted end materials and a solid motor.
Madden Manufacturing Inc.
09/27/2018
The process of chemical metering requires the injection of the chemical(s) at a consistent, finite and accurate flow rate. As a result, chemical injection applications require significant planning and consideration, often accounting for the following:
- What concentration level of chemical will be used/is available?
- How much should be dosed into the process to achieve the desired outcome?
- What is the operating pressure to be overcome by the chemical injector?
- What materials are necessary to handle the chemical?
- Will this be installed at a hazardous site? Does it require a special motor?
- Will any ancillary equipment be vital to this process, allowing the metering pump to dose accurately and with repeatable output?
Sizing the Chemical Metering Pump
The more information available about the chemical dosing application, specifically about the chemical itself, the easier it is to choose the capacity of the diaphragm metering pump. Concentration levels of the chemical, specific gravity, viscosity and pH are a few of the factors that can affect the pump’s flow rate. Whether the chemical process injects a flow rate at a percentage of the process flow rate or injects a finite amount into a stagnate process, understanding the chemical’s make up is a crucial piece of the operation. Often, chemical-focused companies and chemical engineers are the best place to start when confirming the volume of chemical to be dosed into the process. Once sizing the pump is complete, the next step is addressing the operating pressure the chemical metering pump must overcome to inject the chemical into the process.Understanding How Pressure Affects Diaphragm Pump Capacities
It is important to ask the manufacturer what the factory pressure rating is when used to rate their pumps’ capacities. This will help users better understand what to expect when calibrating a pump to the specific application. In the case of diaphragm metering pumps, pressure directly relates to the pump’s output in an inverse manner. If pressure in the application goes up, the pump’s flow rate—while operating at the same motor speed and stroke length—will go down, and vice versa if the pressure goes down.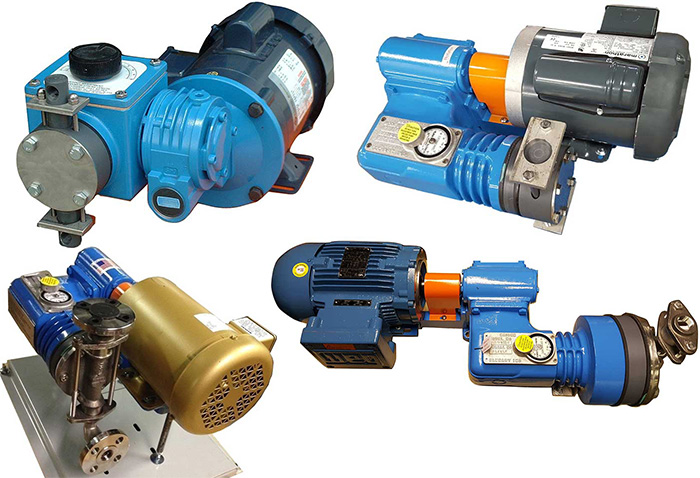
Choosing Proper Pump Wetted End Materials to Handle the Chemical
Most diaphragm metering pump manufacturers offer multiple pump solution head materials, diaphragm materials and valve ball assembly materials to be able to handle chemical injection applications. Some offer more choices than others, so if using an especially corrosive and aggressive chemical, make sure to understand the ratings of each material according to trusted chemical resistance charts. When choosing these materials to be used in the diaphragm pump’s wetted end, review several chemical compatibility or chemical resistance charts to make sure the combination of materials available will not corrode when in contact with the chemical needing to be injected. After noting the materials that will handle the chemical well, the next things to consider are cost, pressure and preference. The cost and preference when reviewing materials often go hand-in-hand during the decision-making process. The desired wetted end and piping for the system may be 316 stainless steel, but polyvinyl chloride (PVC) may work just as well for half the cost. Similarly, a PVC solution head with a Hypalon diaphragm may be adequate to inject the chemical with a reasonable service life, but the more expensive combination of a Teflon solution head with Viton diaphragms would likely hold up to the corrosive chemical for a longer period of time. And then there is everything in between. Talk to the industrial equipment provider or directly to a diaphragm metering pump manufacturer to seek recommendations based on the application. The other factor to keep in mind is pressure. The diaphragm metering pump itself could be rated for higher pressures like 300 to 500 pounds per square inch (psi), but the plastic parts used for the solution head and valve assembly of the pump may not be. Pressures around and above 200 psi can start to become troublesome for PVC valve assemblies, for example. The weaker points in the parts can become prone to cracking when consistently asked to inject chemical into an application operating around 200 psi or higher. For these applications, a metal housing is recommended for the pump’s solution head and valve assembly.Motors & Ancillary Equipment
After sizing and designing the diaphragm metering pump, the last things to consider are the alternating current (AC) or direct current (DC) electric motor (or air-operated motor if required) and ancillary equipment that can be added to the processes line to aid the chemical injection or diaphragm pump. When considering the motor to drive the diaphragm pump, the horsepower (hp) rating will be selected per the manufacturer’s design, but know the preference on single-phase or three-phase power and the type of enclosure needed. Know the environment in which the diaphragm metering pump will dose chemicals to save trouble in the long run. Make sure to check on classifications that need to be met for hazardous environments. As for ancillary equipment, this category could be another article, but here are some common factors to be addressed when chemical metering is involved:- Is there consistent back pressure to inject into at least 20 psi? If not, consider getting a back pressure valve.
- Does the injection need a smooth flow rate with no spikes in pressure or flow? Diaphragm dosing pumps inject in a pulsing manner with each stroke of the diaphragm. If the process line needs this to be a smooth, consistent stream, consider a pulsation dampener.
- Is there any concern that this diaphragm pump could potentially dead head? (Accidents happen. There is almost always a situation where the pump could dead head.) If so, make sure to install a pressure relief valve.